A systematic review of haptic texture reproduction technology
Abstract
This paper provides an overview of the development of haptic texture reproduction technology, focusing on methods such as vibration, ultrasound, and electrostatic systems. It also explores how artificial intelligence (AI) and deep learning contribute to enhancing the adaptability and personalization of tactile feedback. The paper emphasizes the importance of understanding tactile perception mechanisms, particularly the role of Piezo proteins and the interaction between receptors and their microenvironment, in improving feedback system accuracy. Despite technological advancements, the accurate reproduction of fine textures and high-frequency vibrations remains a challenge. The review underscores that interdisciplinary research, including neuroscience, materials science, and AI, is crucial for future advancements in haptic systems.
Keywords
1. INTRODUCTION
Haptic texture reproduction technology has developed rapidly and is now widely applied in fields such as virtual reality (VR), medical rehabilitation, and industrial inspection. Haptic interfaces are capable of generating a variety of sensations, including force, vibration, and temperature, thereby successfully simulating fundamental tactile experiences. However, accurately reproducing textures - such as surface roughness, smoothness, and fine tactile details - remains a central challenge in haptic reproduction. This challenge is particularly evident in the simulation of high-frequency vibrations and complex surface textures. Overcoming these obstacles requires a deeper understanding of the mechanisms underlying tactile perception, which is essential for advancing current technologies.
The core of haptic texture reproduction is the ability to mimic surface textures through physical feedback systems, allowing users to feel and interact with virtual or remote objects. This innovation greatly enhances user immersion by providing more realistic and varied tactile sensations. The significance of texture perception is evident across multiple fields - ranging from enriching entertainment experiences, such as gaming and VR, to aiding rehabilitation therapies and ensuring accurate industrial inspections. However, reliably replicating a broad spectrum of textures - whether smooth, soft, rough, or abrasive - remains one of the greatest challenges for haptic systems.
Currently, haptic texture replication is achieved through techniques such as pulse feedback, electrostatic methods, and ultrasonic technologies. However, these approaches often fall short of capturing the finer texture details and high-frequency vibrations essential for a truly immersive tactile experience. Recent advancements in integrating artificial intelligence (AI) and deep learning algorithms show promise in overcoming these limitations, making contact experiences more personalized and adaptable to various types of textures. Nonetheless, these methodologies remain in the experimental stage, and their full potential has yet to be realized.
This paper provides a comprehensive evaluation of the current state of haptic texture reproduction technology, examining existing strategies, emerging trends, and research gaps that need to be addressed in future studies. It highlights the shift toward smarter, more personalized systems designed to enhance the realism and accuracy of haptic feedback in texture reproduction, thereby pushing the boundaries of immersive tactile experiences.
2. BIBLIOMETRIC ANALYSIS
Haptic texture reproduction technology has rapidly evolved, with significant contributions from neuroscience, materials science, and computer vision[1]. A recent bibliometric analysis of the Web of Science (2010-2024) reveals that AI and deep learning have become pivotal in the development of intelligent, personalized haptic texture reproduction systems, as shown in Figure 1. This marks a shift from traditional mechanical models. Figure 1 illustrates the key interdisciplinary trends in haptic texture reproduction from 2010 to 2024, emphasizing the growing role of AI and deep learning in the development of personalized haptic systems. The integration of neuroscience, materials science, and computer vision has accelerated advancements in tactile sensor technologies and feedback systems, resulting in smarter, more adaptive haptic texture devices. These technologies enhance adaptability, making tactile experiences more responsive to texture perception and individual needs[2].
To more clearly demonstrate the significance of AI and deep learning in the development of haptic perception systems, Figure 2 illustrates trends in the application of AI and deep learning in haptic texture reproduction technology from 2016 to 2024. The chart highlights the increasing number of publications on AI and deep learning, underscoring the growing role of these technologies in enhancing the effectiveness and adaptability of haptic feedback systems. The data reflects the surge in interest and research in these areas, showcasing their pivotal contribution to advancing more personalized and intelligent haptic technologies.
Figure 2. Growth of AI and deep learning in haptic texture reproduction (2016-2024). AI: Artificial intelligence.
The integration of neuroscience has advanced the mechanistic understanding of tactile perception, while developments in materials science, such as nanomaterials and flexible sensors, have significantly enhanced device performance[3]. The fusion of computer vision and haptic technology is also facilitating more immersive multisensory interactions in applications such as virtual and augmented reality.
Edward Adelson’s classification of academic schools of thought highlights that research in haptic technology can be divided into three major factions: the mechanics faction, the perception faction, and the computational faction[4]. The mechanics faction focuses on force sensing and hardware device development, the perception faction emphasizes the modeling and analysis of tactile perception mechanisms, and the computational faction is dedicated to optimizing algorithms and models to enhance the precision and complexity of haptic reproduction. Analyzing highly cited authors reveals the evolving relationships and developments among the major factions in haptic technology research[5].
3. FOUNDATIONAL THEORY
The bibliometric analysis underscores the growing significance of AI in haptic technology. This transition has opened new avenues in the theoretical modeling of tactile perception, which will be discussed in the next section.
Research on haptic texture reproduction involves interdisciplinary collaboration across fields such as perception science, neuroscience, engineering, and materials science. Achieving accurate haptic texture reproduction requires a deep understanding of the fundamental mechanisms of tactile perception and their models, as well as an exploration of the physical and cross-modal factors influencing texture reproduction. This chapter will focus on reviewing models of tactile texture perception, the physical mechanisms of haptic texture reproduction, and recent advancements in cross-modal integration research[6,7].
3.1. Tactile perception mechanism
Tactile perception begins when mechanical stimuli interact with the skin, which consists of multiple layers, including the epidermis and dermis. These layers help transmit and distribute mechanical forces. The skin’s texture, elasticity, and biomechanical properties influence the perception of pressure, vibration, and other stimulation[8]. Mostafavi Yazdi et al. reviewed the skin’s biomechanical properties, highlighting that its non-linearity, viscoelasticity, and anisotropy make its friction behavior complex. These characteristics not only affect the transmission of mechanical stimuli but also determine how the skin responds to various contact conditions, such as compression, bending, and stretching[9].
In driving principles for haptic systems, understanding the biomechanical properties of the skin is essential, especially its anisotropic nature. The skin’s structure, consisting of the epidermis, dermis, and subcutaneous layers, shows varying stiffness, elasticity, and friction depending on the direction and location of the applied force. Many traditional models of haptic feedback assume the skin behaves isotropically, indicating its mechanical properties are the same in all directions. However, recent biomechanical studies have revealed that the skin’s response to force is direction-dependent, implying the skin is anisotropic[10]. This suggests that the stiffness, elasticity, and friction of the skin vary according to the direction and location of the applied force, directly affecting tactile perception. The anisotropy of the skin is a crucial factor in force feedback models, influencing the accuracy of tactile sensations and the realism of simulated textures.
Additionally, the friction between the skin and the object being touched varies across different areas of the skin, further complicating force feedback models. These biological factors must be carefully considered when designing haptic systems intended to replicate real-world tactile sensations, ensuring the feedback models are as accurate and responsive as possible[11].
Tactile receptors, such as Merkel cells, Meissner’s corpuscles, and Pacinian corpuscles, detect specific types of mechanical stimuli. Merkel cells are sensitive to light touch, while Pacinian corpuscles respond to vibration. These receptors convert mechanical energy into neural signals, which are processed by the brain. The efficiency of signal transmission is influenced by the coupling between the receptors and their surrounding microenvironment, including the extracellular matrix and cell membrane dynamics[12].
The discovery of Piezo proteins has significantly advanced our understanding of tactile perception. These mechanosensitive ion channels open in response to mechanical forces, allowing ions to flow into cells and generating action potentials. This process is crucial for transmitting tactile information to the brain. Understanding how these elements interact within the skin’s microstructure is essential for designing realistic haptic systems that replicate human tactile sensations[13].
3.2. Tactile perception modeling
Tactile texture perception models aim to explain how individuals experience surface textures through skin contact. Classical models, such as the Weber-Fechner law, describe the relationship between stimulus intensity and tactile perception; however, they struggle to account for the perception of complex textures, particularly at high frequencies[14].
Dynamic system models, including recurrent neural networks (RNNs), have been introduced to address the limitations of classical theories[15]. These models emphasize the role of tactile memory, allowing for a more accurate representation of temporal changes in perception. Additionally, debates between spectral and spatiotemporal theories highlight the significance of both vibration frequency and the spatial-temporal distribution of stimuli in texture perception[16,17].
3.3. Physical mechanisms of haptic texture feedback
The physical mechanisms of haptic texture reproduction are crucial in determining whether the technology can accurately transmit subtle texture perceptions. Currently, vibration haptic technology, ultrasonic haptic technology, and electrostatic haptic technology are the three most widely studied methods for physical texture reproduction in the research field.
3.3.1. Vibration haptic technology
The mechanical wave interference model of vibration haptics has become one of the most widely adopted physical mechanisms in haptic texture reproduction devices. According to this model, when tactile stimuli are transmitted from the device to the skin, the mechanical waves generated interact with the skin, producing different texture perceptions[18]. This theory effectively explains the tactile sensations transmitted by vibration array devices, such as vibration motor arrays, which can simulate various surface textures. Among haptic feedback technologies, electro-vibration devices are commonly used. However, with advancements in technology, the use of linear motors has gradually gained attention. Compared to traditional devices, linear motors excel at precisely controlling vibration amplitude and frequency, making them particularly well-suited for simulating fine surface textures and enhancing tactile texture feedback.
Figure 3 shows several different cutaneous and kinesthetic feedback devices currently being developed. Both kinesthetic and cutaneous feedback devices have their unique functions in haptic systems. Understanding their strengths and limitations will facilitate the advancement of new technologies.
Figure 3. An example of both cutaneous and kinesthetic feedback devices[19]. (A) hRing, which utilizes skin stretch to provide feedback; (B) TacTiles, which apply pressure using electromagnetic brakes; (C) LucidVR, which uses string-based actuators for tactile sensations; and (D) ExoTen, which employs McKibben-based artificial muscles for kinesthetic feedback[19].
3.3.2. Electrostatic haptic technology
Electrostatic haptic technology generates tactile feedback through the interaction between an electric field and the skin. This technology offers the advantage of non-contact, enabling the simulation of delicate tactile textures without direct skin contact[20]. However, the applicability of electrostatic technology is limited by impedance differences across individual skin types. Particularly in high-precision texture reproduction, optimizing the electrostatic control algorithm to improve stability and accuracy remains a key challenge.
Figure 4 illustrates how tactile sensors fixed on a prosthesis detect touch and pain responses in amputees. The device shown in the figure demonstrates how the tactile sensors perform under different sensory conditions: on the left, the “touch” state shows that the prosthetic sensor detects contact with an external object; in the middle, the “hold” state indicates that the prosthesis maintains its grip on the object via the sensor; on the right, the “pain” state reveals that when the prosthetic sensor detects stimuli resembling pain, the system triggers a “pain reflex” response. The integration of these tactile sensors is essential for enhancing the interactivity and adaptability of prostheses, allowing amputees to more intuitively perceive the characteristics of external objects, better perform tasks, and perceive changes in pain or pressure.
Figure 4. Prosthetic tactile sensor system: touch, hold, and pain response feedback[20].
3.3.3. Ultrasonic haptic technology
Ultrasonic haptic technology generates tactile feedback in the air by focusing ultrasonic waves, enabling non-contact texture reproduction, as shown in Figure 5. This figure illustrates the haptic interface device designed by the team from Southeast University[21]. The advancement of ultrasonic modulation methods is crucial for improving both tactile resolution and penetration, as discussed in the article. The main advantage of ultrasonic haptic technology lies in its deep penetration and multi-point synchronous excitation capabilities[22]. However, certain limitations remain in the penetration depth and precision of ultrasound, especially in reproducing high-frequency textures, where the effective penetration depth is still influenced by skin impedance and surface structure. A key challenge in advancing this technology is how to enhance tactile resolution while maintaining sufficient depth penetration.
Figure 5. The setup of haptic interface device. (A) The structure of system; (B) Ultrasonic phased array; (C) Actuator[21].
3.4. Cross-modal integration in tactile systems
Haptic texture reproduction is not only a singular process of tactile perception but also involves the integration of multisensory information. Research on cross-modal integration has revealed the interaction between visual, auditory, and tactile information, particularly in applications within VR and augmented reality.
In virtual environments, visual information often exerts a strong interference effect on tactile perception. Studies have shown that conflicts between tactile and visual information can lead to distortions in tactile perception[23]. In recent years, to address this issue, researchers such as Boban have proposed optimizing the spatiotemporal synchronization of haptic feedback and the coordination of visual stimuli. For example, through visual-tactile synergistic enhancement technology, the sense of immersion for users in VR has been significantly improved[24].
The phase synchronization mechanism between touch and sound remains an unsolved challenge. Although several electroencephalogram (EEG) studies suggest that coupling tactile and auditory information can enhance texture perception[25], achieving effective integration of touch and sound in dynamic environments remains a key focus for future research. Researchers are exploring emerging technologies, such as neuromorphic computing, to better integrate touch and sound, further enhancing the accuracy and naturalness of tactile feedback[26].
Figure 6 illustrates a bio-inspired crossmodal in-sensor computing system designed for human-machine interaction. Figure 6A depicts the biological network where the sensory and motor cortices are involved in processing sensory feedback through spikes. Figure 6B shows the flexible VO2 memristor-based crossmodal spiking sensory neuron (CSSN) system, which encodes temperature and pressure stimuli into neuronal spikes, enabling real-time haptic feedback and dynamic object recognition[27].
Figure 6. Bio-inspired crossmodal in-sensor computing system. (A) Schematic diagram of the multisensory processing in biological proprioceptive system; (B) Schematic illustration of the spiking crossmodal in-sensor computing system[27].
4. TECHNICAL METHODOLOGIES
Haptic texture reproduction technology encompasses interdisciplinary research across various fields, including hardware design, driving principles, and signal generation algorithms. Despite continuous advancements in related technologies, significant debates persist in the academic community regarding the effectiveness and feasibility of different technical approaches. This chapter will provide a detailed analysis from three perspectives: device morphology, driving principles, and signal generation algorithms, while also addressing the controversies within the academic community surrounding these methods.
4.1. Device morphology: rigid, flexible, and non-contact technologies
Haptic texture reproduction devices can be classified based on their physical morphology into rigid haptic interfaces, flexible haptic devices, and non-contact technologies. Each device type performs differently in terms of application scenarios, texture perception, and user experience. Different academic perspectives have offered various opinions on the advantages and disadvantages of these devices[28,29].
4.1.1. Rigid haptic interfaces
Rigid haptic interfaces, particularly those based on vibration arrays, are widely used in haptic texture reproduction. Studies have shown that when the density of the vibration array is reduced to below 5 mm, the accuracy of texture perception can be significantly improved. However, there is ongoing debate within the academic community regarding the optimal array density. Biswas and Visell suggest that excessively high array densities may lead to increased power consumption and response delays[30], while Pestell and Lepora believe that optimizing the array density can overcome current precision limits[31]. The output force in this context can be defined by
where F represents the output force, N is the number of turns of the coil, I is the current intensity, B is the magnetic field strength, A is the area of the coil, and l is the length of the conductor. This equation demonstrates the relationship between the output force of the electromagnetic drive and several factors[32].
In rigid haptic interfaces, particularly those using vibration arrays, the response time typically ranges from 1 to 5 ms, making them suitable for applications requiring rapid feedback, such as in mobile devices or wearables. These systems offer an accuracy of 80%-90%, making them effective for simulating simpler textures but less accurate for reproducing fine details. Their power consumption is relatively low, usually around 0.5-2 watts, which makes them energy-efficient for smaller devices[33]. However, their scalability is limited, and they are generally more suitable for small-area applications such as mobile phones and wearables.
With the advancement of haptic feedback technology, pen-type devices and fingertip-based texture haptic feedback devices have emerged as prominent research hotspots. These devices not only simulate surface textures through vibration but also adjust vibration parameters based on the characteristics of different textures, allowing for more precise reproduction of diverse tactile experiences. For example, Figure 7 illustrates a rigid haptic interface design featuring a three-degree-of-freedom (DOF) mechanism that provides feedback in the linear, yaw, and pitch directions. Figure 7A shows the overall structure of the device, while Figure 7B highlights the specific motions and axes controlled by the mechanism. This device, commonly used in rigid haptic interfaces, enables precise force feedback by simulating complex movements in a controlled environment. It is designed to enhance the user experience in VR and robotics by providing realistic tactile sensations. The system’s ability to simulate both linear and rotational movements makes it particularly useful for applications requiring high precision, such as object manipulation or surgery simulation[34].
Figure 7. The planar linear haptic interface with modular actuators proposed by the Jeonbuk National University team: (A) the haptic interface and (B) the modular actuators[34].
4.1.2. Flexible haptic devices
The advantage of flexible haptic devices lies in their excellent adaptability and comfort, making them highly applicable in fields such as wearable devices and bionic prosthetics[35,36]. Recent advancements in bionic-inspired flexible strain sensors, such as the bionic stretchable strain sensor (BSSS) inspired by fishbone and nettle fiber structures, have shown promising results in wearable electronics. These sensors, utilizing multi-walled carbon nanotubes and graphene, exhibit exceptional sensitivity, response time, and durability, which are crucial for enhancing the performance of wearable haptic devices[37]. However, the resolution and accuracy of flexible electrodes remain limited in high-frequency texture reproduction. The academic debate centers on the material’s Young’s modulus matching theory. To enhance their response accuracy, researchers have proposed constitutive models to describe the relationship between stress and strain:
where σ represents stress, E is the Young’s modulus, and ε is the strain. One of the main controversies currently centers on how to optimize the material’s rigidity to enhance resolution while maintaining flexibility.
Flexible haptic devices generally have a response time of 10-15 ms, making them suitable for larger-scale applications such as interactive touchscreens and tablet devices. The accuracy of these devices ranges from 90%-95%, offering a more detailed and precise tactile experience. Their power consumption is higher compared to rigid systems, typically ranging from 2-4 watts. However, they excel in scalability, as they are well-suited for large interactive surfaces[30].
Figure 8 illustrates a closed-loop human-machine interface system that provides tactile feedback through a series of actuators. Figure 8A outlines the interaction between the machine, human control, and the tactile feedback system. Figure 8B displays images of an actuator with and without pressure-amplification structures under applied voltage. Figure 8C shows an actuator attached to a finger. Figure 8D illustrates the actuator array integrated with fabric, with close-ups highlighting the actuator’s pressure-amplification structure. Figure 8E demonstrates the actuator’s performance under bending, twisting, and stretching without applied voltage. This system enhances haptic feedback for wearable devices by simulating realistic mechanical deformations[38].
Figure 8. A closed-loop human-machine interface with flexible haptic actuators for wearable devices[38]. (A) Illustration of the closed-loop interface, connecting machine sensing, human control, and haptic feedback; (B) An actuator without pressure-amplification structures shown before (OFF) and after (ON) voltage application; (C) Front and side views of the actuator mounted on a finger; (D) An actuator array integrated with fabric, showing top (left) and bottom (right) views, with inserts detailing the array layout and pressure-amplification structure; (E) The actuator demonstrating mechanical robustness under bending, twisting, and stretching without applied voltage. Scale bars: 2 mm (B), 10 mm (C), 1 mm (D, insert), 3 mm (E).
4.1.3. Non-contact technologies
Non-contact technology has been a research hotspot in recent years, with ultrasonic haptic technology being the primary focus. By utilizing the focusing effect of ultrasonic beams, non-contact devices can create tactile perceptions in mid-air. By adjusting the frequency, amplitude, and waveform of the ultrasonic waves, researchers are able to achieve more precise tactile feedback. Notably, different ultrasonic modulation methods provide additional possibilities for tactile reproduction[39,40].
Non-contact ultrasonic systems generally have a response time of 20-30 ms, which is slower than that of vibration or flexible systems due to the complexity involved in generating and controlling ultrasonic waves. However, they offer high accuracy, achieving around 95% in larger surface applications. Their power consumption is higher, typically ranging from 4-6 watts, and they face scalability limitations due to the difficulty of scaling up ultrasonic feedback for larger areas[33].
The wearable breeze-sense feedback system shown in Figure 9 utilizes thin, flexible breeze-sense generators that generate a gentle, non-contact breeze, mimicking a natural air flow. The system consists of a sandwich-structured device incorporating polytetrafluoroethylene (PTFE) and silver electrodes, which, when activated, produce airflow pressure up to 163 Pa. The breeze generated by these devices stimulates tactile receptors and hair follicle receptors in the skin, providing a realistic non-contact tactile sensation. This system, integrated into wearable devices, offers continuous or sudden breeze feedback for users in VR environments, enhancing immersion and interaction by adding a new layer of haptic feedback[41].
Figure 9. Schematic illustrating a wearable breeze-sense feedback system[41].
A 2022 study proposed that the force resolution of acoustic tweezers has overcome previous technological bottlenecks, achieving higher precision in tactile reproduction[42]. However, a fundamental contradiction exists between the penetration depth and accuracy of ultrasound. Some studies argue that the effective penetration depth of ultrasound cannot be reconciled with tactile precision. To improve penetration power, researchers such as Suzuki have proposed solutions to optimize ultrasonic focusing technology, but whether this approach can overcome the current technical limitations remains a key focus of academic discussion[43].
To summarize the performance of the different haptic technologies:
• Rigid haptic interfaces offer fast response times (1-5 ms) and are energy-efficient (0.5-2 watts) but have limited scalability.
• Flexible devices provide higher accuracy (90%-95%) and better scalability, but their response times (10-
• Non-contact ultrasonic systems provide excellent accuracy (95%) and larger-scale applications, but their response time (20-30 ms) and power consumption (4-6 watts) are comparatively higher.
Table 1 provides a quantitative comparison of these haptic technologies.
Comparison of haptic technologies based on quantitative metrics
Technology | Response time (ms) | Accuracy (%) | Power consumption (W) | Scalability |
Vibration-based | 1-5 | 80-90 | 0.5-2 | Limited |
Flexible devices | 10-15 | 90-95 | 2-4 | High |
Non-contact (ultrasonic) | 20-30 | 95 | 4-6 | Moderate |
4.2. Driving principles: electromagnetic, electroactive, and triboelectric technologies
Haptic texture reproduction relies on various driving principles, including electromagnetic, electroactive polymer, and triboelectric nanogenerator technologies. These driving methods directly influence the precision and diversity of texture feedback[44,45]. Electromagnetic drives are widely used due to their high response speed and precise vibration control. However, they are energy-intensive and may not be suitable for applications requiring low power consumption. In contrast, electroactive polymers offer flexibility but face challenges in response accuracy. Triboelectric nanogenerators are low-power but have limited output energy, restricting their use in large-scale systems. Electroactive polymer drives offer flexibility and adaptability, often used in wearable devices, though challenges remain regarding response accuracy. Triboelectric nanogenerators, while low-power, provide less energy output, limiting their application in large-scale tactile feedback systems[46-48]. Table 2 outlines the core driving principles behind three key technologies - electromagnetic drive, electroactive drive, and triboelectric drive. It highlights the fundamental working mechanisms, advantages, and common applications of each drive, providing a clear overview of how these principles are applied in various fields such as robotics, wearable devices, and haptic feedback systems.
Overview of driving principles
Driving principle | Working principle | Advantages | Typical applications |
Electromagnetic drive | Magnetic field generated by electrical current | Fast response, high precision | Robotics, precision machinery, magnetic levitation |
Electroactive drive | Electrical signals deform electroactive materials | High flexibility, ideal for wearables | Wearable devices, smart skin, bionic robots |
Triboelectric drive | Electric charge generated by friction | Non-contact, low power | Haptic feedback, sensors, micro-robots |
The choice of driving method significantly influences texture reproduction, particularly in simulating high-frequency vibrations and complex textures. The combination and optimization of these technologies enhance the realism and fine-grained detail of tactile feedback, pushing the field toward higher precision and more complex texture representations.
4.3. Signal generation algorithms: from fourier synthesis to neural ODE
Signal generation algorithms are at the core of haptic texture reproduction technology. Traditional Fourier synthesis methods encounter spectral distortion issues when handling complex textures, while recent data-driven generation algorithms, such as haptic generative adversarial networks (Haptic GAN) and neural ordinary differential equations (Neural ODE), have gradually become mainstream. The academic community has extensively discussed the advantages and disadvantages of these algorithms[49]. Table 3 compares three signal generation algorithms - Fourier synthesis methods, Haptic GAN, and Neural ODE - highlighting their core principles, data requirements, control methods, and complexity. It provides a quick overview of each algorithm’s strengths and suitability for different haptic texture rendering applications.
Comparison of signal generation algorithms for haptic texture rendering
Feature | Fourier synthesis methods | Haptic GAN | Neural ODE |
Core principle | Magnetic field generated by electrical current | Fast response, high precision | Robotics, precision machinery, magnetic levitation |
Data requirement | Low | High (large datasets) | Moderate (time-series/dynamic data) |
Generation | Periodic/simple | Highly realistic and diverse | Smooth and continuous |
Control | Direct (frequency, amplitude) | Indirect (latent space) | Fine-grained (initial conditions, dynamics) |
Complexity | Low (real-time) | High (training), moderate (inference) | High (training), moderate (inference) |
Fourier synthesis, one of the earliest methods for generating haptic signals, breaks the signal down into different frequency components to produce haptic feedback. However, this method tends to generate spectral distortion when reproducing complex textures with high precision[50]. The debate in the academic community centers on whether Fourier synthesis can effectively address the multidimensional nature of complex textures and provide sufficiently fine-grained tactile perception.
Haptic GAN, as a data-driven signal generation method, produces higher-quality haptic signals through an adversarial generation process. However, this method faces the problem of mode collapse, where the generated signals lack diversity, resulting in unnatural haptic feedback. There are differing opinions in the academic literature regarding its stability and diversity. Some studies argue that optimizing the training process can resolve the mode collapse issue, while others suggest that the algorithm’s application remains limited[51,52].
Neural ODE is a signal generation method that combines neural networks with ordinary differential equations, capable of simulating dynamically changing haptic signals[53]. Research indicates that Neural ODE offers significant advantages in dynamic modeling and continuous signal generation. However, Docquier pointed out that its training process is complex, and the computational cost is high, which may make it difficult to apply in real-time haptic feedback systems[54]. The central academic debate focuses on whether the neural network structure and training methods can be optimized to reduce computational costs while maintaining high signal generation accuracy[55,56].
5. APPLIED RESEARCH
Research on haptic texture reproduction technology continues to advance across various application fields, particularly in VR, medical rehabilitation, and industrial inspection, where significant progress has been made. Despite the immense potential of these technologies, their practical implementation and real-world effectiveness remain subjects of ongoing academic debate. This chapter will focus on the three main areas of VR, medical rehabilitation, and industrial inspection, offering an in-depth analysis of the technological challenges and academic controversies within these fields.
5.1. VR: immersive interaction and latency challenges
VR has seen significant advancements in haptic texture reproduction, particularly in enhancing user immersion through haptic feedback. One major challenge remains compensating for haptic delays, which can disrupt the user experience. Techniques such as Kalman filtering and long short-term memory (LSTM) models have been explored to mitigate these delays, though both methods have limitations in real-time applications[56,57].
Furthermore, the balance between active touch, where users control interactions, and passive feedback, which reduces cognitive load, is critical for improving VR experiences. Active touch requires more physical effort from the user, which can increase cognitive load, especially in complex virtual environments. In contrast, passive feedback, which involves tactile sensations automatically generated by the system, can reduce user effort. However, it may not provide the comprehensive and immersive interaction required for specific applications, such as tactile exploration or precise manipulation[58-60].
Figure 10 illustrates a VR simulator designed for remote control of machines, as seen in Figure 10A on the left, where a user is interacting with the simulator wearing a VR headset, and Figure 10B shows the real-world scenario of a truck with a crane lifting logs. This setup highlights the impact of latency on the quality of experience in VR, particularly in applications requiring real-time control of machinery. The comparison between the simulated interaction in VR and the physical machine operation emphasizes how latency affects the user’s ability to control and perceive actions accurately[61].
Figure 10. Photo of VR-goggle based crane operation from a remote location. (A) Operator with a VR headset and two joysticks. Operator’s view is shown on the adjacent display; (B) The remotely operated crane[61]. VR: Virtual reality.
5.2. Medical rehabilitation: prosthetic feedback and neuroadaptive mechanisms
In the field of medical rehabilitation, haptic texture reproduction technology is widely applied in prosthetic haptic feedback, transcutaneous electrical nerve stimulation (TENS), and other technologies, with significant progress made in research on neuroadaptive mechanisms[62]. However, considerable debate exists in the academic community regarding the effectiveness and applicability of these technologies. Research on prosthetic haptic feedback has focused on how tactile signals can promote the neuroplasticity of individuals with disabilities, although different studies have yielded inconsistent results. Pasluosta suggests that haptic feedback significantly improves the control accuracy and comfort of prostheses[63], while DJ Weber, in his experiments, pointed out that long-term use of prosthetic feedback might lead to neuroadaptive fatigue, reducing the patient’s sensitivity to tactile feedback[64]. Figure 11 shows a schematic diagram of a prosthesis system equipped with tactile sensors, enabling users to perceive touch and pain responses through feedback, which enhances their ability to interact with external objects and perform tasks more effectively[20].
Figure 11. Schematic diagram of the prosthesis system[20].
TENS, a common rehabilitation technique, simulates haptic feedback by applying electrical currents to the skin. While this technology has yielded positive results in some patients, the primary controversy centers around the control of pain thresholds. The control of current intensity in transcutaneous electrical stimulation presents a challenge: excessive current can cause pain, while insufficient current may not provide adequate tactile feedback. To address this issue, the academic community has proposed several formulas to describe the relationship between current intensity and tactile perception, where the perceptual effect of skin electrical currents can be estimated using
where Istim represents the current intensity, Vstim represents the voltage, and α and β are experimental fitting parameters that describe the nonlinear relationship between current and voltage[65]. The precise adjustment of current intensity and frequency to provide effective and comfortable tactile feedback remains a significant challenge in this field.
Clinical efficacy research is essential for the widespread adoption of haptic feedback technology in the medical field. In recent years, several studies have employed meta-analysis methods to evaluate the clinical efficacy of haptic feedback in prosthetic rehabilitation. However, despite some statistical evidence supporting the positive effects of haptic feedback, many studies have small sample sizes and lack long-term follow-up data, raising concerns about the broader clinical applicability of these technologies[66,67]. Additionally, these studies often lack high-quality control groups and randomized experimental designs, limiting the generalizability of the research findings.
5.3. Industrial inspection: surface roughness and micro-force control
Haptic technology in industrial inspection is primarily used for surface roughness detection and micro-force control[68]. Haptic sensors, particularly those using piezoelectric materials, offer high accuracy in surface texture detection, though their performance can be influenced by complex surface geometries. Thermosensitive sensors are also being explored to enhance accuracy, although their reliability in extreme environments remains a concern[69].
Micro-Newton-level force control algorithms are widely used to ensure precise feedback in industrial settings, but challenges such as error accumulation during repeated tests persist. The effectiveness of multi-finger coordination in improving inspection efficiency, particularly for complex objects, remains a topic of debate and warrants further validation through experimentation[70,71].
6. METHODOLOGICAL CRITIQUE
In the research of haptic texture reproduction, the choice of methodology is critical to the reliability of research outcomes and conclusions. Despite significant progress in haptic reproduction technologies, there remain numerous controversies in areas such as experimental design, theoretical modeling, and emerging research paradigms. This chapter will explore the academic debates within the current field from three perspectives: the crisis of repeatability in experimental design, the limitations of theoretical modeling, and emerging research paradigms. Additionally, the chapter will analyze the potential impact of these debates on future research directions.
6.1. Reproducibility crisis in experimental design
In haptic texture reproduction experiments, the repeatability of experimental design is a key concern due to the complexity of conditions. Skin moisture, which directly affects tactile perception thresholds, plays a critical role. Variations in moisture can lead to deviations in results, yet many studies overlook this factor, affecting the comparability of outcomes[70,71]. The relationship between skin moisture and tactile thresholds is determined by
where Th represents the tactile threshold, H is the skin moisture, and α and β are fitting parameters that describe the exponential relationship between moisture and the threshold. Therefore, in haptic perception research, establishing a standardized moisture control mechanism becomes a key factor in improving the repeatability of experiments.
The reproducibility of experimental results is a key challenge in the field of haptic technology research. Given the complexity and ongoing debates surrounding the effectiveness of various haptic technologies, ensuring consistent and reproducible outcomes is crucial for advancing this field. Environmental factors, such as temperature, humidity, and skin moisture, significantly influence tactile perception and impact the performance of haptic systems[72]. For example, studies have demonstrated that temperature variations of
A major challenge in haptic texture reproduction experiments is the lack of standardized device calibration, particularly regarding vibration frequency, amplitude, and force perception. This variability in calibration methods across studies affects the comparability of results. The NIST haptic benchmark proposal seeks to establish unified standards to improve the reliability and accuracy of haptic devices[74-76]. Additionally, participant selection bias is prevalent, as many studies rely on convenience sampling, leading to variations in skin type, age, and gender, all of which influence tactile perception. These individual differences can limit the generalizability of experimental outcomes, particularly in texture perception[77].
6.2. Limitations of theoretical models: isotropy assumption and thermodynamic coupling
Despite significant progress in the theoretical models of haptic reproduction technology, existing models still face numerous limitations in practical applications. Firstly, the failure of the isotropy assumption in real skin modeling remains unresolved. Most haptic models assume the isotropic nature of the skin, meaning they assume the skin’s response is consistent in all directions[78]. However, Georges Limbert’s research indicates that the physical properties of the skin exhibit clear directional characteristics, particularly in different regions of the skin surface, where significant differences in elasticity and perceptual capacity exist[79]. The failure of this assumption leads to considerable discrepancies in existing models when simulating complex scenarios involving skin contact with objects.
Another unresolved issue is the neglect of thermodynamic coupling effects. Haptic perception is not only a physical response triggered by tactile stimuli but also involves the interaction of factors such as temperature and humidity. However, most current haptic models overlook the impact of temperature on tactile perception, particularly in cases involving tactile stimuli with temperature changes (such as thermal touch), where the predictive accuracy of existing models is low[80,81]. Therefore, incorporating thermodynamic factors into haptic perception models will be crucial for improving simulation accuracy in future theoretical modeling.
The quantification and modeling of individual differences is also a significant challenge in haptic research. Although some studies have proposed statistical methods for modeling individual differences, these approaches are often overly simplistic and fail to account for the complex psychological and physiological variations among individuals. For example, there are considerable differences in tactile perception thresholds, sensitivity, and preferences across various populations, meaning that haptic reproduction technologies based on universal models often fail to meet individualized needs in practical applications[82-84]. Future research must place greater emphasis on addressing these differences through personalized modeling.
6.3. Emerging paradigms: neuromorphic computing and quantum sensing
With the continuous development of haptic reproduction technology, emerging research paradigms are beginning to take shape, holding the potential to become significant directions for future exploration. One such emerging paradigm is haptic neuromorphic computing, which simulates tactile signals with low energy consumption using Memristor-based technology. This approach shows great promise for real-time tactile feedback systems, though its practical applications remain in the early stages of research. Based on Memristor technology, it uses pulse coding to simulate the response process of haptic neurons[85]. This technology enables efficient tactile signal processing with low energy consumption and demonstrates strong neural adaptability. By simulating the synaptic plasticity of neurons, haptic neuromorphic computing offers a new theoretical foundation for the adaptive optimization of haptic perception systems[27,86].
The application prospects of quantum sensing technology are also noteworthy. Quantum sensors can achieve higher precision, particularly in tactile sensing at the nanoscale. Current research suggests that quantum sensing technology is likely to make breakthroughs in nano-tactile applications. For example, quantum tactile sensors can detect smaller force and displacement changes than current technologies[87,88]. Although quantum haptic technology remains in the exploratory stage, its potential for high precision and low noise characteristics makes it an exciting area for future research.
Another widely discussed area is the cross-modal potential of large language models (LLMs) for haptic perception. Following the success of LLMs in natural language processing, researchers have begun exploring their potential application in cross-modal perception. By integrating tactile signals with other sensory inputs, such as vision and hearing, haptic LLMs can provide richer tactile experiences and even simulate complex emotional tactile communication. This interdisciplinary research direction opens new pathways for the future development of haptic reproduction technologies[89,90].
7. FUTURE DIRECTIONS AND CONCLUSION
7.1. Future directions
Research on the neural adaptability of tactile perception mainly focuses on how short-term tactile stimuli affect the nervous system. There is less focus on the long-term changes in the nervous system caused by prolonged tactile exposure. Studies show that continuous tactile stimuli lead to changes in the nervous system that affect tactile perception, including sensitivity and thresholds[91,92]. However, most research focuses on short-term experiments, and there is little exploration of how long-term use of haptic feedback devices influences the nervous system. Haptic technology is not just limited to basic sensory feedback but also includes emotional and psychological feedback. However, no clear framework exists to measure the effectiveness of emotional transfer through haptic feedback[93-95]. Research on this should aim to develop a clear and measurable way to evaluate this. As haptic technology becomes more common, especially in medical rehabilitation and personalized services, there are rising concerns about data privacy and ethics. These technologies collect and process sensitive data, so future work should focus on creating secure systems to protect privacy and avoid unauthorized access to this data[96,97].
7.2. Conclusions
This study reviews the development of haptic texture reproduction technology, focusing on key trends and challenges in the field. Bibliometric analysis shows that the technology is shifting towards more intelligent and personalized systems, with AI and deep learning enhancing haptic feedback systems. Traditional mechanical models are being replaced by new methods based on vibration, ultrasound, and electrostatic feedback, offering the potential for fine texture reproduction and high-frequency vibrations. Understanding tactile perception mechanisms, particularly the role of receptors such as Piezo proteins and their surrounding microenvironment, is essential for improving feedback accuracy. However, accurately replicating various surface textures remains a challenge, especially for high-frequency vibrations and fine details.
The integration of neuroscience, materials science, and computer vision has been crucial in developing better tactile sensors and feedback systems. Future research should address current issues with accuracy and stability in the technology and explore how different senses can work together to improve applications in VR and medical rehabilitation.
DECLARATIONS
Authors’ contributions
Conceptualization, supervision, writing - review and editing, funding acquisition: Chen, S.
Conceptualization, methodology, investigation, data curation, formal analysis, writing - original draft: Yuan, T.
Investigation, data curation: Xu, L.
Visualization, validation: Ru, W.
Supervision, writing - review and editing: Wang, D.
Availability of data and materials
All data generated during this study are included in this published article.
Financial support and sponsorship
This research was funded by the National Natural Science Foundation of China (Nos. 52475190 and 52275191), China Postdoctoral Science Foundation Funded Project (No. 2024M751165).
Conflicts of interest
All authors declared that there are no conflicts of interest.
Ethical approval and consent to participate
Not applicable.
Consent for publication
Not applicable.
Copyright
© The Author(s) 2025.
REFERENCES
1. Fitzek, F. H. P.; Li, S. C.; Speidel, S.; Strufe, T.; Seeling, P. Frontiers of transdisciplinary research in Tactile Internet with human-in-the-loop. In 2021 17th International Symposium on Wireless Communication Systems (ISWCS), Berlin, Germany. Sep 06-09, 2021. IEEE; 2021. p. 1-6.
2. Lipomi, D. J.; Dhong, C.; Carpenter, C. W.; Root, N. B.; Ramachandran, V. S. Organic haptics: intersection of materials chemistry and tactile perception. Adv. Funct. Mater. 2020, 30, 1906850.
3. Yang, J.; Liu, S.; Meng, Y.; et al. Self-powered tactile sensor for gesture recognition using deep learning algorithms. ACS. Appl. Mater. Interfaces. 2022, 14, 25629-37.
4. Li, R.; Adelson, E. H. Sensing and recognizing surface textures using a GelSight sensor. In 2013 IEEE Conference on Computer Vision and Pattern Recognition, Portland, USA. Jun 23-28, 2013. IEEE; 2013. pp. 1241-7.
5. Olugbade, T.; He, L.; Maiolino, P.; Heylen, D.; Bianchi-Berthouze, N. Touch technology in affective human-, robot-, and virtual-human interactions: a survey. Proc. IEEE. 2023, 111, 1333-54.
6. Di Stefano, N.; Spence, C. Roughness perception: a multisensory/crossmodal perspective. Atten. Percept. Psychophys. 2022, 84, 2087-114.
7. Sathian, K.; Lacey, S. Cross-modal interactions of the tactile system. Curr. Dir. Psychol. Sci. 2022, 31, 411-8.
8. Chen, S.; Ge, S.; Tang, W.; Zhang, J.; Chen, N. Tactile perception of fabrics with an artificial finger compared to human sensing. Text. Res. J. 2015, 85, 2177-87.
9. Mostafavi Yazdi, S. J.; Baqersad, J. Mechanical modeling and characterization of human skin: a review. J. Biomech. 2022, 130, 110864.
10. Kirby, M. A.; Tang, P.; Liou, H. C.; et al. Probing elastic anisotropy of human skin in vivo with light using non-contact acoustic micro-tapping OCE and polarization sensitive OCT. Sci. Rep. 2022, 12, 3963.
11. Infante, V. H. P.; Fehlberg, M.; Saikumar, S.; Drewing, K.; Meinke, M. C.; Bennewitz, R. The role of skin hydration, skin deformability, and age in tactile friction and perception of materials. Sci. Rep. 2025, 15, 9935.
12. Coste, B.; Mathur, J.; Schmidt, M.; et al. Piezo1 and Piezo2 are essential components of distinct mechanically activated cation channels. Science 2010, 330, 55-60.
13. Douguet, D.; Honoré, E. Mammalian mechanoelectrical transduction: structure and function of force-gated ion channels. Cell 2019, 179, 340-54.
14. Bochereau, S. Perception, recording and reproduction of physical invariants during bare fingertip exploration of tactile textures. 2017. https://theses.hal.science/tel-01609838v1. (accessed 26 Jun 2025).
15. Henderson, J. An investigation of the neural basis of texture processing during active touch. 2023. https://www.proquest.com/openview/3c3a3d045a93675055c053ec6393644d/1?pq-origsite=gscholar&cbl=2026366&diss=y. (accessed 26 Jun 2025).
16. Kuroki, S.; Sawayama, M.; Nishida, S. The roles of lower- and higher-order surface statistics in tactile texture perception. J. Neurophysiol. 2021, 126, 95-111.
17. Chen, H.; Fu, S.; Zhi, X.; et al. Research progress on neural processing of hand and forearm tactile sensation: a review based on fMRI research. Neuropsychiatr. Dis. Treat. 2025, 21, 193-212.
18. Liu, Z.; Kim, J. T.; Rogers, J. A.; Klatzky, R. L.; Colgate, J. E. Realism of tactile texture playback: a combination of stretch and vibration. IEEE. Trans. Haptics. 2024, 17, 441-50.
19. See, A. R.; Choco, J. A. G.; Chandramohan, K. Touch, texture and haptic feedback: a review on how we feel the world around us. Appl. Sci. 2022, 12, 4686.
20. Yin, F.; Niu, H.; Kim, E.; Shin, Y. K.; Li, Y.; Kim, N. Advanced polymer materials-based electronic skins for tactile and non-contact sensing applications. InfoMat 2023, 5, e12424.
21. Fan, L.; Song, A.; Zhang, H. Haptic interface device using cable tension based on ultrasonic phased array. IEEE. Access. 2020, 8, 162880-91.
22. Kumar, A.; Kempski Leadingham, K. M.; Kerensky, M. J.; Sankar, S.; Thakor, N. V.; Manbachi, A. Visualizing tactile feedback: an overview of current technologies with a focus on ultrasound elastography. Front. Med. Technol. 2023, 5, 1238129.
23. Hecht, D.; Reiner, M. Sensory dominance in combinations of audio, visual and haptic stimuli. Exp. Brain. Res. 2009, 193, 307-14.
24. Boban, L.; Pittet, D.; Herbelin, B.; Boulic, R. Changing finger movement perception: influence of active haptics on visual dominance. Front. Virtual. Real. 2022, 3, 860872.
25. Friedrich, J.; Beste, C. The impact of stimulus modality on the processing of conflicting sensory information during response inhibition. Neuroscience 2019, 410, 191-201.
26. Jagt, M.; Ganis, F.; Serafin, S. Enhanced neural phase locking through audio-tactile stimulation. Front. Neurosci. 2024, 18, 1425398.
27. Li, Z.; Li, Z.; Tang, W.; et al. Crossmodal sensory neurons based on high-performance flexible memristors for human-machine in-sensor computing system. Nat. Commun. 2024, 15, 7275.
28. Strese, M.; Brudermueller, L.; Kirsch, J.; Steinbach, E. Haptic material analysis and classification inspired by human exploratory procedures. IEEE. Trans. Haptics. 2020, 13, 404-24.
29. Adilkhanov, A.; Rubagotti, M.; Kappassov, Z. Haptic devices: wearability-based taxonomy and literature review. IEEE. Access. 2022, 10, 91923-47.
30. Biswas, S.; Visell, Y. Haptic perception, mechanics, and material technologies for virtual reality. Adv. Funct. Mater. 2021, 31, 2008186.
31. Pestell, N.; Lepora, N. F. Artificial SA-I, RA-I and RA-II/vibrotactile afferents for tactile sensing of texture. J. R. Soc. Interface. 2022, 19, 20210603.
32. Kim, S.; Lee, D. Y. Introduction to haptic systems. control design for haptic systems. Singapore: Springer Nature; 2024. pp. 1-11.
33. Basdogan, C.; Giraud, F.; Levesque, V.; Choi, S. A review of surface haptics: enabling tactile effects on touch surfaces. IEEE. Trans. Haptics. 2020, 13, 450-70.
34. Jung, Y.; Ramos, J. A large force haptic interface with modular linear actuators. Actuators 2023, 12, 293.
35. Zhu, M.; Biswas, S.; Dinulescu, S. I.; Kastor, N.; Hawkes, E. W.; Visell, Y. Soft, wearable robotics and haptics: technologies, trends, and emerging applications. Proc. IEEE. 2022, 110, 246-72.
36. Chen, K.; Li, T.; Yan, T.; et al. A soft gripper design for apple harvesting with force feedback and fruit slip detection. Agriculture 2022, 12, 1802.
37. Hong, W.; Guo, X.; Li, X.; et al. Fishbone and nettle fiber inspired stretchable strain sensor with high sensitivity and wide sensing range for wearable electronics. Chem. Eng. J. 2024, 492, 152281.
38. Chen, S.; Chen, Y.; Yang, J.; Han, T.; Yao, S. Skin-integrated stretchable actuators toward skin-compatible haptic feedback and closed-loop human-machine interactions. npj. Flex. Electron. 2023, 7, 235.
39. Suzuki, S.; Fujiwara, M.; Makino, Y.; Shinoda, H. Radiation pressure field reconstruction for ultrasound midair haptics by greedy algorithm with brute-force search. IEEE. Trans. Haptics. 2021, 14, 914-21.
40. Ragolia, M. A.; De Palma, L.; Giaquinto, N.; Pignatelli, A.; Scarpetta, M. Ultrasound haptics for XR and rehabilitation: influence of arm and hand muscle stiffness on user perception. In 2024 IEEE International Conference on Metrology for eXtended Reality, Artificial Intelligence and Neural Engineering (MetroXRAINE), St Albans, UK. Oct 21-23, 2024. IEEE; 2024. pp. 1000-4.
41. Zhang, K.; Liu, Z.; Zhou, Y.; et al. Thin and flexible breeze-sense generators for non-contact haptic feedback in virtual reality. Nanomicro. Lett. 2025, 17, 144.
42. Cao, H. X.; Jung, D.; Lee, H. S.; et al. Holographic acoustic tweezers for 5-DoF manipulation of nanocarrier clusters toward targeted drug delivery. Pharmaceutics 2022, 14, 1490.
43. Hirayama, R.; Martinez Plasencia, D.; Masuda, N.; Subramanian, S. A volumetric display for visual, tactile and audio presentation using acoustic trapping. Nature 2019, 575, 320-3.
44. Gao, Y.; Yao, K.; Jia, S.; et al. Advances in materials for haptic skin electronics. Matter 2024, 7, 2826-45.
45. Zhi, C.; Shi, S.; Wu, H.; et al. Emerging trends of nanofibrous piezoelectric and triboelectric applications: mechanisms, electroactive materials, and designed architectures. Adv. Mater. 2024, 36, e2401264.
46. Chi, X.; Tan, C.; Li, B.; Lu, J.; Gu, C.; Fu, C. Multidisciplinary optimization of electromagnetic linear actuators for direct-drive systems with a combination of static and dynamic performance. COMPEL 2023, 42, 476-93.
47. Singh, N. K. Fabrication, characterization and modeling of electroactive polymer-based strain sensors for wearable applications. 2022. (in Japanese) https://kyutech.repo.nii.ac.jp/records/7811. (accessed 26 Jun 2025).
48. Xiang, H.; Peng, L.; Yang, Q.; Wang, Z. L.; Cao, X. Triboelectric nanogenerator for high-entropy energy, self-powered sensors, and popular education. Sci. Adv. 2024, 10, eads2291.
50. Brahimaj, D. Integrating haptic feedback in smart devices: multimodal interfaces and design guidelines. 2024. https://theses.hal.science/tel-04623701. (accessed 26 Jun 2025).
51. Zhang, M.; Terui, S.; Makino, Y.; Shinoda, H. TexSenseGAN: a user-guided system for optimizing texture-related vibrotactile feedback using generative adversarial network. IEEE. Trans. Haptics. 2025, 18, 325-39.
52. Cai, S.; Zhao, L.; Ban, Y.; Narumi, T.; Liu, Y.; Zhu, K. GAN-based image-to-friction generation for tactile simulation of fabric material. Comput. Graph. 2022, 102, 460-73.
53. Yi, Z.; Zhang, Y.; Peters, J. Biomimetic tactile sensors and signal processing with spike trains: a review. Sens. Actuators. A. Phys. 2018, 269, 41-52.
54. Docquier, N.; Timmermans, S.; Fisette, P. Haptic devices based on real-time dynamic models of multibody systems, Sensors 2021;21:4794.
55. Fang, Y.; Zhang, X.; Xu, W.; Liu, G.; Zhao, J. Bidirectional visual-tactile cross-modal generation using latent feature space flow model. Neural. Netw. 2024, 172, 106088.
56. Aykut, T.; Karimi, M.; Burgmair, C.; Finkenzeller, A.; Bachhuber, C.; Steinbach, E. Delay compensation for a telepresence system with 3D 360 degree vision based on deep head motion prediction and dynamic FoV adaptation. IEEE. Robot. Autom. Lett. 2018, 3, 4343-50.
57. Lei, Y.; Deng, Y.; Dong, L.; Li, X.; Li, X.; Su, Z. A novel sensor fusion approach for precise hand tracking in virtual reality-based human-computer interaction. Biomimetics 2023, 8, 326.
58. Shen, Y.; Pan, Z. Evaluating the impact of immersive virtual reality learning environments with a cognitive load on students in various interaction modes. In 2022 8th International Conference on Virtual Reality (ICVR), Nanjing, China. May 26-28, 2022. IEEE; 2022. pp. 210-5.
59. Webb, M.; Tracey, M.; Harwin, W.; et al. Haptic-enabled collaborative learning in virtual reality for schools. Educ. Inf. Technol. 2022, 27, 937-60.
60. Tanacar, N. T.; Mughrabi, M. H.; Batmaz, A. U.; Leonardis, D.; Sarac, M. The impact of haptic feedback during sudden, rapid virtual interactions. In 2023 IEEE World Haptics Conference (WHC), Delft, Netherlands. Jul 10-13, 2023. IEEE; 2023. pp. 64-70.
61. Brunnström, K.; Dima, E.; Qureshi, T.; Johanson, M.; Andersson, M.; Sjöström, M. Latency impact on Quality of Experience in a virtual reality simulator for remote control of machines. Signal. Process. Image. Commun. 2020, 89, 116005.
62. Raspopovic, S.; Valle, G.; Petrini, F. M. Sensory feedback for limb prostheses in amputees. Nat. Mater. 2021, 20, 925-39.
63. Pasluosta, C.; Kiele, P.; Stieglitz, T. Paradigms for restoration of somatosensory feedback via stimulation of the peripheral nervous system. Clin. Neurophysiol. 2018, 129, 851-62.
64. Weber, D. J.; Hao, M.; Urbin, M. A.; Schoenewald, C.; Lan, N. Chapter Twenty one - Sensory information feedback for neural prostheses. In: Biomedical information technology. Elsevier; 2020. pp. 687-715.
65. Girard, A.; Marchal, M.; Gosselin, F.; Chabrier, A.; Louveau, F.; Lécuyer, A. HapTip: displaying haptic shear forces at the fingertips for multi-finger interaction in virtual environments. Front. ICT. 2016, 3, 6.
66. Kourtesis, P.; Argelaguet, F.; Vizcay, S.; Marchal, M.; Pacchierotti, C. Electrotactile feedback applications for hand and arm interactions: a systematic review, meta-analysis, and future directions. IEEE. Trans. Haptics. 2022, 15, 479-96.
67. Höhler, C.; Trigili, E.; Astarita, D.; Hermsdörfer, J.; Jahn, K.; Krewer, C. The efficacy of hybrid neuroprostheses in the rehabilitation of upper limb impairment after stroke, a narrative and systematic review with a meta-analysis. Artif. Organs. 2024, 48, 232-53.
68. Li, S.; Xu, J. Multiaxis force/torque sensor technologies: design principles and robotic force control applications: a review. IEEE. Sensors. J. 2025, 25, 4055-69.
69. Yi, Z.; Xu, T.; Guo, S.; Shang, W.; Wu, X. Tactile surface roughness categorization with multineuron spike train distance. IEEE. Trans. Automat. Sci. Eng. 2021, 18, 1835-45.
70. Liao, X.; Li, Y.; Hu, J.; et al. Effects of contact method and acclimation on temperature and humidity in touch perception. Text. Res. J. 2018, 88, 1605-15.
71. Filingeri, D.; Fournet, D.; Hodder, S.; Havenith, G. Tactile cues significantly modulate the perception of sweat-induced skin wetness independently of the level of physical skin wetness. J. Neurophysiol. 2015, 113, 3462-73.
72. Jha, S.; Balaji, M.; Peck, J.; Oakley, J.; Deitz, G. D. The effects of environmental haptic cues on consumer perceptions of retailer warmth and competence. J. Retail. 2020, 96, 590-605.
73. Dione, M.; Watkins, R. H.; Aimonetti, J. M.; Jourdain, R.; Ackerley, R. Effects of skin moisturization on various aspects of touch showing differences with age and skin site. Sci. Rep. 2023, 13, 17977.
74. Kirschner, R. J.; Kurdas, A.; Karacan, K.; et al. Towards a reference framework for tactile robot performance and safety benchmarking. In 2021 IEEE/RSJ International Conference on Intelligent Robots and Systems (IROS), Prague, Czech Republic. Sep 27 - Oct 01, 2021. IEEE; 2021. pp. 4290-7.
75. Li, F.; Hiley, J.; Syed, T. M.; Hitchens, C.; Garcia Lopez-Astilleros, M. A region segmentation method to measure multiple features using a tactile scanning probe. Int. J. Comput. Integr. Manuf. 2019, 32, 569-79.
76. Bi, Z.; Miao, Z.; Zhang, B.; Zhang, C. W. The state of the art of testing standards for integrated robotic systems. Robot. Comput. Integr. Manuf. 2020, 63, 101893.
77. Hedge, C.; Powell, G.; Sumner, P. The reliability paradox: why robust cognitive tasks do not produce reliable individual differences. Behav. Res. Methods. 2018, 50, 1166-86.
78. Krishnan, A.; Thiyagarajan, K.; Kodagoda, S.; Bhattacharjee, M. Wearable flexible temperature sensor suite for thermal-tactile perception. IEEE. Sensors. J. 2024, 24, 39736-43.
79. Limbert, G. Mathematical and computational modelling of skin biophysics: a review. Proc. Math. Phys. Eng. Sci. 2017, 473, 20170257.
80. Bai, J.; Peng, J.; Tang, D.; et al. Thermal tactile perception: device, technology, and experiments. Int. J. Cogn. Inform. Nat. Intell. 2021, 15, 1-19.
81. Park, J.; Lee, Y.; Hong, J.; et al. Tactile-direction-sensitive and stretchable electronic skins based on human-skin-inspired interlocked microstructures. ACS. Nano. 2014, 8, 12020-9.
82. Emami, M.; Bayat, A.; Tafazolli, R.; Quddus, A. A survey on haptics: communication, sensing and feedback. IEEE. Commun. Surv. Tutorials. 2025, 27, 2006-50.
83. Dalsgaard, T. S.; Schneider, O. A unified model for haptic experience. ACM. Trans. Comput. Hum. Interact. 2025, 32, 1-38.
84. Raisamo, R.; Salminen, K.; Rantala, J.; Farooq, A.; Ziat, M. Interpersonal haptic communication: review and directions for the future. Int. J. Hum. Comput. Stud. 2022, 166, 102881.
85. Xie, Z.; Zhu, X.; Wang, W.; et al. Temporal pattern coding in ionic memristor-based spiking neurons for adaptive tactile perception. Adv. Elect. Mater. 2022, 8, 2200334.
86. Kumar, S.; Kumar, N.; Tiwari, S.; Sandeep,
87. Xavier, J.; Yu, D.; Jones, C.; Zossimova, E.; Vollmer, F. Quantum nanophotonic and nanoplasmonic sensing: towards quantum optical bioscience laboratories on chip. Nanophotonics 2021, 10, 1387-435.
88. Tafadzwa Mpofu, K.; Mthunzi-Kufa, P. Recent advances in quantum biosensing technologies. In: Current developments in biosensor applications and smart strategies [Working Title]. IntechOpen; 2025.
89. Maclean, K. E.; Schneider, O. S.; Seifi, H. Multisensory haptic interactions: understanding the sense and designing for it. In: The Handbook of multimodal-multisensor interfaces, Volume 1; 2017. pp. 97-142.
90. Cornelio, P.; Velasco, C.; Obrist, M. Multisensory integration as per technological advances: a review. Front. Neurosci. 2021, 15, 652611.
91. Graczyk, E. L.; Schiefer, M. A.; Saal, H. P.; Delhaye, B. P.; Bensmaia, S. J.; Tyler, D. J. The neural basis of perceived intensity in natural and artificial touch. Sci. Transl. Med. 2016, 8, 362ra142.
92. Parianen Lesemann, F. H.; Reuter, E. M.; Godde, B. Tactile stimulation interventions: influence of stimulation parameters on sensorimotor behavior and neurophysiological correlates in healthy and clinical samples. Neurosci. Biobehav. Rev. 2015, 51, 126-37.
93. Mcdaniel, T.; Panchanathan, S. Therapeutic haptics for mental health and wellbeing. In: Mcdaniel T, Panchanathan S, editors. Haptic interfaces for accessibility, health, and enhanced quality of life. Cham: Springer International Publishing; 2020. pp. 149-81.
94. Hajas, D. Ultrasonic mid-air haptic technology in context of science communication, 2021. https://sussex.figshare.com/articles/thesis/Ultrasonic_mid-air_haptic_technology_in_context_of_science_communication/23481617?file=41190560. (accessed 26 Jun 2025).
95. Ninu, A.; Dosen, S.; Farina, D.; Rattay, F.; Dietl, H. A novel wearable vibro-tactile haptic device. In 2013 IEEE International Conference on Consumer Electronics (ICCE), Las Vegas, USA. Jan 11-14, 2013. IEEE; 2013. pp. 51-2.
96. Ley, M.; Rambukkana, N. Touching at a distance: digital intimacies, haptic platforms, and the ethics of consent. Sci. Eng. Ethics. 2021, 27, 63.
Cite This Article

How to Cite
Download Citation
Export Citation File:
Type of Import
Tips on Downloading Citation
Citation Manager File Format
Type of Import
Direct Import: When the Direct Import option is selected (the default state), a dialogue box will give you the option to Save or Open the downloaded citation data. Choosing Open will either launch your citation manager or give you a choice of applications with which to use the metadata. The Save option saves the file locally for later use.
Indirect Import: When the Indirect Import option is selected, the metadata is displayed and may be copied and pasted as needed.
About This Article
Special Issue
Copyright
Data & Comments
Data
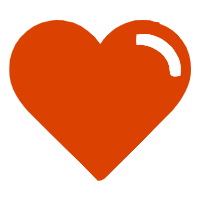
Comments
Comments must be written in English. Spam, offensive content, impersonation, and private information will not be permitted. If any comment is reported and identified as inappropriate content by OAE staff, the comment will be removed without notice. If you have any queries or need any help, please contact us at [email protected].