Design of a polymer electrolyte membrane for enhanced zinc anode stability in reversible aqueous zinc-ion batteries
Abstract
Aqueous zinc-ion batteries (ZIBs) hold great promise for energy storage applications. Nevertheless, the realization of high-capacity ZIBs with extended cycle durability remains a significant scientific challenge, predominantly attributed to two inherent limitations: the uncontrollable dendritic growth and concomitant side reactions. In this study, we present a polymer electrolyte membrane denoted as TAC, which addresses these challenges by enhancing the uniform distribution of zinc ions. By incorporating phenolic hydroxyl groups from tannic acid (TA) onto the surface of cellulose fibers, TAC is synthesized, which not only effectively shields both the front and back surfaces of the zinc anode from corrosive effects of the liquid electrolyte, but also exhibits a high liquid-retention capacity under pressures up to 5 MPa. Combining density functional theory simulations with experimental investigations, we demonstrate that the phenolic hydroxyl groups from TA actively engage with zinc ions, thereby significantly reducing the desolvation energy during the plating/stripping processes of the zinc anode. The assembled battery utilizing 1% TAC achieves remarkable performance, retaining 83.1% of its discharge capacity after 1,000 cycles at a current density of 5 C. Moreover, it exhibits high reversibility, high coulombic efficiency of 99.9%, and an impressive lifespan exceeding 2,300 h at 0.5 mA cm-2. Furthermore, 1% TAC demonstrates excellent cycling stability across four different electrolyte systems [ZnSO4, Zn(CF3SO3)2, Zn(OAc)2, and ZnCl2], highlighting its outstanding compatibility across diverse electrolyte compositions. The exceptional performance of the assembled batteries underscores the efficacy of our design, offering a novel strategy for the development and fabrication of polymer electrolyte membranes tailored for aqueous ZIBs.
Keywords
INTRODUCTION
The heightened prevalence of environmental pollution and escalating energy consumption have spurred the dynamic advancement of clean and renewable energy technologies. However, the intermittent nature and inherent variability of wind and solar energy have posed obstacles to their seamless integration into electrical infrastructure. Consequently, the storage and conversion of energy necessitate secondary batteries endowed with superior performance characteristics to ensure the consistent delivery of clean power. Among the widely discussed secondary batteries, zinc-ion batteries (ZIBs), utilizing a blend of pure water and zinc salts as electrolytes, have emerged as a promising contender for large-scale energy storage and mobile power applications. This is attributed to their notable features of being low-cost, high-energy, highly safe, and environmentally friendly[1-6]. However, the utilization of ZIBs is significantly impeded by the instability of zinc metal anodes during the plating/stripping process[7], primarily attributable to zinc dendrites, zinc corrosion, and side reactions occurring on the anode[8-10]. Zinc dendrites, characterized by a high Young’s modulus, proliferate with cycling, introducing dead zinc metal that extends to the cathode and induces short circuits in the battery. Conversely, pure zinc metal is prone to corrosion when exposed to salt solutions, leading to its degradation and the accumulation of byproducts on the anode surface. This circumstance severely hampers the zinc plating/stripping process and diminishes the cycling lifespan of ZIBs. To address these challenges and enhance the reversibility of the anode in ZIBs, numerous effective strategies have been proposed. These include the incorporation of additives into the electrolyte[5,11,12], the fabrication of semi/all-solid-state electrolytes[13-17], the construction of layered protection around the anodes[10,18,19], the design of intricate anode structures[20-24], and the utilization of polymer electrolytes[25-27]. Among these approaches, the utilization of polymer electrolytes stands out as the simplest and most effective method to enhance the electrochemical performance of ZIBs. Polymer electrolytes offer numerous advantages[28,29], including higher electrolyte-confinement capability[30], superior uniform distribution of ions in solution, easily controlled thickness, broader operating temperatures, and better interface compatibility[28] compared to aqueous electrolytes. Furthermore, owing to their cross-linked structure and functional groups, the electrochemical properties of the polymer can be readily optimized through the design of unique structures, incorporation of functional groups, and combination with other materials[29,31].
In order to mitigate zinc dendrite formation and enhance ion conductivity in ZIBs using optimized polymer electrolytes, researchers have proposed and designed a series of polymer electrolytes. These include poly (ethylene oxide)[32], xanthan gum[33], gelatin[34], polyacrylamide[35], carboxymethyl cellulose sodium[36], and polyvinyl alcohol[37,38]. It is noteworthy that the aforementioned polymer electrolytes have demonstrated excellent electrochemical performance with significant implications. However, the preparation processes are complicated and often yield numerous byproducts. Therefore, there is an urgent need to develop high-performance ZIBs by utilizing polymer electrolytes based on sustainable materials through easily implementable methods.
Cellulose, a renewable biomaterial composed of nanofibers made of hexose units, possesses exceptional hydrophilicity and moisture retention due to the abundance of hydroxyl groups along its lengthy chains. Additionally, it boasts advantages such as low cost, sustainability, biodegradability, chemical stability, and widespread availability as a natural polymer, rendering it a promising candidate for high-performance electrolytes in ZIB applications[39-43]. However, the pristine cellulose-based electrolytes in ZIBs exhibit poor performance and low capacity during cycling, primarily due to their inability to prevent the formation of zinc dendrites on the anode and the dissolution of cathode materials.
In this study, a polymer electrolyte membrane (TAC) was synthesized by incorporating tannic acid (TA) into cellulose, facilitating the formation of ether bonds and introducing numerous phenolic hydroxyl groups. Compared to pristine cellulose, TAC exhibits enhanced liquid retention capacity, effectively mitigating cathode material dissolution and non-reactive parts corrosion of zinc foil. Moreover, the lower binding energy (Eb) of phenolic hydroxyl groups and zinc ions in TAC, compared to pristine cellulose, significantly inhibits zinc dendrite growth on the anode, resulting in reduced desolvation energy and accelerated uniform zinc ion deposition. These findings were corroborated through thermodynamic calculations and Zn-MnO2 battery test. Notably, a battery employing 1% TAC demonstrated impressive performance metrics, maintaining a high discharge capacity retention of 83.1% after 1,000 cycles at a current density of 5 C, coupled with exceptional reversible ability (99.9% coulombic efficiency) and prolonged lifespan exceeding 2,300 h at a current density of 0.5 mA cm-2. This innovative design not only provides effective strategies for fabricating high-performance ZIBs but also holds promise for broader applications in secondary batteries. Hence, as depicted in Figure 1A, TAC was synthesized by introducing TA into the cellulose solution. In brief, a homogeneous cellulose solution was blended with TA and reacted in pure water for approximately 30 min. The reaction between cellulose and TA resulted in the formation of a polymer electrolyte membrane, which was subsequently vacuum-filtered to produce a film with abundant phenolic hydroxyl groups distributed on the surface of the fibers. Figure 1B illustrates the schematic diagram for protecting the Zn anode. It is noteworthy that due to the stronger attractive interaction between the phenolic hydroxyl groups in TAC and Zn2+, the flux of zinc ions was effectively and uniformly regulated. Consequently, in the absence of TA, the battery produced vertical zinc dendrites after extended cycling. Conversely, in the presence of TA, zinc deposition and stripping occurred uniformly, resulting in horizontally stacked zinc layers without zinc dendrites.
EXPERIMENTAL
Preparation of TAC: X% (X = 0, 0.5, 1, 3) TAC was prepared as follows: 2 g bacterial cellulose
MnO2/carbon nanotube (CNT) material was synthesized referencing a previous work with a slight modification[44]; the detail of experiment was as follows: 0.15 g multi-walled CNT (diameter: 5-15 nm, length: 10-30 μm, Nanjing XFNANO Materials Tech Co., Ltd) with hydroxylation was dispersed in 150 mL pure water and 2.03 g MnSO4 (AR grade, Aladdin) was added into the above solution stirring for 30 min. 1.27 g KMnO4 (AR grade, Alfa) was dispersed into 80 mL pure water stirring for 30 min and added into the above solution slowly stirring for 10 min. Then, the mixture solution was transferred to an autoclave heating for 12 h at 120 °C and obtained a dark brown powder through filtering and drying.
For preparing cathode electrode, MnO2/CNT powder, super P carbon black (TIMCAL), and poly(vinylidene fluoride) binder(Arkema) (weight ratio of 7:2:1) were mixed in N-Methylpyrrolidone solvent (99.9%, Aladdin), stirred for 1 h, and coated on a piece of single-walled CNTs paper (Nanjing XFNANO Materials Tech Co., Ltd). Then it was dried in a vacuum at 70 °C and cut into electrodes with a diameter of 9 mm and a mass loading of 0.6-1.5 mg MnO2. Zinc foil (purity > 99.98%, Alfa) was polished using sandpaper and used as anode.
Characterization: The surface morphology of electrode and TAC materials was revealed using a scanning electron microscope (SEM) (Zeiss Sigma 300). The functional groups and chemical states of TAC materials were investigated by X-ray photoelectron spectroscopy (XPS) (Thermo Scientific K-Alpha) and Fourier transform infrared spectroscopy (FTIR) spectra (Thermo Scientific Nicolet iS5). An electronic universal testing machine (MTS CMT6103) and optical contact angle measuring system (KRUSS DSA100) were utilized to evaluate the mechanical properties and wettability of TAC materials. The thermal curves were performed by simultaneous thermal analyzer (NETZSCH STA 449F5) at 10 °C min-1 under nitrogen atmosphere.
Electrochemical measurements: Cyclic voltammetry (CV) curves, linear sweeping voltammetry (LSV), and electrochemical impedance spectroscopy (EIS) were tested using an Admiral potentiostats (Squidstat Plus). The CV and LSV were conducted using polished Zn foil and obtained MnO2/CNT material corresponding to the counter electrode, the reference electrode, and the work electrode, respectively. Electrochemical properties of Zn-MnO2 batteries (voltage range of 0.8-1.85 V) and Zn||Zn batteries were tested using CR2032-type coin cells and 2001A battery testing system at 25 °C. Before the X% TAC materials were used as polymer electrolyte membranes, a small amount of 2 M ZnSO4 mixed with 0.1 M MnSO4,
The liquid retention capacity of TAC materials under 5 MPa was determined by
where M0 is the weight of TAC before soaked in the mixture solution of 2 M ZnSO4 + 0.1 M MnSO4. M1 is the weight of TAC after being soaked in the mixture solution under 5 MPa.
The test of liquid retention rates with 5 MPa: First, 0%, 0.5%, 1%, and 3% TAC were cut into samples with 19 mm diameter and soaked in the liquid electrolyte with 2 M ZnSO4 + 0.1 M MnSO4 for 6 h. The weights of abovementioned polymer electrolytes were recorded and named as M0 and M1, where M0 is the weight of TAC before soaked in the mixture solution of 2 M ZnSO4 + 0.1 M MnSO4. M1 is the weight of TAC after being soaked in the mixture solution under pressure of 5 MPa. The hollow diameter size of bibulous paper is larger than 19 mm (by 1-2 mm) avoiding the polymer electrolyte contact with bibulous directly.
DFT calculation: The first principal calculation was conducted in the computational chemistry package of Gaussian 16 program[45] based on the density functional theory (DFT). The optimized structures without virtual frequency were acquired with the B3LYP functional[46]. The basis set 6-311+G (d, p)[47] with D3 (BJ)[48] was utilized for C, H and O atoms while the SDD basis set[49,50] with an effective core potential (ECP) was employed for Zn atoms. The impact of the water solvent environment on all the systems was taken into consideration on the basis of the IEFPCM model[51] for structure optimization. The Multiwfn[52-55] and VMD[56] program were utilized in the calculation and analysis of electrostatic potential (ESP) on molecule surface. The binding energies of all systems were calculated under the M06-2X-D3/def2-TZVP[57-59] level and the ECP was also used for Zn atoms. The solvation model density (SMD) model[60] was taken into consideration in the calculation of binding energies. The Eb for system was defined according to
where Etotal, E2, and E1 stand for the energy for the interaction system, the different substrate materials (0% TAC, 1% TAC), and Zn2+, respectively.
RESULTS AND DISCUSSION
Optical images illustrating TAC concentrations of 0%, 0.5%, 1%, and 3% are shown in
Figure 2. SEM images of (A) 0% TAC, (B) 0.5% TAC, (C) 1% TAC, and (D) 3% TAC; (E) XPS of C 1s of the TAC samples; (F) FTIR spectra of TAC samples; (G) Galvanostatic Zn stripping and plating in a Zn||Zn cell using TAC under different current density (0.1, 0.2, 0.5, 1, and 2 mA cm-2) with 1 mAh cm-2 capacity limitation; Potential profiles of Zn/Zn cell under (H) 0.1, (I) 0.2, (J) 0.5, and (K)
Upon the addition of TA, there was an observable increase in the C-O-C content of TAC, suggesting a reaction between TA and the oxygen groups within the cellulose matrix
Figure 3. SEM images of (A) 10 μm and (B) 200 nm of 1% TAC, (C) 10 μm and (D) 200 nm of 0% TAC; SEM images of Zn anode in Zn||Zn symmetry cells after 700 h plating/stripping cycles in ZnSO4 using (E) 10 μm and (F) 500 nm of 1% TAC, (G) 10 μm and (H) 500 nm of 0% TAC at 0.5 mA cm-2; (I) Galvanostatic Zn stripping and plating in a Zn||Zn cell using TAC with 2 M ZnSO4 as the electrolyte under current density of 0.5 mA cm-2 with 1 mAh cm-2 capacity limitation; Potential profiles of Zn||Zn cell plating/stripping cycles using 1% TAC at (J) the first, (K) the 100th, (L) 200th, (M) 400th, (N) 500th with 1 mAh cm-2 capacity limitation.
The electrochemical stability of 0% and 1% TAC was investigated through LSV curves, employing a limited voltage of 2.5 V and a scan rate of 0.1 mV s-1, as shown in Supplementary Figure 5D. It was observed that the current profiles of 0% and 1% TAC in Zn-MnO2 batteries remained stable below 1.54 and 1.90 V, respectively. This suggests that 1% TAC exhibits superior stability, particularly at higher voltage. Furthermore, the stability and electrochemical performances of TAC materials and both positive and negative electrodes were assessed using EIS and CV, as illustrated in Supplementary Figure 6A-D. Notably, in the context of Zn-MnO2 batteries, 1% TAC demonstrated enhanced electrochemical stability and interfacial compatibility compared to 0% TAC. To explore the protective role of TAC on the Zn anode, Zinc foils were employed as electrodes in Zn||Zn batteries, utilizing both 0% and 1% TAC with a 2 M ZnSO4 electrolyte. These batteries underwent plating and stripping cycles for 700 h at a current density of
Figure 4. (A) Schematic of Zn2+ plating/stripping process by using 0% TAC or 1% TAC; (B) LUMO and HOMO gap comparison between 1% TAC and 0% TAC; electrostatic potential (ESP) distribution on the Van der Waals surface of (C) 0% TAC and (D)
Hence, the maxima ESP value of 1% TAC with Zn2+ was reduced to 395.1561 kcal mol-1, which was lower than that of 0% TAC with Zn2+ (440.0305 kcal mol-1), as shown in Supplementary Figure 10. Therefore, in comparison with 0% TAC, the easier interaction and stronger attraction interaction between 1% TAC and Zn2+ indicated that the desolvation process of Zn2+ with 1% TAC was easier than that with 0% TAC. Less energy was consumed during the process when zinc ions left the electrolyte to move to the interface of the anode electrode, which made the reaction process easier and boosted the uniform distribution of zinc ions on the zinc foil electrode. As a result of the weaker attraction interaction between 0% TAC and Zn2+, zinc ions were nonuniformly distributed on the surface of the anode electrode and a large number of dendrites were found, as shown in Figure 4A. On the other hand, 1% TAC possessed abundant hydroxyl and π-π stacking that exhibited high interaction with H2O molecules, which ensured excellent liquid electrolyte retention of the 1% TAC at 5 MPa. In addition, in order to assess the compatibility of the TAC with different electrolytes, galvanostatic Zn stripping and plating in a Zn||Zn cell using TAC was conducted in various electrolytes, as shown in Figure 5. After long cycles of the Zn foil with 1% TAC in Zn(CF3SO3)2 as shown in Figure 5A, abundant regular bulks composed of stacked flakes can be observed. while in
Figure 5. SEM images of Zn anode in Zn|| Zn cells after long cycles in different electrolytes: (A) 1% TAC and (B) 0% TAC in
Hence, the cycle performance of 1% TAC is prior to that of 0% TAC, which was displayed in Figure 5G for Zn(CF3SO3)2 and Figure 5H for Zn(OAc)2. Concretely, when in Zn(OAc)2 at 2 mA cm-2, 1% TAC nearly stably cycles for 1,200 h while the battery using 0% TAC shot-circuited within 100 h; when used in
In addition, the CV curves of the Zn-MnO2 batteries that used 0% TAC or 1% TAC were investigated, as shown in Figure 6A. Both CV profiles presented similar redox reaction pairs, indicating that 1% TAC did not influence the intercalation/deintercalation process of Zn2+. To study the electrochemical properties of the TAC, CNT paper with MnO2, 0% TAC or 1% TAC, and zinc foil, were used as the positive electrode, polymer electrolyte membrane, and negative electrode assembled in Zn-MnO2 batteries, respectively. To investigate the adaptability of 1% TAC, the electrochemical performance of the assembled battery was investigated in ZnSO4, as shown in Figure 6B-D and Zn(CF3SO3)2, as shown in Figure 6E-G, as the matrix of the aqueous electrolyte, respectively. As shown in Figure 6B, the battery using 1% TAC displayed a higher rate capability than that using 0% TAC. This was because 1% TAC possessed abundant phenolic hydroxyls, which modified the solvation environment of Zn2+ ions, weakened the solvation-free energy, and ultimately lowered the reaction barrier for the deposition and insertion of zinc ions[74]. The Zn-MnO2 battery using 1% TAC with ZnSO4 exhibited excellent discharge capacities of 288.1, 254.7, 221.5, 202.0, 188.3, and
Figure 6. (A) CV curves of 0% TAC and 1% TAC at a scan rate of 1 mV s-1; discharge capacity and the corresponding coulombic efficiency of the battery using ZnSO4 at (B) different current densities, (C) 1 C, (D) 5 C and using 2 M Zn(CF3SO3)2 as the electrolyte at (E) different current densities, (F) 1 C, (G) 5 C, respectively.
CONCLUSIONS
By regulating cellulose with TA, we obtained a polymer electrolyte membrane of 1% TAC, which possessed a three-dimensional porous network and dense structure with abundant phenolic hydroxyls. Additionally, the 1% TAC delivered a high liquid retention rate at 5 MPa and protected both the front and back surfaces of the zinc foil from corrosion by the electrolyte. Supported by the excellent electrochemical properties mentioned above and simulation calculations, this strategy has proven to be an efficient way to reduce the hydroxyl groups on the surface of cellulose and increase the quantity of phenolic hydroxyl groups, which suppressed the reaction of the polymer electrolyte and Zn2+, and subsequently demonstrated a lower desolvation energy during the plating/stripping process of Zn2+ as well as a lower overpotential. Remarkably, these advantages were beneficial to the uniform distribution of Zn2+ on the surface of the anode, the alleviated zinc dendrite, and the prolonged life of the Zn-MnO2 battery. This novel method has been demonstrated to be an effective strategy for the design and fabrication of high-performance polymer electrolyte membranes for ZIBs, and offers a viable path to assemble other batteries with excellent performance.
DECLARATIONS
Authors’ contributions
Writing-original draft, data curation, formal analysis, methodology, investigation, funding acquisition: Deng, Q.
Validation, visualization: Zhou, W.
Data curation, resources: Wang, H.
Formal analysis, investigation: Ma, Q.
Project administration, funding acquisition, software conceptualization: Li, C.
Project administration, supervision, methodology: Wu, X.
Project administration, data curation, writing-review & editing: Wu, Y.
Availability of data and materials
The data supporting our work can be found in the Supplementary Materials.
Financial support and sponsorship
This work was financially supported by the National Natural Science Foundation of China (Grant No. 52103053), Outstanding Youth Fund of Hunan Provincial Forestry Bureau (XLK202448), Huxiang Young Talents of Hunan Province (Grant No. 2022RC1004), Natural Science Foundation of Henan (Grant No. 232300420404), Special Project for Forestry Science and Technology Innovation of Hunan Province (Grant No. XLKY202205), the Innovation Demonstration Project of Chenzhou City (Grant No.2022sfq53), Major Science and Technology Innovation Platform Project (Grant No. 2022PT1004) and State Key Laboratory Open Research Project (Grant No. GZKF202219).
Conflict of Interest
Prof. Wu, Y. serves as the Editor-in-Chief of Energy Materials, and Prof. Wu, X. is a member of the journal's Editorial Board. However, neither Wu, Y. nor Wu, X. participated in any editorial decisions, including reviewer selection, manuscript handling, or final evaluations related to this work, while the other authors have declared that they have no conflicts of interest.
Ethical approval and consent to participate
Not applicable.
Consent for publication
Not applicable.
Copyright
© The Author(s) 2025.
Supplementary Materials
REFERENCES
1. Liu, S.; Zhang, R.; Wang, C.; et al. Zinc ion batteries: bridging the gap from academia to industry for grid-scale energy storage. Angew. Chem. Int. Ed. 2024, 63, e202400045.
2. Luo, C.; Lei, H.; Xiao, Y.; et al. Recent development in addressing challenges and implementing strategies for manganese dioxide cathodes in aqueous zinc ion batteries. Energy. Mater. 2024, 4, 400036.
3. Li, J.; Liang, H. Organic cathode materials for aqueous zinc-organic batteries. Energy. Mater. 2024, 4, 400033.
4. Cui, Y.; Ding, Y.; Guo, L.; et al. Ultra-long Zn3V2O7(OH)2·2H2O nanowires grown on carbon cloth as cathode material for aqueous zinc-ion batteries. Energy. Mater. 2023, 3, 300023.
5. Miao, L.; Guo, Z.; Jiao, L. Insights into the design of mildly acidic aqueous electrolytes for improved stability of Zn anode performance in zinc-ion batteries. Energy. Mater. 2023, 3, 300014.
6. Han, M.; Chen, D.; Lu, Q.; Fang, G. Aqueous rechargeable Zn-iodine batteries: issues, strategies and perspectives. Small 2024, 20, e2310293.
7. Li, G.; Sun, L.; Zhang, S.; et al. Developing cathode materials for aqueous zinc ion batteries: challenges and practical prospects. Adv. Funct. Mater. 2024, 34, 2301291.
8. Ma, Q.; Ma, A.; Lv, S.; et al. Regulating zinc ion transport behavior and solvated structure towards stable aqueous Zn metal batteries. J. Energy. Chem. 2024, 93, 609-26.
9. Qian, Y.; Chen, L. Interfacial engineering of manganese-based oxides for aqueous zinc-ion batteries: Advances, mechanisms, challenges and perspectives. J. Energy. Chem. 2024, 99, 553-79.
10. Guo, Y.; Liu, C.; Xu, L.; et al. A cigarette filter-derived nitrogen-doped carbon nanoparticle coating layer for stable Zn-ion battery anodes. Energy. Mater. 2022, 2, 200032.
11. Zhu, Q.; Sun, G.; Qiao, S.; et al. Selective shielding of the (002) plane enabling vertically oriented zinc plating for dendrite-free zinc anode. Adv. Mater. 2024, 36, e2308577.
12. Yuan, Y.; Pu, S. D.; Pérez-Osorio, M. A.; et al. Diagnosing the electrostatic shielding mechanism for dendrite suppression in aqueous zinc batteries. Adv. Mater. 2024, 36, e2307708.
13. Tu, W.; Liang, S.; Song, L.; Wang, X.; Ji, G.; Xu, J. Nanoengineered functional cellulose ionic conductor toward high- performance all-solid-state zinc-ion battery. Adv. Funct. Mater. 2024, 34, 2316137.
14. Ge, H.; Xie, X.; Xie, X.; et al. Critical challenges and solutions: quasi-solid-state electrolytes for zinc-based batteries. Energy. Environ. Sci. 2024, 17, 3270-306.
15. Zhang, B.; Cai, X.; Li, J.; et al. Biocompatible and stable quasi-solid-state zinc-ion batteries for real-time responsive wireless wearable electronics. Energy. Environ. Sci. 2024, 17, 3878-87.
16. Liu, C.; Xu, W.; Zhang, L.; et al. Electrochemical hydrophobic tri-layer interface rendered mechanically graded solid electrolyte interface for stable zinc metal anode. Angew. Chem. Int. Ed. 2024, 63, e202318063.
17. Cui, Y.; Chen, W.; Xin, W.; et al. Gradient quasi-solid electrolyte enables selective and fast ion transport for robust aqueous zinc-ion batteries. Adv. Mater. 2024, 36, e2308639.
18. Wang, J.; Peng, J.; Huang, W.; et al. Enabling stable Zn anode with PVDF/CNTs nanocomposites protective layer toward high-performance aqueous zinc-ion batteries. Adv. Funct. Mater. 2024, 34, 2316083.
19. Lee, Y.; Jeoun, Y.; Kim, J. H.; et al. Selective ion transport layer for stable aqueous zinc-ion batteries. Adv. Funct. Mater. 2024, 34, 2310884.
20. Liu, Z.; Guo, Z.; Fan, L.; et al. Construct robust epitaxial growth of (101) textured zinc metal anode for long life and high capacity in mild aqueous zinc-ion batteries. Adv. Mater. 2024, 36, e2305988.
21. Wu, T.; Hu, C.; Zhang, Q.; et al. Helmholtz plane reconfiguration enables robust zinc metal anode in aqueous zinc-ion batteries. Adv. Funct. Mater. 2024, 34, 2315716.
22. Al-Abbasi, M.; Zhao, Y.; He, H.; et al. Challenges and protective strategies on zinc anode toward practical aqueous zinc-ion batteries. Carbon. Neutral. 2024, 3, 108-41.
23. Wang, Z.; Zhou, D.; Zhou, Z.; et al. Synergistic effect of 3D elastomer/super-ionic conductor hybrid fiber networks enables zinc anode protection for aqueous zinc-ion batteries. Adv. Funct. Mater. 2024, 34, 2313371.
24. Zhu, Y.; Liang, G.; Cui, X.; et al. Engineering hosts for Zn anodes in aqueous Zn-ion batteries. Energy. Environ. Sci. 2024, 17, 369-85.
25. Yan, K.; Fan, Y.; Hu, F.; et al. A “polymer-in-salt” solid electrolyte enabled by fast phase transition route for stable Zn batteries. Adv. Funct. Mater. 2024, 34, 2307740.
26. Li, Y.; Yang, X.; He, Y.; et al. A novel ultrathin multiple-kinetics-enhanced polymer electrolyte editing enabled wide-temperature fast-charging solid-state zinc metal batteries. Adv. Funct. Mater. 2024, 34, 2307736.
27. Ji, S.; Luo, H.; Qin, S.; et al. Component fluctuation modulated gelation effect enable temperature adaptability in zinc-ion batteries. Adv. Energy. Mater. 2024, 14, 2400063.
28. Wang, Y.; Li, Q.; Hong, H.; et al. Lean-water hydrogel electrolyte for zinc ion batteries. Nat. Commun. 2023, 14, 3890.
29. Qi, R.; Tang, W.; Shi, Y.; et al. Gel polymer electrolyte toward large-scale application of aqueous zinc batteries. Adv. Funct. Mater. 2023, 33, 2306052.
30. He, Q.; Chang, Z.; Zhong, Y.; et al. Highly entangled hydrogel enables stable zinc metal batteries via interfacial confinement effect. ACS. Energy. Lett. 2023, 8, 5253-63.
31. Yan, Y.; Duan, S.; Liu, B.; et al. Tough hydrogel electrolytes for anti-freezing zinc-ion batteries. Adv. Mater. 2023, 35, e2211673.
32. Chinnakutti, K. K.; Treerittiwittaya, W.; Gao, H.; Tapia-Ruiz, N.; Kidkhunthod, P.; Kasemchainan, J. Solid-state Zn-ion batteries using composite cellulose polyethylene oxide materials-Illustration of reaction and capacity fading mechanisms. Polymer 2024, 299, 126949.
33. Chen, Y.; Zhao, J.; Wang, Y. Quasi-solid-state zinc ion rechargeable batteries for subzero temperature applications. ACS. Appl. Energy. Mater. 2020, 3, 9058-65.
34. Yang, Z.; Zhang, Q.; Wu, T.; et al. Thermally healable electrolyte-electrode interface for sustainable quasi-solid zinc-ion batteries. Angew. Chem. Int. Ed. 2024, 63, e202317457.
35. Wang, N.; Liu, H.; Sun, M.; et al. Achieving wide-temperature-range sustainable zinc-ion batteries via magnesium-doped cathodes and gel electrolytes. ACS. Sustain. Chem. Eng. 2024, 12, 3527-37.
36. Xu, L.; Meng, T.; Zheng, X.; et al. Nanocellulose-carboxymethylcellulose electrolyte for stable, high-rate zinc-ion batteries. Adv. Funct. Mater. 2023, 33, 2302098.
37. Li, W.; Wang, Y.; Liu, R.; Chen, W.; Zhang, H.; Zhang, Z. Gel polymer-based composite solid-state electrolyte for long-cycle-life rechargeable zinc-air batteries. ACS. Sustain. Chem. Eng. 2023, 11, 3732-9.
38. Ma, R.; Xu, Z.; Wang, X. Polymer hydrogel electrolytes for flexible and multifunctional zinc-ion batteries and capacitors. Energy. Environ. Mater. 2023, 6, e12464.
39. Yang, L.; Fu, Y.; Liu, H.; Nie, Q.; Zhang, M.; Shen, Z. Investigating the zinc deposition behavior in aqueous zinc-ion batteries with PEG/cellulose/ZnCl2 water-in-salt electrolytes via a homemade visualized three-electrode tubular cell. ACS. Sustain. Chem. Eng. 2023, 11, 10311-23.
40. Li, Y.; Yang, S.; You, Y.; et al. Cellulose nanocrystals built multiscale hydrogel electrolyte for highly reversible all-flexible zinc ion batteries. Chem. Eng. J. 2024, 496, 154357.
41. Lim, G. J. H.; Koh, J. J.; Chan, K. K.; et al. Amorphous cellulose electrolyte for long life and mechanically robust aqueous structural batteries. Adv. Funct. Mater. 2024, 34, 2313531.
42. Han, X.; Chen, L.; Yanilmaz, M.; et al. From nature, requite to nature: bio-based cellulose and its derivatives for construction of green zinc batteries. Chem. Eng. J. 2023, 454, 140311.
43. Zhang, H.; Gan, X.; Yan, Y.; Zhou, J. A sustainable dual cross-linked cellulose hydrogel electrolyte for high-performance zinc-metal batteries. Nanomicro. Lett. 2024, 16, 106.
44. Li, H.; Han, C.; Huang, Y.; et al. An extremely safe and wearable solid-state zinc ion battery based on a hierarchical structured polymer electrolyte. Energy. Environ. Sci. 2018, 11, 941-51.
45. Gaussian 16 Rev. C.01/C.02 release notes. Available from: https://gaussian.com/relnotes/ [Last accessed on 16 May 2025]
46. Stephens, P. J.; Devlin, F. J.; Chabalowski, C. F.; Frisch, M. J. Ab initio calculation of vibrational absorption and circular dichroism spectra using density functional force fields. J. Phys. Chem. 1994, 98, 11623-7.
47. Krishnan, R.; Binkley, J. S.; Seeger, R.; Pople, J. A. Self-consistent molecular orbital methods. XX. A basis set for correlated wave functions. J. Chem. Phys. 1980, 72, 650-4.
48. Grimme, S.; Ehrlich, S.; Goerigk, L. Effect of the damping function in dispersion corrected density functional theory. J. Comput. Chem. 2011, 32, 1456-65.
49. Dolg, M.; Wedig, U.; Stoll, H.; Preuss, H. Energy-adjusted ab initio pseudopotentials for the first row transition elements. J. Chem. Phys. 1987, 86, 866-72.
50. Pritchard, B. P.; Altarawy, D.; Didier, B.; Gibson, T. D.; Windus, T. L. New basis set exchange: an open, up-to-date resource for the molecular sciences community. J. Chem. Inf. Model. 2019, 59, 4814-20.
51. Tomasi, J.; Mennucci, B.; Cammi, R. Quantum mechanical continuum solvation models. Chem. Rev. 2005, 105, 2999-3093.
52. Lu, T.; Chen, F. Multiwfn: a multifunctional wavefunction analyzer. J. Comput. Chem. 2012, 33, 580-92.
53. Lu, T.; Manzetti, S. Wavefunction and reactivity study of benzo[a]pyrene diol epoxide and its enantiomeric forms. Struct. Chem. 2014, 25, 1521-33.
54. Lu, T.; Chen, F. Quantitative analysis of molecular surface based on improved Marching Tetrahedra algorithm. J. Mol. Graph. Model. 2012, 38, 314-23.
55. Zhang, J.; Lu, T. Efficient evaluation of electrostatic potential with computerized optimized code. Phys. Chem. Chem. Phys. 2021, 23, 20323-8.
56. Humphrey, W.; Dalke, A.; Schulten, K. VMD: visual molecular dynamics. J. Mol. Graph. 1996, 14, 33-8.
57. Grimme, S.; Antony, J.; Ehrlich, S.; Krieg, H. A consistent and accurate ab initio parametrization of density functional dispersion correction (DFT-D) for the 94 elements H-Pu. J. Chem. Phys. 2010, 132, 154104.
58. Zhao, Y.; Truhlar, D. G. The M06 suite of density functionals for main group thermochemistry, thermochemical kinetics, noncovalent interactions, excited states, and transition elements: two new functionals and systematic testing of four M06-class functionals and 12 other functionals. Theor. Chem. Account. 2008, 120, 215-41.
59. Weigend, F.; Ahlrichs, R. Balanced basis sets of split valence, triple zeta valence and quadruple zeta valence quality for H to Rn: Design and assessment of accuracy. Phys. Chem. Chem. Phys. 2005, 7, 3297-305.
60. Marenich, A. V.; Cramer, C. J.; Truhlar, D. G. Universal solvation model based on solute electron density and on a continuum model of the solvent defined by the bulk dielectric constant and atomic surface tensions. J. Phys. Chem. B. 2009, 113, 6378-96.
61. Lv, D.; Chai, J.; Wang, P.; et al. Pure cellulose lithium-ion battery separator with tunable pore size and improved working stability by cellulose nanofibrils. Carbohydr. Polym. 2021, 251, 116975.
62. Chen, S.; Jang, H.; Wang, J.; Qin, Q.; Liu, X.; Cho, J. Bimetallic metal-organic framework-derived MoFe-PC microspheres for electrocatalytic ammonia synthesis under ambient conditions. J. Mater. Chem. A. 2020, 8, 2099-104.
63. Fernández, S.; Mercado, A.; Cuara, E.; Yeverino-miranda, C.; Sierra, U. Asphalt as raw material of graphene-like resources. Fuel 2019, 241, 297-303.
64. Romero-sarria, F.; Bobadilla, L.; Jiménez, B. E.; Odriozola, J. Experimental evidence of HCO species as intermediate in the fischer tropsch reaction using operando techniques. Appl. Catal. B. Environ. 2020, 272, 119032.
65. Ma, M.; Dai, L.; Xu, J.; Liu, Z.; Ni, Y. A simple and effective approach to fabricate lignin nanoparticles with tunable sizes based on lignin fractionation. Green. Chem. 2020, 22, 2011-7.
66. Yu, B.; Park, K.; Jang, J.; Goodenough, J. B. Cellulose-based porous membrane for suppressing Li dendrite formation in lithium-sulfur battery. ACS. Energy. Lett. 2016, 1, 633-7.
67. Adams, R. A.; Varma, A.; Pol, V. G. Mechanistic elucidation of thermal runaway in potassium-ion batteries. J. Power. Sources. 2018, 375, 131-7.
68. Ouyang, Q.; Wang, X.; Wang, X.; Huang, J.; Huang, X.; Chen, Y. Simultaneous DSC/TG analysis on the thermal behavior of PAN polymers prepared by aqueous free-radical polymerization. Polym. Degrad. Stabil. 2016, 130, 320-7.
69. Zhang, X. Q.; Chen, X.; Cheng, X. B.; et al. Highly stable lithium metal batteries enabled by regulating the solvation of lithium ions in nonaqueous electrolytes. Angew. Chem. Int. Ed. 2018, 57, 5301-5.
70. Yu, H.; Chen, Y.; Wang, H.; et al. Engineering multi-functionalized molecular skeleton layer for dendrite-free and durable zinc batteries. Nano. Energy. 2022, 99, 107426.
71. Tie, Z.; Liu, L.; Deng, S.; Zhao, D.; Niu, Z. Proton insertion chemistry of a zinc-organic battery. Angew. Chem. Int. Ed. 2020, 59, 4920-4.
72. Ye, Z.; Xie, S.; Cao, Z.; et al. High-rate aqueous zinc-organic battery achieved by lowering HOMO/LUMO of organic cathode. Energy. Storage. Mater. 2021, 37, 378-86.
73. Chen, Z.; Cui, H.; Hou, Y.; et al. Anion chemistry enabled positive valence conversion to achieve a record high-voltage organic cathode for zinc batteries. Chem 2022, 8, 2204-16.
Cite This Article
How to Cite
Download Citation
Export Citation File:
Type of Import
Tips on Downloading Citation
Citation Manager File Format
Type of Import
Direct Import: When the Direct Import option is selected (the default state), a dialogue box will give you the option to Save or Open the downloaded citation data. Choosing Open will either launch your citation manager or give you a choice of applications with which to use the metadata. The Save option saves the file locally for later use.
Indirect Import: When the Indirect Import option is selected, the metadata is displayed and may be copied and pasted as needed.
About This Article
Copyright
Data & Comments
Data
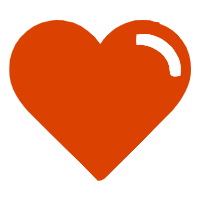
Comments
Comments must be written in English. Spam, offensive content, impersonation, and private information will not be permitted. If any comment is reported and identified as inappropriate content by OAE staff, the comment will be removed without notice. If you have any queries or need any help, please contact us at [email protected].