Li2SO4 coating for enhanced electrochemical performance of Co-free, Li-rich layered oxide cathode
Abstract
In the continued evolution toward high-performance lithium (Li)-ion batteries, cobalt (Co) has presented itself as a major obstacle due to its price, toxicity and supply. Thus, Co-free, Li-rich layered oxide cathodes (CF-LLC) have garnered interest for their exclusion of cobalt and high theoretical capacity. Nevertheless, CF-LLC suffers from issues such as sluggish kinetics, voltage fade and low early capacity due to the increase in cation mixing resulting from the absence of cation-ordering cobalt. To mitigate this, a sulfate coating was applied to the cathode carbonate precursor prior to lithiation, resulting in the formation of a Li2SO4-coated CF-LLC. The Li2SO4 coating prevents the agglomeration of primary particles during lithiation, thereby reducing the primary particle sizes. As a result, Li diffusion pathways are shortened, enhancing Li diffusivity. The coating also prevents transition metal dissolution by acting as a protective barrier against electrolytic reactions. With the Li2SO4 coating, first cycle capacity increased from 205.1 mAh∙g-1 to 259.0 mAh∙g-1, and first cycle Coulombic efficiency also increased from 76.6% to 83.6%. Moreover, after 100 cycles, the Li2SO4-coated sample showed a good 84.7% capacity retention and an improved average voltage fade per cycle of 2.79 mV.
Keywords
INTRODUCTION
Over the past decades, lithium-ion batteries (LIB) have become a primary focus of research in the field of secondary batteries due to their applicability especially in the electric vehicle (EV) market. In this market, specific attention has been placed into increasing the energy density of LIBs in order to increase the driving range[1-3]. Li-rich layered oxide cathodes (LLCs) are one of the candidates as a high-performance LIB cathode material due to their high practical specific capacity (~250 mAh∙g-1) and high operating midpoint voltage (MPV) (~3.6 V)[4]. Consequently, LLCs exhibit some of the highest energy density in layered oxide cathode materials. This can be explained by the structure of LLCs, where there are excess lithium ions in the transition metal (TM) layer, allowing the theoretical capacity to be greater than that of conventional layered oxide cathodes[5].
Due to the rising price of Co and controversy surrounding its toxicity and supply, recent efforts have focused on excluding Co from the typical nickel-cobalt-manganese (NCM) TM blend to produce Co-free, layered oxide cathodes[6-8]. Such trends have crossed over to the field of LLC research, making Co-free LLCs (CF-LLCs) also a new research topic of interest[9]. CF-LLCs offer cheaper yet easier-to-produce batteries without sacrificing theoretical capacity.
However, previous research has shown that the CF-LLCs also suffer from the typical issues that plague LLCs, such as rapid structural degradation. Upon performing charge/discharge cycles, the layered oxide phase shifts to a less ordered spinel structure, and then to a rocksalt structure in its finality[10]. As a result, the mid-point discharge voltage decays, leading to a loss in specific energy. Moreover, Co offers the highest electrical conductivity among the TMs, and acts as a structure stabilizer in the TM blend, reducing cation disordering[11]. Due to the exclusion of Co, CF-LLCs exhibit reduced electrical conductivity and lower Li diffusivity[12], leading to significantly worse early cycle capacity compared to conventional LLCs.
Attempts have been made to alleviate these issues through various cathode modification techniques. In particular, LLCs have been coated with oxides, fluorides, phosphates and conductive materials
In this study, we introduce a novel, dual-function coating strategy designed to simultaneously improve the early-cycle capacity of CF-LLCs and suppress undesired interfacial reactions with the electrolyte, as outlined in the schematic in Supplementary Figure 1. Lithium sulfate (Li2SO4) was selected as the coating material due to its ability not only to prevent primary particle agglomeration during annealing, but also to form in situ through a reaction of the sulfate precursor with Li species, resulting in a uniform and protective coating. Additionally, the use of nickel sulfate hexahydrate - a readily available and water-soluble TM
The effects of Li2SO4 coating layers on the structural and interfacial properties of LLCs were thoroughly investigated before and after electrochemical cycling. To elucidate the morphological, compositional, and surface chemical changes, comprehensive characterization techniques were employed including scanning electron microscopy (SEM), energy-dispersive X-ray spectroscopy (EDS), high-angle annular dark-field scanning transmission electron microscopy (HAADF-STEM), X-ray photoelectron spectroscopy (XPS), attenuated total reflectance Fourier transform infrared spectroscopy (ATR-FTIR), X-ray diffraction (XRD), time-of-flight secondary ion mass spectrometry (TOF-SIMS) and Raman spectroscopy. In parallel, electrochemical analyses such as galvanostatic cycling, electrochemical impedance spectroscopy (EIS), differential capacity analysis (dQ/dV) and galvanostatic intermittent titration technique (GITT) were conducted to evaluate the functional role of the coating in enhancing Li+ diffusion kinetics, interfacial stability, and overall electrochemical performance.
EXPERIMENTAL
Material synthesis
Synthesis of CF-LLC
CF-LLC was synthesized using a hydrothermal method. Stoichiometric amounts of manganese acetate tetrahydrate, [Mn(CH3COO)2·4H2O, Sigma Aldrich] and nickel Acetate tetrahydrate [Ni(OCOCH3)2·4H2O, Sigma Aldrich] were added to a Teflon liner along with urea (CH4N2O, Junsei) and 50 mL solution mixture of deionized (DI) water and anhydrous ethyl alcohol (C2H6O, 99.9%, Samchun). The liner was placed in a stainless steel autoclave, sealed shut and heated in a convection oven to 200 °C for 12 h. The resulting mixture was then vacuum filtered with anhydrous ethyl alcohol (C2H6O, 99.9%, Samchun) and then dried overnight at 80 °C in a convection oven. The dried powder was then finely mixed in an agate mortar to produce the carbonate powder.
The carbonate was then mixed with stoichiometric amounts of lithium carbonate (Li2CO3, Samchun) in an agate mortar and then pressed in a pellet mold. The resulting pellet was then placed in an alumina combustion boat and annealed in a tube furnace at 450 °C for 2 h and then at 900 °C for 12 h under constant airflow to produce CF-LLC.
Synthesis of Li2SO4-coated CF-LLC
For the synthesis of Li2SO4-coated CF-LLC (S-CF-LLC), DI water and the carbonate powder were mixed in a 2:1 wt ratio along with 6 wt% of nickel sulfate hexahydrate (NiSO4·6H2O, Samchun) in a glass vial. After placing a magnetic stirring bar inside, the mixture was then placed on a stirrer/hotplate and dried overnight. The resulting coated carbonate mixture was then lithiated in the same process as above to produce
The full synthesis schematic for CF-LLC and S-CF-LLC is outlined in Supplementary Figure 2.
Material characterization
To examine the particle surface and primary particle size, SEM images were collected (SU5000, Hitachi). SEM-energy dispersive X-ray spectroscopy (SEM-EDS) data was collected in order to confirm the presence of the sulfate coating (Octane Elect EDS detector, EDAX). Primary particle size measurements were also performed to show the particle size distribution of each sample (ImageJ). Inductively coupled plasma optical emission spectroscopy was performed to examine the chemical composition of each sample
Electrochemical measurements
To evaluate the electrochemical performance of CF-LLC and S-CF-LLC, the cathode active materials (CAM) were mixed with Super-P carbon black powder and polyvinylidene fluoride (PVDF) in an 8:1:1 weight ratio in an agate mortar. After thorough mixing, 800 μL of N-Metyl-2-pyrrolidine (NMP, Sigma Aldrich) was added to form a slurry. This slurry mixture was placed on Al foil and then doctor bladed at approximately 200 μm thickness and then dried overnight at 80 °C in a vacuum oven. The resulting cathode film was punched using a 10 mm film punch to form circular films. The circular films were then pressed using a flat mold at 3000 psi for 10 sec before being place inside the glovebox for cell assembly. Coin cell 2032 was constructed using premade 2032 coin cell parts (bottom/top cap, gasket, spring, 1t spacer) with a lithium metal chip as the counter-electrode, 2 layers of polypropylene film as the separator and 200 μL of 1M LiPF6 ethylene carbonate:diethyl carbonate (EC:DEC) as the electrolyte.
The coin cells were tested in a WBCS3000S (WonATech) test system for galvanostatic cycling. The coin cells were put through charge/discharge cycles at a voltage range of 2.0~4.8 V at 0.1 C for the first cycle followed by subsequent cycles at various 0.2 C for 99 cycles for a total of 100 cycles. All cycles were performed in a LCH-11-2C (Jeiotech) temperature chamber with the temperature set to 25 °C. dQ/dV was carried out using the IVMAN differential analysis software (WonATech). GITT analysis was also performed at 10 min current pulses of 0.2 C current followed by 4hr rest cycles. EIS was performed using a VersaSTAT4 (AMETEK) with a voltage amplitude of 10 mV and a frequency range of 106 Hz to 10-3 Hz. EIS fitting was performed using ZMAN (Zive Lab).
RESULTS AND DISCUSSION
Characterization of CF-LLC and S-CF-LLC
To synthesize a CF-LLC, a carbonate precursor was prepared and lithiated. For the S-CF-LLC, the prepared carbonate precursor was immersed in an aqueous nickel sulfate (NiSO4) solution prior to lithiation
Figure 1. (A) XRD Patterns of CF-LLC and S-CF-LLC with (003) peak inset and corresponding PDF of Li1.2Mn0.6Ni0.2O2 and Li2MnO3; High-magnification SEM images of primary particles of (B) CF-LLC and (C) S-CF-LLC and the corresponding primary particle size distribution of (D) CF-LLC and (E) S-CF-LLC. XRD: X-ray diffraction; SEM: scanning electron microscopy; CF-LLC: Co-free, Li-rich layered oxide cathodes; S-CF-LLC: Li2SO4-coated CF-LLC.
SEM images [Supplementary Figure 4A and B] show that both samples consist of spherical secondary particles with diameters of approximately 3~4 μm, though larger secondary particles have been observed up to 10 μm. Notably, S-CF-LLC exhibits smaller primary particles [Figure 1B and C] with an average particle size of 131 nm, compared to 213 nm for C-F-LLC [Figure 1D and E]. These results suggest that the sulfate coating effectively suppressed the agglomeration of primary particles during the lithiation process. Seeing as most of the primary particles in S-CF-LLC fall in the range of 100~150 nm, smaller than the 150~250 nm range observed for CF-LLC, the coating likely formed at the primary particle level, thereby significantly reducing their size.
EDS mapping images [Figure 2A and B] display a uniform distribution of TMs (Mn, Ni) in both samples. Notably, S-CF-LLC reveals distinct sulfur (S) signals, while CF-LLC exhibits S signals indistinguishable from the background. The EDS spectrum [Supplementary Figure 5A and B] confirms the presence of S Kα1 peak only in S-CF-LLC. CF-LLC comprises 0.0 atm% S, 0.6 atm% Ni, 3.0 atm% Mn and 33.3 atm% O, while S-CF-LLC contains 0.1 atm% S, 1.2 atm% Ni, 3.8 atm% Mn and 40.8 atm% O [Supplementary Table 3]. As SEM-EDS does not give us accurate chemical stoichiometries, chemical compositions were also determined using ICP-OES, assuming stoichiometry for Li and O as 1.2 due to the difficulty in accurately measuring these elements with ICP-OES[27]. Sulfur was omitted from ICP-OES measurements due to challenges such as low sensitivity, spectral interferences and volatility in the plasma[28]. As shown in Supplementary Table 4, both samples show chemical compositions closely aligned with the stoichiometry of Li1.2Mn0.6Ni0.2O2.
Figure 2. SEM-EDS images of (A) CF-LLC and (B) S-CF-LLC and their corresponding EDS mapping images; (C) XPS S 2p surface spectra of CF-LLC and S-CF-LLC; (D) XPS Li 1s surface spectra of CF-LLC and S-CF-LLC. SEM-EDS: Scanning electron microscopy-energy dispersive X-ray spectroscopy; CF-LLC: Co-free, Li-rich layered oxide cathodes; XPS: X-ray photoelectron spectroscopy;
To further investigate the chemical state and distribution of sulfur in S-CF-LLC, S 2p XPS spectra were collected and compared with CF-LLC [Figure 2C]. S-CF-LLC displays a clear peak at binding energy of around 169.5 eV, corresponding to lithium sulfate (Li2SO4)[29], which is not observed in CF-LLC. In accordance with this, Li 1s XPS spectra [Figure 2D] of S-CF-LLC also show a peak at binding energy of around 55.8 eV, corresponding to Li2SO4[30], which is not present in CF-LLC. Furthermore, the XPS S 2p depth profile with 40 sec etching time intervals [Supplementary Figure 6] demonstrates that the sulfate peak intensity decreases with increasing etching time, indicating that sulfate exists only as a surface coating layer and not within the bulk. Additionally, ATR-FTIR spectra [Supplementary Figure 7] show a distinct peak in the asymmetric S-O stretching mode region for S-CF-LLC, which is absent in CF-LLC, confirming the presence of a sulfate in S-CF-LLC[31].
As discussed above, the smaller primary particle sizes of S-CF-LLC suggest that the sulfate exerts its
Figure 3. (A) HAADF-STEM images of a S-CF-LLC primary particle and the corresponding STEM-EDS mapping images; (B) Line profile EDS and (C) Area profile EDS of the S-CF-LLC primary particle. HAADF-STEM: High-angle annular dark-field scanning transmission electron microscopy; SEM-EDS: scanning electron microscopy-energy dispersive X-ray spectroscopy; S-CF-LLC: Li2SO4-coated CF-LLC.
Electrochemical performance
Figure 4 shows the comprehensive electrochemical performance of CF-LLC, and S-CF-LLC. In the first cycle [Figure 4A], CF-LLC exhibits a reduced specific discharge capacity (SC) of 205.1 mAh∙g-1 and a Coulombic efficiency (CE) of 76.6%, attributed to the exclusion of Co, which results in lowered kinetics such as reduced electronic conductivity and a higher degree of disordering[11,12]. In contrast, S-CF-LLC outperforms CF-LLC, delivering a SC of 259.0 mAh∙g-1 and a CE of 83.6%. The superior performance of
Figure 4. Electrochemical performance charts of LLC, CF-LLC and S-CF-LLC: (A) 1st cycle charge-discharge curves; (B) specific discharge capacity across 100 cycles; (C) Coulombic efficiency across 100 cycles; (D) midpoint voltage across 100 cycles; (E) specific discharge energy across 100 cycles; (F) Rate capability test of CF-LLC and S-CF-LLC. C-rate was increased sequentially from 0.1, 0.2, 0.5, 1, 2 C with 5 cycles per C-rate, after which the C-rate was returned to 0.1 C. CF-LLC: Co-free, Li-rich layered oxide cathodes;
Figure 4B and C shows the SC and CE over 100 cycles for CF-LLC and S-CF-LLC. After 100 cycles, CF-LLC exhibits a relatively low specific discharge capacities of 175.2 mAh∙g-1, corresponding to capacity retention of 96.0% (calculated from the second cycle), respectively. In contrast, S-CF-LLC maintains a high SC of 210.5 mAh∙g-1 whilst maintaining a good 84.7% capacity retention. The high capacity retention of CF-LLC can be attributed to the sluggish kinetics, which results in a partially realized first cycle oxygen plateau and suppression of TM migration[34]. Moreover, the lower charge capacity indicates that CF-LLC hardly undergoes deep delithiation due to ist sluggish kinetics. As a result, CF-LLS experiences reduced volume change and thus, is less susceptable to capacity decaying issues such as cracking and the formation of stacking faults[35]. However, this capacity retention comes at the expense of SC, which hinders the viability of CF-LLC as a high energy density cathode material. In contrast, S-CF-LLC offers a more favorable balance between high SC and good capacity retention, making it a more promising candidate for practical applications.
Both CF-LLC and S-CF-LLC also exhibited a high average CE of > 99% (calculated from the second cycle) over 100 cycles with S-CF-LLC showing a slight improvement of 99.2% over 99.1% of CF-LLC, indicating better reversibility of the Li+ intercalation/de-intercalation process.
Voltage fade results from both bulk structural degradation and surface degradation. Oxygen release at the surface during the first cycle can induce TM migration, which can contribute to voltage decay[4,36]. Moreover, uncoated cathode surfaces are susceptible to hydrogen fluoride (HF) etching, leading to TM dissolution and formation of unstable, thick CEI layers, that can increase overpotential and thus, lower the discharge voltage[37,38]. Therefore, to evaluate voltage fade[36] and examine the extent of material degradation, midpoint discharge voltage (MPV) was recorded from the charge-discharge curves over 100 cycles [Figure 4D]. The average change in voltage per cycle (ΔV) was 2.79 mV for S-CF-LLC, which is markedly lower than 3.20 mV for CF-LLC, suggesting reduced structural degradation.
Moreover, while smaller particle sizes typically increase surface area and exacerbate voltage fade[39],
Increasing energy density is one of the key goals in the development of next-generation LIBs. The specific discharge energy density (SE), calculated as the product of SC and MPV[40] (Figure 4E), was 939.0 mWh∙g-1 for S-CF-LLC for the first cycle, significantly higher than that of CF-LLC (734.7 mWh∙g-1) and remained high after 100 cycles at 704.5 mWh∙g-1 compared to 571.5 mWh∙g-1 of CF-LLC.
Finally, rate capability of CF-LLC and S-CF-LLC was evaluated through five charge-discharge cycles at various C-rates (0.1 C, 0.2 C, 0.5 C, 1 C and 2 C in order and then returning to 0.1 C, Figure 4F). S-CF-LLC consistently shows increased SC compared to CF-LLC across all C-rates, with the capacity difference increasing from 47.4 mAh∙g-1 at 0.1 C to 58.9 mAh∙g-1 at 2 C. Extended cycling at high C-rates of 1C and 3C [Supplementary Figure 8A and B] further confirms the superior rate performance of S-CF-LLC, compared to CF-LLC. At 1 C, S-CF-LLC shows an impressive 2nd cycle capacity of 193.4 mAh∙g-1 compared to
Primary particle size reduction effect on electrochemical performance
In many previous studies, reducing primary particle size has been touted as an effective method
Li+ diffusivity was also calculated using EIS to further verify the above findings. Supplementary Figure 12A shows the Nyquist plots of CF-LLC and S-CF-LLC prior to cycling. It can be seen that both samples show similar charge transfer resistance and ohmic resistance, with the only difference seen in the Warburg impedance. The Warburg impedance can then be plotted against the reciprocal of the square root of the angular frequency to obtain the slope which is the Warburg factor[46]. This plot is illustrated in Supplementary Figure 12B, which shows that the Warburg factor for S-CF-LLC is lower than that of
Another commonly used electrochemical analytical technique to examine capacity is dQ/dV which can give insight on the voltage windows where the capacity originates from, and the corresponding redox reactions that are often assigned to these voltage windows. Supplementary Figure 13 shows the dQ/dV plot of
Li2SO4 coating effect and surface degradation analyses
Outside of primary particle size reduction, the other purpose of the dual-effect coating procedure is to create a protective Li2SO4 coating layer at a primary particle level. As surface area increases with the reduction of primary particle size, it is important that surface stability is increased to offset the increase in potential unwanted surface reactions. As Li2SO4 coating layer has been characterized to be successfully synthesized, samples of CF-LLC and S-CF-LLC cathode films prior to and after 100 cycles were prepared for comparison to examine the efficacy of the Li2SO4 coating layer.
XPS analysis of the cathode film prior to and after 100 cycles is illustrated in Figure 5. F 1s spectra of
Figure 5. XPS analysis of (A) CF-LLC F 1s spectra before and after 100 cycles; (B) S-CF-LLC F 1s spectra before and after 100 cycles; (C) CF-LLC O 1s spectra before and after 100 cycles; (D) S-CF-LLC O 1s spectra before and after 100 cycles. XPS: X-ray photoelectron spectroscopy; CF-LLC: Co-free, Li-rich layered oxide cathodes; S-CF-LLC: Li2SO4-coated CF-LLC.
{LiPF}_{6}+{H}_{2}{O} \rightarrow 2 \cdot {LiF}+2 \cdot {HF}+{POF}_{3}
The HF product can then react with the cathode surface in:
{HF}+2 \cdot {LiMO}_{2} \rightarrow 2 \cdot {LiF}+{MF}_{2}+{H}_{2} {O}+{MO}_{2}({M}={Mn},{Ni})
This not only causes the dissolution of TMs (through MF2 formation) causing structural degradation loss in electrochemical performance, but also produces additional water, which can restart the reaction cycle[37,52]. The result is that LiF and MF2 (which have similar binding energy levels) progressively form more and more on the cathode surface whilst reducing performance, causing the LiF/MF2 peak to grow. In contrast to the bare CF-LLC surface, the Li2SO4 coating on the surface of S-CF-LLC can react with HF in:
{HF}+{Li}_{2} {SO}_{4} \rightarrow {LiF}+{LiHSO}_{4}
In contrast to CF-LLC, although this reaction does produce LiF (as seen by the small growth in LiF peak), it does not produce any water, ending the reaction cycle. Thus, due to the chemically protective Li2SO4 coating, S-CF-LLC undergoes less TM dissolution as evidenced by the F 1s spectra. This can be further corroborated by Supplementary Figure 14A and B, which shows reduced Mn3+ and Mn2+ peak growth after 100 cycles for the Mn 2p spectra for S-CF-LLC compared to CF-LLC, showing that the oxidation state of Mn species at the surface is higher due to less surface reactions[53]. Supplementary Figure 14C also shows the presence of Li2SO4 for S-CF-LLC after cycling, indicating that the protective coating is durable. In addition, Supplementary Figure 15A-D shows the Mn 2p and Ni 2p spectra of the lithium metal anode and the PP separator extracted from both CF-LLC and S-CF-LLC half-cells. It has been reported that TMs deposit onto the anode after dissolution[54]. Thus, examining the lithium metal anode and the separator (which are deposited with Li dendrites) can show us the amount of TMs that have dissolved and been deposited on to the lithium metal. Overall, the anode and separator used in S-CF-LLC half cells show much lower Ni 2p and Mn 2p signals compared to CF-LLC, indicating that less TM dissolution has occurred due to the protective Li2SO4 coating layer.
O 1s spectra of CF-LLC and S-CF-LLC [Figure 5C and D] also show the effect of the Li2SO4 coating on the surface prior to and after cycling. Prior to cycling, O 1s spectra of both samples show a large main peak that corresponds to the lattice oxygen peak (~530.0 eV). Beyond this main peak, there is a peak attributed to surface oxygen species (~531.8 eV) and CO3/C=O and C-O peaks (~532.5 eV and ~533.6 eV, respectively) that are attributed to cathode residual/CEI species[55]. After 100 cycles, S-CF-LLC shows the enlargement of these surface/CEI species peaks relative to the lattice oxygen peak due to the formation of CEI layers upon cycling. However, this enlargement is much smaller in scale compared to that seen in the CF-LLC spectra after 100 cycles. It has been reported in other works that charging/discharging to high potential can cause instability of the CEI layer and continued formation of CEI species[37]. However, coating layers have been found to mitigate this continued CEI formation, resulting in a lower amount of CEI species detected in the O 1s spectra as seen in the S-CF-LLC spectra[56]. This reduction in CEI species formation from Li2SO4 coating also means reduced electrolyte consumption from decomposition reactions and reduced overall overpotential.
To validate the proposed chemically protective mechanism of Li2SO4, TOF-SIMS analysis was conducted on CF-LLC and S-CF-LLC cathode films before and after 100 charge-discharge cycles. As seen in the surface mass spectra [Figure 6A], whereas no distinct HSO4- peaks around 96.96 m/z were observed in either sample prior to cycling, a prominent HSO4- peak emerges in the S-CF-LLC sample after 100 cycles. These results indicate that the chemical reaction between Li2SO4 and HF occurred to some extent, supporting the chemically protective mechanism of Li2SO4 coating layers[57]. Furthermore, the TOF-SIMS 3D mapping
Figure 6. (A) TOF-SIMS data for CF-LLC and S-CF-LLC prior to and after 100 cycles and the corresponding (B) TOF-SIMS 3D mapping and (C) TOF-SIMS depth profile; (D) Raman spectra for CF-LLC and S-CF-LLC prior to and after 100 cycles. TOF-SIMS: Time-of-flight secondary ion mass spectrometry; CF-LLC: Co-free, Li-rich layered oxide cathodes; S-CF-LLC: Li2SO4-coated CF-LLC.
Raman spectra of CF-LLC and S-CF-LLC were analyzed to examine the structural degradation that may have occurred due to surface TM dissolution. As shown in Figure 6D, both samples show completely overlapping Raman spectra prior to cycling, with LiMO2 peaks at 608 and 492 cm-1 and the Li2MnO3 peak at 435 cm-1 which are characteristic of LLC materials[24]. However, after cycling, CF-LLC Raman spectra show a clear growth of a spinel phase shoulder peak around 605~660 cm-1[24]. This is evidence of structural degradation due to TM dissolution during cycling.
In order to physically observe the worsened structural degradation during cycling, HAADF-STEM images of CF-LLC and S-CF-LLC samples were taken prior to and after 100 cycles. Prior to cycling, both CF-LLC and S-CF-LLC samples exhibit a well-defined layered structure with a similar interlayer spacing of approximately 0.48 nm [Supplementary Figure 16A and B]. In contrast, post-cycling observations reveal structural changes in the surface regions of both samples [Figure 7A and B], while the layered structure in the bulk remains largely preserved. To investigate these structures’ degradation in more detail, FFT was applied to the high-resolution STEM images
Figure 7. HAADF-STEM images of (A) CF-LLC and (B) S-CF-LLC after 100 cycles and the corresponding magnified images/FFT of each phase for (C) CF-LLC and (D) S-CF-LLC. HAADF-STEM: High-angle annular dark-field scanning transmission electron microscopy;
Finally, EIS results show a similar difference in surface degradation with CF-LLC and S-CF-LLC after cycling as presented Supplementary Figure 17A. EIS fitting was performed with the equivalent circuit illustrated in Supplementary Figure 17B, and the resulting film resistance (Rf) and charge transfer resistance (Rct) are presented in
CONCLUSION
In this study, a dual-effect sulfate coating method was explored to improve the electrochemical performance of a CF-LLC. Coating the carbonate precursor material prior to the annealing process produced a cathode material with a Li2SO4 coating layer at the primary particle level that both protects the cathode material and also prevents agglomeration during the annealing process. The prevention of agglomeration resulted in the reduction of cathode primary particle size, improving its kinetics and Li+ diffusivity which were initially sluggish due to the exclusion of Co. Furthermore, the protective Li2SO4 coating layer serves as a chemically protective layer, preventing the continued decomposition of the electrolyte and more importantly, preventing HF attack and in turn, reducing TM dissolution from the surface. Through these modifications, S-CF-LLC exhibited a significantly improved 1st cycle SC of 259.0 mAh∙g-1 and 1st cycle CE of 83.6% compared to both CF-LLC and even Co-inclusive LLC. Beyond the first cycle, S-CF-LLC also demonstrated a good capacity retention of 84.7% after 100 cycles, as well as improved voltage fade, specific discharge energy and rate capability compared to the pristine cathode. In all, this simple and scalable dual-effect coating method potentially opens up the commercial viability and applicability of CF-LLCs that have previously been inadequate due to low electrochemical performance.
DECLARATIONS
Acknowledgments
The authors would like to thank the KAIST Analysis Center for Research Advancement (KARA), and the National NanoFab Center for granting access to their equipment.
Authors’ contributions
First author of this study and led the conceptualization, design, experimental processes, data analyses, data interpretation, data presentation and manuscript writing: Moon, J. H.
Made contributions to conceptualization, data analyses and data interpretation: Kang, H.; Hwang, G.;
Made significant contributions to formal analysis: Kim, G.
Made contributions to data interpretation and manuscript draft: Kang, H.
Corresponding author of this study and provided administrative, technical, and material support as well as contributing to conceptualization, data analyses and data interpretation: Cho, E.
Availability of data and materials
The data supporting this article have been included as part of the Supplementary Materials.
Financial support and sponsorship
This work was supported by the National Research Foundation of Korea (NRF) grant funded by the Korean government (MSIT) (RS-2023-00247245), and by the Korea Institute for Advancement of Technology (KIAT) grant funded by the Korean government (MOTIE) (P0017120, Competency Development Program for Industry Specialists).
Conflicts of interest
All authors declared that there are no conflicts of interest.
Ethical approval and consent to participate
Not applicable.
Consent for publication
Not applicable.
Copyright
© The Author(s) 2025.
Supplementary Materials
REFERENCES
1. Mohammadi, F.; Saif, M. A comprehensive overview of electric vehicle batteries market. e-Prime. Adv. Electr. Eng. Electron. Energy. 2023, 3, 100127.
2. Rangarajan, S. S.; Sunddararaj, S. P.; Sudhakar, A. V. V.; et al. Lithium-ion batteries-the crux of electric vehicles with opportunities and challenges. Clean. Technol. 2022, 4, 908-30.
3. Sankaran, G.; Venkatesan, S. An overview of lithium-ion batteries for electric mobility and energy storage applications. IOP. Conf. Ser.. Earth. Environ. Sci. 2022, 1042, 012012.
4. Xie, Y.; Jin, Y.; Xiang, L. Li-rich layered oxides: structure, capacity and voltage fading mechanisms and solving strategies. Particuology 2022, 61, 1-10.
5. Yan, J.; Liu, X.; Li, B. Recent progress in Li-rich layered oxides as cathode materials for Li-ion batteries. RSC. Adv. 2014, 4, 63268-84.
6. Banza, Lubaba., Nkulu., C.; Casas, L.; Haufroid, V.; et al. Sustainability of artisanal mining of cobalt in DR congo. Nat. Sustain. 2018, 1, 495-504.
8. Sun, Y. K.; Lee, D. J.; Lee, Y. J.; Chen, Z.; Myung, S. T. Cobalt-free nickel rich layered oxide cathodes for lithium-ion batteries. ACS. Appl. Mater. Interfaces. 2013, 5, 11434-40.
9. Ding, X.; Luo, D.; Cui, J.; Xie, H.; Ren, Q.; Lin, Z. An ultra-long-life lithium-rich Li1.2Mn0.6Ni0.2O2 cathode by three-in-one surface modification for lithium-ion batteries. Angew. Chem. Int. Ed. 2020, 59, 7778-82.
10. Kim, S.; Cho, W.; Zhang, X.; Oshima, Y.; Choi, J. W. A stable lithium-rich surface structure for lithium-rich layered cathode materials. Nat. Commun. 2016, 7, 13598.
11. Manthiram, A. A reflection on lithium-ion battery cathode chemistry. Nat. Commun. 2020, 11, 1550.
12. Clément, R. J.; Lun, Z.; Ceder, G. Cation-disordered rocksalt transition metal oxides and oxyfluorides for high energy lithium-ion cathodes. Energy. Environ. Sci. 2020, 13, 345-73.
13. Zhou, C.; Wang, P.; Zhang, B.; et al. Suppressing the voltage fading of Li[Li0.2Ni0.13Co0.13Mn0.54]O2 cathode material via Al2O3 coating for Li-ion batteries. J. Electrochem. Soc. 2018, 165, A1648.
14. Zhai, X.; Zhang, P.; Huang, H.; et al. Surface modification of Li-rich layered Li1.2Mn0.54Ni0.13Co0.13O2 oxide with Fe2O3 as cathode material for Li-ion batteries. Solid. State. Ionics. 2021, 366-7, 115661.
15. Lee, J.; Kang, H.; Moon, J.; et al. Enhancement of the cyclic stability of a Li-excess layered oxide through a simple electrode treatment for LiF-coating. Electrochim. Acta. 2025, 524, 145919.
16. Zhao, T.; Chen, S.; Chen, R.; et al. The positive roles of integrated layered-spinel structures combined with nanocoating in low-cost Li-rich cathode Li[Li0.2Fe0.1Ni0.15Mn0.55]O2 for lithium-ion batteries. ACS. Appl. Mater. Interfaces. 2014, 6, 21711-20.
17. Wang, Y.; Yu, W.; Zhao, L.; et al. AlPO4-Li3PO4 dual shell for enhancing interfacial stability of Co-free Li-rich Mn-based cathode. Electrochim. Acta. 2023, 462, 142664.
18. Sai, L.; Dai, Z.; Wang, Z.; Zhao, H.; Bai, Y. Multiple-functional LiTi2(PO4)3 modification improving long-term performances of Li-rich Mn-based cathode material for advanced lithium-ion batteries. J. Power. Sources. 2024, 613, 234870.
19. Wu, H.; Li, H.; Yang, P.; Xing, Y.; Zhang, S. Surface modification of Li1.2Mn0.6Ni0.2O2 with electronic conducting polypyrrole. Int. J. Electrochem. Sci. 2018, 13, 6930-9.
20. Song, B.; Lai, M. O.; Liu, Z.; Liu, H.; Lu, L. Graphene-based surface modification on layered Li-rich cathode for high-performance Li-ion batteries. J. Mater. Chem. A. 2013, 1, 9954-65.
21. Uzun, D. Boron-doped Li1.2Mn0.6Ni0.2O2 as a cathode active material for lithium ion battery. Solid. State. Ionics. 2015, 281, 73-81.
22. Jiang, W.; Zhang, C.; Feng, Y.; et al. Achieving high structure and voltage stability in cobalt-free Li-rich layered oxide cathodes via selective dual-cation doping. Energy. Storage. Mater. 2020, 32, 37-45.
23. Li, G.; You, L.; Wen, Y.; et al. Ultrathin Li-Si-O Coating layer to stabilize the surface structure and prolong the cycling life of single-crystal LiNi0.6Co0.2Mn0.2O2 cathode materials at 4.5 V. ACS. Appl. Mater. Interfaces. 2021, 13, 10952-63.
24. Celeste, A.; Tuccillo, M.; Santoni, A.; Reale, P.; Brutti, S.; Silvestri, L. Exploring a Co-free, Li-rich layered oxide with low content of nickel as a positive electrode for Li-ion battery. ACS. Appl. Energy. Mater. 2021, 4, 11290-7.
25. Li, Y.; Bai, Y.; Wu, C.; et al. Three-dimensional fusiform hierarchical micro/nano Li1.2Ni0.2Mn0.6O2 with a preferred orientation (110) plane as a high energy cathode material for lithium-ion batteries. J. Mater. Chem. A. 2016, 4, 5942-51.
26. Geng, F.; Wang, L.; Stralka, T.; et al. (111)-oriented growth and acceptor doping of transparent conductive CuI:S thin films by spin coating and radio frequency-sputtering. Adv. Eng. Mater. 2023, 25, 2201666.
27. Kiciński, W.; Dyjak, S. Transition metal impurities in carbon-based materials: pitfalls, artifacts and deleterious effects. Carbon 2020, 168, 748-845.
28. Martínez-sierra J, Galilea San Blas O, Marchante Gayón J, García Alonso J. sulfur analysis by inductively coupled plasma-mass spectrometry: a review. Spectrochim. Acta. B. 2015, 108, 35-52.
29. Wahlqvist, M.; Shchukarev, A. XPS spectra and electronic structure of group IA sulfates. J. Electron. Spectrosc. Relat. Phenom. 2007, 156-158, 310-4.
30. Liao, W.; Liu, H.; Qi, L.; et al. Lithium/bismuth co-functionalized phosphotungstic acid catalyst for promoting dinitrogen electroreduction with high Faradaic efficiency. Cell. Rep. Phys. Sci. 2021, 2, 100557.
31. Lauer, A. R.; Hellmann, R.; Montes-Hernandez, G.; et al. Deciphering strontium sulfate precipitation via Ostwald’s rule of stages: from prenucleation clusters to solution-mediated phase tranformation. J. Chem. Phys. 2023, 158, 054501.
32. Yoon, T.; Soon, J.; Lee, T. J.; Ryu, J. H.; Oh, S. M. Dissolution of cathode-electrolyte interphase deposited on LiNi0.5Mn1.5O4 for lithium-ion batteries. J. Power. Sources. 2021, 503, 230051.
33. Liao, J.; Zhang, Z.; Fan, W.; Wang, Q.; Liao, D. Synchronous construction of oxygen vacancies with suitable concentrations and carbon coating on the surface of Li-rich layered oxide cathode materials by spray drying for Li-ion batteries. Electrochim. Acta. 2022, 405, 139798.
34. Gent, W. E.; Lim, K.; Liang, Y.; et al. Coupling between oxygen redox and cation migration explains unusual electrochemistry in lithium-rich layered oxides. Nat. Commun. 2017, 8, 2091.
35. Singer, A.; Zhang, M.; Hy, S.; et al. Nucleation of dislocations and their dynamics in layered oxide cathode materials during battery charging. Nat. Energy. 2018, 3, 641-7.
36. Abdel-ghany, A.; Hashem, A. M.; Mauger, A.; Julien, C. M. Lithium-rich cobalt-free manganese-based layered cathode materials for Li-ion batteries: suppressing the voltage fading. Energies 2020, 13, 3487.
37. Hirooka, M.; Sekiya, T.; Omomo, Y.; et al. Degradation mechanism of LiCoO2 under float charge conditions and high temperatures. Electrochim. Acta. 2019, 320, 134596.
38. Zhuang, Z.; Wang, J.; Jia, K.; et al. Ultrahigh-voltage LiCoO2 at 4.7 V by interface stabilization and band structure modification. Adv. Mater. 2023, 35, 2212059.
39. Yabuuchi, N.; Kubota, K.; Aoki, Y.; Komaba, S. Understanding particle-size-dependent electrochemical properties of Li2MnO3-based positive electrode materials for rechargeable lithium batteries. J. Phys. Chem. C. 2016, 120, 875-85.
40. Li, Q.; Li, G.; Fu, C.; et al. Balancing stability and specific energy in Li-rich cathodes for lithium ion batteries: a case study of a novel Li-Mn-Ni-Co oxide. J. Mater. Chem. A. 2015, 3, 10592-602.
41. Nitta, N.; Wu, F.; Lee, J. T.; Yushin, G. Li-ion battery materials: present and future. Mater. Today. 2015, 18, 252-64.
42. Choi, H.; Schuer, A. R.; Moon, H.; Kuenzel, M.; Passerini, S. Investigating the particle size effect on the electrochemical performance and degradation of cobalt-free lithium-rich layered oxide Li1.2Ni0.2Mn0.6O2. Electrochim. Acta. 2022, 430, 141047.
43. Gao, D.; Zeng, Z.; Mi, H.; et al. Enhanced structural stability and overall conductivity of Li-rich layered oxide materials achieved by a dual electron/lithium-conducting coating strategy for high-performance lithium-ion batteries. J. Mater. Chem. A. 2019, 7, 23964-72.
44. McClelland, I.; Booth, S. G.; Anthonisamy, N. N.; et al. Direct observation of dynamic lithium diffusion behavior in nickel-rich, LiNi0.8Mn0.1Co0.1O2 (NMC811) cathodes using operando muon spectroscopy. Chem. Mater. 2023, 35, 4149-58.
45. Zheng, J.; Shi, W.; Gu, M.; et al. Electrochemical kinetics and performance of layered composite cathode material Li[Li0.2Ni0.2Mn0.6]O2. J. Electrochem. Soc. 2013, 160, A2212.
46. Chen, M.; Jiang, S.; Huang, C.; et al. Synergetic effects of multifunctional composites with more efficient polysulfide immobilization and ultrahigh sulfur content in lithium-sulfur batteries. ACS. Appl. Mater. Interfaces. 2018, 10, 13562-72.
47. Assat, G.; Foix, D.; Delacourt, C.; Iadecola, A.; Dedryvère, R.; Tarascon, J. M. Fundamental interplay between anionic/cationic redox governing the kinetics and thermodynamics of lithium-rich cathodes. Nat. Commun. 2017, 8, 2219.
48. Bag, S.; Zhou, C.; Kim, P. J.; Pol, V. G.; Thangadurai, V. LiF modified stable flexible PVDF-garnet hybrid electrolyte for high performance all-solid-state Li-S batteries. Energy. Storage. Mater. 2020, 24, 198-207.
49. Khosla, N.; Narayan, J.; Narayan, R.; Sun, X.; Paranthaman, M. P. Nanosecond laser annealing of NMC 811 cathodes for enhanced performance. J. Electrochem. Soc. 2023, 170, 030520.
50. Xu, J. Critical review on cathode-electrolyte interphase toward high-voltage cathodes for Li-ion batteries. Nano-Micro. Lett. 2022, 14, 166.
51. Han, J. Y.; Jung, S. Thermal stability and the effect of water on hydrogen fluoride generation in lithium-ion battery electrolytes containing LiPF6. Batteries 2022, 8, 61.
52. Son, S.; Zhang, Z.; Gim, J.; et al. Transition metal dissolution in lithium-ion cells: a piece of the puzzle. J. Phys. Chem. C. 2023, 127, 1767-75.
53. Zhang, W.; Sun, Y.; Deng, H.; et al. Dielectric polarization in inverse spinel-structured Mg2TiO4 coating to suppress oxygen evolution of Li-rich cathode materials. Adv. Mater. 2020, 32, 2000496.
54. Jung, R.; Linsenmann, F.; Thomas, R.; et al. Nickel, manganese, and cobalt dissolution from Ni-rich NMC and their effects on NMC622-graphite cells. J. Electrochem. Soc. 2019, 166, A378.
55. Björklund, E.; Brandell, D.; Hahlin, M.; Edström, K.; Younesi, R. How the negative electrode influences interfacial and electrochemical properties of LiNi1/3Co1/3Mn1/3O2 cathodes in Li-ion batteries. J. Electrochem. Soc. 2017, 164, A3054.
56. Gao, L.; Jin, X.; Li, Z.; Li, F.; Xu, B.; Wang, C. Ultrathin titanium dioxide coating enables high-rate and long-life lithium cobalt oxide. Materials 2024, 17, 3036.
57. Holsclaw, C. M.; Sogi, K. M.; Gilmore, S. A.; et al. Structural characterization of a novel sulfated menaquinone produced by stf3 from mycobacterium tuberculosis. ACS. Chem. Biol. 2008, 3, 619-24.
58. Lin, Q.; Guan, W.; Meng, J.; et al. A new insight into continuous performance decay mechanism of Ni-rich layered oxide cathode for high energy lithium ion batteries. Nano. Energy. 2018, 54, 313-21.
59. Hua, W.; Chen, M.; Schwarz, B.; et al. Lithium/oxygen incorporation and microstructural evolution during synthesis of Li-rich layered Li[Li0.2Ni0.2Mn0.6]O2 oxides. Adv. Energy. Mater. 2019, 9, 1803094.
60. Choi, W.; Shin, H.; Kim, J. M.; Choi, J.; Yoon, W. Modeling and applications of electrochemical impedance spectroscopy (EIS) for lithium-ion batteries. J. Electrochem. Sci. Technol. 2020, 11, 1-13.
Cite This Article

How to Cite
Download Citation
Export Citation File:
Type of Import
Tips on Downloading Citation
Citation Manager File Format
Type of Import
Direct Import: When the Direct Import option is selected (the default state), a dialogue box will give you the option to Save or Open the downloaded citation data. Choosing Open will either launch your citation manager or give you a choice of applications with which to use the metadata. The Save option saves the file locally for later use.
Indirect Import: When the Indirect Import option is selected, the metadata is displayed and may be copied and pasted as needed.
About This Article
Copyright
Data & Comments
Data
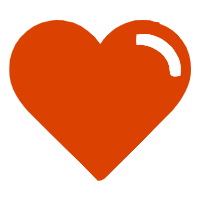
Comments
Comments must be written in English. Spam, offensive content, impersonation, and private information will not be permitted. If any comment is reported and identified as inappropriate content by OAE staff, the comment will be removed without notice. If you have any queries or need any help, please contact us at [email protected].