A quantitative reconstruction strategy for the surface structure of LiNi0.80Co0.15Al0.05O2 cathode material
Abstract
To address the detrimental impact of residual LiOH on the electrochemical performance of LiNi0.80Co0.15Al0.05O2 (NCA) cathode material, it is imperative to optimize its surface structure. Adding a Li-reactant to react with residual LiOH on the cathode surface not only removes residual LiOH but also forms new surface structure layers. However, this reaction process not only necessitates evaluating the compatibility between the newly formed surface layer and the crystal structure of the NCA cathode material but also requires careful determination of the optimal amount of Li-reactant. Currently, there remains a lack of well-established theoretical guidance for determining the optimal addition amount of lithium reactants. In this study, the quantitative addition of 6,000 ppm Al2O3 as a Li-reactant to react with the residual 3,156 ppm LiOH on the NCA surface not only effectively reduces the residual LiOH but also facilitates the formation of a LiAlO2@NCA heterostructure on the NCA cathode materials. This approach provides a theoretical foundation for the addition of Li-reactant, overcomes the limitations of empirical trial-and-error methods, and achieves quantitative reconstruction of the NCA cathode materials surface structure. Based on an in-depth analysis of the surface structure, first-principles calculations and electrochemical performance tests, the LiAlO2@NCA heterostructure not only serves as an efficient Li+ diffusion channel and reduces the Li+ migration energy barrier, but also provides a stable protection of the surface of the cathode material, thereby enhancing its stability and reversibility.
Keywords
INTRODUCTION
To achieve the goal of carbon neutrality by 2050, reducing carbon emissions necessitates a coordinated effort. Expanding the market share of electric vehicles is one of the most effective measures[1]. However, electric vehicles still face several challenges, including driving range, safety, and cost. These issues primarily stem from the power source and key components of electric vehicles - lithium-ion batteries[2]. Among these components, the cathode and anode materials are crucial to lithium-ion batteries, as they directly influence the capacity and stability of the lithium-ion batteries. A wide range of novel anode materials has emerged, exhibiting not only high capacity but also exceptional cycle stability[3-6]. The cathode material has emerged as the primary factor limiting the performance of lithium-ion batteries. Currently, numerous researchers are focused on developing cathode materials that possess high energy density, extended cycle life, and reduced cost[7-9]. NCA cathode materials have garnered significant attention from researchers and battery manufacturers owing to their superior electrochemical properties[10]. However, the application of NCA cathode materials continues to face challenges, including rapid capacity decay, structural instability, and safety concerns.
Residual lithium compounds are the main culprits for the rapid capacity decay, structural instability and low safety performance of NCA cathode materials[11]. During air exposure, the alkaline NCA cathode surface and residual lithium (Li2O) form compounds such as LiOH and Li2CO3, as given in[12-14]
During the slurry preparation of cathode materials, lithium-ion deintercalation, and practical application, residual LiOH may pose substantial safety risks[15-17]. During the preparation of electrode materials, residual LiOH can act as an inducer for slurry gelation and flocculation, which hinders the preparation of electrodes[18,19]. During charge-discharge cycles, residual LiOH forms an insulating layer that hinders Li+ migration and reduces the capacity of the cathode material[20,21]. Residual LiOH reacts with the electrolyte to release CO2 gas, leading to battery expansion and localized overheating, which significantly reduces the safety performance of the battery[22-24].
To reduce the amount of residual LiOH, researchers are investigating various surface optimization strategies to improve the surface structure and enhance the surface stability of the cathode material. These strategies include washing[25], slurry additives[26], surface coating[27], etc. The addition of a surface coating layer is a simple and effective method to reconstruct the surface structure of the cathode material, mitigate the adverse effects caused by residual LiOH on the surface, and enhance the surface stability of the cathode material. Common coating layers include oxides[28], phosphates[29], conductive polymers[30], and other ionic conductors[31]. Among various coatings, Al2O3 has become the most representative surface coating material due to its high chemical stability, readily available raw materials and excellent economic performance[32].
Adding a Li-reactant to react with residual lithium compounds on the cathode surface not only removes these compounds but also forms new surface structure layers, such as Li3PO4[29], LiF[33], and Li3BO3[34]. In previous studies, Al2O3 has predominantly been employed as a coating material. The research by
In this study, Al2O3 is selected as the Li-reactant, and the residual LiOH content is determined to be
EXPERIMENTAL SECTION
Materials synthesis
The Ni0.80Co0.15Al0.05(OH)2 precursor powder synthesized via the co-precipitation method was combined with an excess of LiOH·H2O (molar ratio of nLi/nTM = 1.05:1.00) and manually ground for half an hour. Subsequently, the mixture was transferred to a tube furnace and heated under an oxygen atmosphere. First, it was heated from ambient temperature to 450 °C at a rate of 5 °C min-1 and maintained at this temperature for 5 h. Then, the temperature was further increased to 750 °C at the same heating rate and held for 12 h. Finally, the sample was cooled down to room temperature to produce the LiNi0.80Co0.15Al0.05O2 cathode material, which was designated as NCA.
Based on the weight ratio of Al2O3/NCA = 6,000 ppm, Al2O3 powder was incorporated into the NCA cathode material and thoroughly mixed by grinding for 30 min. Subsequently, the mixture was subjected to heat treatment in an oxygen environment, where it was ramped to 500 °C at a rate of 5 °C min-1, maintained at this temperature for 6 h, and finally cooled down to ambient temperature. The resulting material was labeled as NCA-6000. The resultant process is illustrated in Figure 1A.
Material characterization
In this study, the crystal structure of the samples was characterized using RIGAKU TTRIII-18KW X-ray diffraction (XRD). The microstructure of secondary particles and the distribution of Ni, Co, and Al elements in NCA and NCA-6000 samples were examined by Nova-Nano450 field emission scanning electron microscopy (SEM) combined with energy dispersive spectroscopy (EDS). The lattice fringes of NCA-6000 samples were further analyzed using Talos F200S high-resolution transmission electron microscopy (HR-TEM) from FEI Company, USA. The valence states of Ni, Al, C, and O elements in NCA and NCA-6000 samples were investigated via PHI5000 X-ray photoelectron spectroscopy (XPS). Additionally, the detailed methodology for determining residual lithium content in NCA and NCA-6000 samples is provided in the Supplementary Materials.
Electrochemical measurements
The cathode material, carbon black, and polyvinylidene fluoride (PVDF) were accurately weighed and uniformly mixed at a mass ratio of 8:1:1. Subsequently, N-methyl-2-pyrrolidone (NMP) was added dropwise to the mixture, which was then thoroughly stirred to form a homogeneous slurry. The slurry was coated onto aluminum foil using a small-scale coater, followed by vacuum drying, rolling, and cutting to produce the cathode sheet with a loading of 7.06~8.16 mg∙cm-2 of cathode material. Finally, in an argon-filled glove box, the dried cathode sheet, lithium sheet (as the counter electrode), and separator were assembled into CR2025-type coin cells. The electrolyte used in assembling the battery is 1 M LiPF6 in EC/DMC/EMC (with a volume ratio of 1:1:1). The assembled batteries were evaluated for their initial charge-discharge performance, rate capability, and cycling stability using the LAND-BT2022A battery testing system. Additionally, cyclic voltammetry (CV) measurements at various scan rates and electrochemical impedance spectroscopy (EIS) analyses of batteries in different states (frequency range: 0.01 Hz to 100 kHz) were performed using the PMC-2000A electrochemical workstation.
Computational details
In this study, CASTEP software package was used to optimize LiAlO2, NCA and LiAlO2@NCA respectively. The electron correlation potential is described using the generalized gradient approximation-Perdew-Burke-Ernzerhof (GGA-PBE). The calculations were performed using ultra-soft pseudopotentials, with the following valence electron configurations selected for each element: O: 2s22p4, Li: 2s1, Ni: 3d84s2, Co: 3d74s2, Al: 3s23p1. In the LiAlO2 and NCA models, the k-point mesh in the Brillouin zone was set to 2 × 2 × 1, and the Brillouin zone integration was performed using the Monkhorst-Pack scheme. Among these parameters, the plane-wave cutoff energy is set to 381.0 eV, the self-consistent convergence accuracy is
RESULTS AND DISCUSSION
The surface concentrations of residual LiOH and Li2CO3 in the prepared NCA cathode material are measured using potentiometric titration, yielding values of 3,156 and 6,290 ppm, respectively. These results are summarized in Supplementary Table 1. In conjunction with previous studies[40], Al2O3 and LiOH can react within a specific temperature range. The reaction for Al2O3 and LiOH is presented in (500 °C,
based on which, the product of the reaction between Al2O3 and LiOH is LiAlO2.
Therefore, the residual LiOH can be converted into LiAlO2 through the quantitative addition of Al2O3. Temperature plays a crucial role in the formation of the LiAlO2 structural layer. If the temperature is too low, it will be insufficient to facilitate the reaction between the added Al2O3 and residual LiOH. Conversely, excessively high temperatures will increase production costs. The ΔG values for reaction Equation (3) at various temperatures are detailed in Supplementary Table 2. To verify the feasibility of this quantitative conversion strategy, Al2O3 and LiOH are mixed according to the stoichiometric ratio in Equation (3). The resulting mixture is placed in a tube furnace and heated from room temperature to 500 °C at a heating rate of 5 °C min-1 under an oxygen atmosphere for 5 h. As illustrated in Figure 1B, the primary product of the calcination reaction between Al2O3 and LiOH is LiAlO2. The XRD pattern for the added Al2O3 can be found in Supplementary Figure 1. It is evident that quantitatively adding Al2O3 to transform the residual LiOH of the cathode material into a layered LiAlO2 surface structure layer is feasible. This approach enables the quantitative reconstruction of the cathode material's surface structure.
According to the measured values of surface residual LiOH and reaction Equation (3), the NCA-6000 sample was prepared by incorporating 6,000 ppm Al2O3 to react with the 3,156 ppm residual LiOH present on the surface of the NCA cathode material (Taking precision into account, 3,156 ppm LiOH is approximated to 3,000 ppm. Based on the stoichiometric requirements of reaction (3), an addition of
In Figure 1C, the XRD patterns of the NCA and NCA-6000 samples are presented. Both samples display a highly ordered hexagonal layered α-NaFeO2 structure belonging to the space group R
The SEM images of the NCA and NCA-6000 samples are shown in Figure 2A-D. It is evident that the secondary particle morphology of both samples shows no remarkable differences, and both consist of nanoscale primary particles with an average size of around 10 nm. However, in the EDS mapping of the NCA-6000 sample [Figure 2E-H], besides the homogeneous distribution of Ni, Co, and Al elements, a slight surface enrichment of Al is also detected. This observation could be associated with the formation of a LiAlO2 structural layer, which arises from the reaction between LiOH and Al2O3 on the surface of the cathode material. The surface structure of NCA-6000 samples is further analyzed by TEM. As illustrated in Figure 2I and J and Supplementary Figure 2, the surface structure of the NCA-6000 sample displays a pronounced heterogeneous morphology. Additionally, the development and distribution of the LiAlO2 structural layer are strongly linked to the existence of residual LiOH. Region I displays lattice fringes with a d-spacing of 0.4784 nm, which matches the (003) plane of NCA[42]. In contrast, region II shows distinct lattice fringes that differ from those of NCA, with a spacing of 0.2047 nm corresponding to the (104) plane of LiAlO2 (PDF#44-0224)[43]. Through XRD, SEM, and TEM analyses, it is observed that the added Al2O3 reacts with residual LiOH to form a heterostructure layer of LiAlO2@NCA on the surface of the cathode material, enabling quantitative reconstruction of the surface structure of the cathode material.
Figure 2. SEM images of NCA and NCA-6000 (A and B) NCA; (C and D) NCA-6000; (E-H) SEM and EDS surface scanning element distribution map of NCA-6000 elements of Ni, Co and Al; (I and J) TEM image of the NCA-6000.
To investigate the impact of the LiAlO2@NCA heterostructural layer on the structural integrity, stability, and electrochemical performance of the cathode material, the surface structures of LiAlO2, NCA and NCA-6000 are modeled and analyzed, as illustrated in Figure 3. Using the NCA as a matrix, a LiAlO2@NCA heterostructure is formed on its surface. As shown in Figure 3A and B, the band structures of both LiAlO2 (Eg = 5.94 eV) and NCA (Eg = 3.11 eV) reveal wide-bandgap semiconductor characteristics. However, the band structure of the LiAlO2@NCA heterostructures reveals characteristics typical of conductors [Figure 3C]. The electron energy levels of the LiAlO2@NCA heterostructure exhibit unique electrochemical properties and provide excellent electron conductivity. In practical applications, the LiAlO2@NCA heterostructure can effectively enhance current efficiency, reduce the ion migration energy barrier, significantly improve electron polarization during charge/discharge cycles, and boost the rate performance of cathode materials.
Figure 3. Energy band and structure (A) LiAlO2; (B) NCA; (C) LiAlO2@NCA; State density diagram (D) LiAlO2; (E) NCA; (F)
To uncover the underlying reasons, the charge density distributions of the two substrates (LiAlO2 and NCA) and atoms are further analyzed. As illustrated in Figure 3D, the valence band top of LiAlO2 is primarily dominated by O-2p orbitals, with a minor contribution from weakly localized Al-3p orbitals. The weak localization of Al-3p allows it to form stable hybrid states with O-2p, effectively suppressing lattice oxygen release. While Al3+ does not participate in redox reactions, it stabilizes the oxygen framework, thereby reducing interfacial side reactions. As shown in Figure 3E, the valence band top of NCA is predominantly composed of Ni-3d orbitals, with contributions from Co-3d and O-2p orbitals. The strong localization of the Ni-3d orbitals indicates that their electron cloud distribution is highly concentrated near the atomic nucleus. This localization necessitates overcoming a higher electronic transition energy barrier during the Ni2+/N3+ oxidation process, significantly reducing the redox reaction rate. Additionally, the localized Ni-3d orbitals enhance the covalency of the Ni-O bond, thereby restricting lithium-ion migration within the layered structure. Although the Co-3d orbitals also exhibit strong charge localization, their significant energy level splitting facilitates electronic transitions in the Co3+/Co4+ redox reaction, partially offsetting the negative effects of localization. Moreover, the hybridization between Co-3d and O-2p orbitals forms delocalized states, accelerating the charge transfer process.
The LiAlO2@NCA heterostructure achieves gradient localized electronic states through orbital hybridization at the interface (Ni-3d/O-2p and Al-3p/O-2p). These interface states bridge the strongly localized Ni-3d and delocalized O-2p orbitals, lowering the charge transfer barrier. Through this interface state regulation, the LiAlO2@NCA heterostructure balances localized and delocalized characteristics, reduces the charge transfer energy barrier, optimizes overall redox kinetics, and achieves a synergistic enhancement in both kinetics and stability.
As shown in Figure 3F, the density of states (DOS) distribution of the LiAlO2@NCA heterostructure is a result of this regulation. The valence bands are primarily formed by the hybridization of Ni-3d, Co-3d, and O-2p orbitals, while the conduction bands are contributed to by the hybridization of O-2p and Al-3p orbitals. Each band exhibits a high degree of localization. The energy loss function also illustrates this point from another perspective. As shown in Supplementary Figure 3, the degree of energy loss caused by charge movement in the LiAlO2@NCA heterostructure is significantly reduced. The formation of the LiAlO2@NCA heterostructure improves the band structure of the original system, introduces interface state characteristics, and enhances electron conductivity.
XPS is further employed to analyze the surface composition of the NCA and NCA-6,000 samples, with the results presented in Figure 4, full spectrum Supplementary Figure 4, and Supplementary Table 3. By comparing the amount of Ni2+/Ni3+ in NCA and NCA-6000 [Figure 4A and B], it is found that the amount of Ni2+ increases slightly in the NCA-6000 sample. It may be that the amount of Li+ in the Li layer is slightly reduced during the heat drive process (500 °C), which is consistent with the results of titration. Compared with NCA, the Al 2p peak in NCA-6000 also exhibited a slight increase [Figure 4C and D], which can primarily be attributed to the addition of Al2O3. In the C1s spectrum [Figure 4E and F], the Li2CO3 content in NCA-6000 increased slightly compared to NCA (from 8.9% to 9.4%). This increase can be attributed to the diffusion of a small amount of Li from the interior of the cathode material to its surface during reheating at 500 °C, leading to the formation of new Li2CO3 on the surface. Figure 4G and H shows the O 1s spectrum, with peaks at 529.00 eV attributed to lattice oxygen (M-O). The peak at 530.35 eV corresponds to residual lithium compounds (R-O-Li, such as Li2CO3 and LiOH) on the surface of the cathode material[13,14,44]. Compared with NCA, the M-O content on the surface of NCA-6000 is slightly increased[45]. This increase may be related to the formation of the LiAlO2@NCA heterostructure. Figure 4G and H presents the O 1s spectrum, where the peak at 529.00 eV is assigned to lattice oxygen (M-O). The peak at 530.35 eV is associated with residual lithium compounds (R-O-Li, such as Li2CO3 and LiOH)[13,14,44]. In comparison with NCA, the M-O content on the surface of NCA-6000 shows a slight increase[45]. This enhancement could potentially be linked to the formation of the LiAlO2@NCA heterostructure. Additionally, the R-O-Li peak area in NCA-6000 decreased from 51.0% (in NCA) to 45.1%, indicating a reduction in residual lithium compounds, which can be attributed to the conversion of LiOH by the addition of Al2O3.
Figure 4. XPS spectra of NCA and NCA-6000 (A and B) Ni 2p; (C and D) Al 2p; (E and F) C 1s; (G and H) O 1 s; (I) the proportion of different components.
The study provides a comprehensive evaluation of the electrochemical performance of two cathode material samples: NCA and NCA-6000. The primary focus is on understanding the influence of the LiAlO2@NCA heterostructure, which is formed through a process of quantitative reconstruction. This heterostructure plays a critical role in altering the surface properties of the cathode materials, thereby affecting their overall electrochemical behavior. In terms of specific electrochemical performance metrics, the results reveal that the NCA-6000 sample demonstrates superior characteristics compared to the standard NCA material. For instance, the initial discharge capacity of NCA-6000 is measured at 206.0 mAh·g-1, which represents an improvement over the capacity of the NCA sample of 201.9 mAh·g-1 [Figure 5 and Supplementary Table 4]. Additionally, the initial coulombic efficiency of NCA-6000 is recorded at 89.4%, surpassing the 88.9% efficiency of the NCA sample. These enhancements suggest that the formation of the LiAlO2@NCA heterostructure effectively mitigates irreversible capacity loss during the initial electrochemical processes.
Figure 5. Comparison of electrochemical performances of the sample (A) first charging and discharging profiles; (B) charge-discharge performance at various current densities; (C) Cycling performance at 1 C; dQ/dV curves NCA (D) and Al-4000 (E).
The rate performance of the two cathode material samples, NCA and NCA-6000, is visually presented in Figure 5B and further detailed in Supplementary Figure 5A. When comparing the two samples, it becomes evident that the NCA-6000 sample demonstrates superior characteristics in terms of discharge capacity and coulombic efficiency. Across all tested rates, the NCA-6000 consistently delivers higher discharge capacities, indicating its ability to maintain a greater energy output even under high current demands. In addition to higher discharge capacities, the NCA-6000 also exhibits more stable coulombic efficiency compared to the standard NCA material. Coulombic efficiency, which measures the ratio of lithium ions extracted during discharge to those inserted during charge, is a key indicator of a battery's overall efficiency and longevity. Specifically, as the rate increased from 0.1 to 2 C, the rate capacity of NCA-6000 showed a more substantial improvement. The enhanced rate performance of the NCA-6000 sample can be attributed to the formation of the LiAlO2@NCA heterostructure. This architecture optimizes the band structure of the initial system, boosts the electronic conductivity of the cathode material, and minimizes electron polarization during charging and discharging, aligning with the computational findings. Figure 5C and
It can be seen that LiAlO2@NCA heterostructure can effectively reduce capacity fade and improve the cyclic stability of cathode materials. Moreover, compared with cathode materials optimized using existing surface modification methods, the NCA-6000 sample exhibits competitive electrochemical performance
In order to further clarify how the LiAlO2@NCA heterostructure, obtained via quantitative reconstruction, enhances the reversibility and structural stability of the cathode material, a comparison of the dQ/dV evolution for the NCA and NCA-6000 samples is presented from the 1st to the 200th cycle. This analysis is conducted within the voltage range of 2.8-4.3 V at a rate of 1 C, as illustrated in Figure 5D and E. The
The outstanding electrochemical performance of cathode materials is strongly linked to the diffusion kinetics of Li+ and the characteristics of the interfacial environment. To explore in greater detail how the reconstructed LiAlO2@NCA heterostructures influence the dynamics of Li+ migration, as well as the structural and interfacial stability of cathode materials, analyses are conducted using CV, EIS, and by examining the cross-sections of electrode plates both before and after cycling. As illustrated in Figure 6A-F, CV measurements are performed on NCA and NCA-6000 samples with sweep rates varying from 0.1 to
Figure 6. CV curves NCA (A) and NCA-6000 (B) at a sweep speed of 0.1 mV·s-1; CV curves NCA (C) and NCA-6000 (D) at different scanning rates; CV curve comparison (E and F); EIS profiles of NCM and Al-4000 in cycles 0 (G) and 200 (H); (I) The NCA pole plate profile is not tested; (J) NCA pole plate profile after 200 cycles; (K) NCA-6000 pole plate profile is not tested; (L) NCA-6000 pole plate profile after 200 cycles.
Here, n refers to the charge number associated with the ion involved in the redox process, which in this case is lithium ions (Li+), carrying a single positive charge (n = 1). The parameter A denotes the geometric surface area of the electrode, which is critical for determining the amount of active material participating in the electrochemical reactions. In this context, the electrode surface area is given as 1.33 cm². The symbol λ represents the scanning rate used in CV experiments, typically expressed in mV·s-1. Lastly, Co signifies the concentration of lithium ions (Li+) in the electrolyte solution[47]. Moreover, DLi can be calculated from Ip and the slope K of the curve. According to the fitted curve slopes, the DLi values for the charging processes of NCA and NCA-6000 are 5.89 × 10-9 and 5.18 × 10-8 cm2S-1, respectively. During the discharging processes, the corresponding the DLi values are 5.89 × 10-9 and 5.18 × 10-8 cm2S-1, respectively. In both the charging and discharging phases, the NCA-6000 sample demonstrates a significantly higher DLi. These results indicate that the LiAlO2@NCA heterostructure obtained through quantitative reconstruction enhances the Li+ diffusion kinetics of the cathode material, which is consistent with the excellent magnification performance of NCA-6000.
Excellent electrochemical properties are closely related to the interfacial environment of the material. Therefore, the EIS profiles of NCA and NCA-6000 samples before and after cycling were compared. Figure 6G and H shows the electrochemical impedance spectra of NCA and NCA-6000 samples after the 0th and 200th cycles. Figure 6G presents the equivalent circuit and impedance curve of a battery in its uncharged or discharged state. The curve shows a semicircle in the high-frequency region and a diagonal line in the low-frequency region, indicating Rct and Warburg impedance[49]. The point where the semicircle meets the real axis (Z') at high frequencies corresponds to the ohmic resistance (Rs). This value encompasses the resistance contributed by the electrolyte as well as other resistive components[50]. Figure 6H presents the electrochemical impedance of the battery after 200 cycles at 1 C rate within 2.8-4.3 V. The spectra of cycled cells reveal a high-frequency semicircle linked to the solid electrolyte interface resistance (Rsf). This is absent in Figure 6G as the SEI film does not form when uncharged[51]. After cycling, the increase in Rs is primarily attributed to the instability of the electrolyte, leading to increased electrolyte resistance. The results of the fitting are compiled in Supplementary Table 6, demonstrating that the cycled battery has a considerably higher Rct compared to the uncycled battery. Notably, the Rct of NCA-6000 samples was markedly reduced compared to NCA, owing to the enhanced conductivity and reduced interfacial side reactions of NCA-6000. This finding matches the excellent cycling performance of NCA-6000. Results show that the LiAlO2@NCA heterostructure improves cathode conductivity and reduces electrode-electrolyte side reactions through quantitative reconstruction.
The cross-sectional morphology of NCA and NCA-6000 samples before and after cycling was analyzed using SEM. As shown in Figure 6I-L, the thickness of the electrode material on the uncycled NCA and NCA-6000 samples is ~31 and ~32 μm, respectively. It can be observed that the thickness difference between the two samples is minimal when the electrodes are uncycled. SEM is used to analyze the cross-sectional morphology of NCA and NCA-6000 samples before and after cycling. As depicted in Figure 6I-L, the uncycled NCA and NCA-6000 electrode thicknesses are ~31 and ~32 μm, respectively, with minimal difference between them.
However, after 200 cycles, the electrode material on the NCA sample exhibits significant volume expansion, increasing from an initial thickness of ~31 to ~49 μm, which correlates with the low capacity and capacity retention rate observed after 200 cycles. In contrast, after 200 cycles, the electrode material on the NCA-6000 sample shows only a slight volume expansion, from an initial thickness of ~32 to ~37 μm. The reduced volume expansion of the NCA-6000 sample indicates that surface side reactions are effectively suppressed, leading to better interface stability. In conclusion, the LiAlO2@NCA heterostructure obtained through quantitative reconstruction improves electrode interface stability and offers a way to enhance the cycle stability of NCA cathode materials.
CONCLUSIONS
This quantitative reconstruction strategy, which involves adding 6,000 ppm of Al2O3 as a Li-reactant to react with the residual 3,156 ppm of LiOH on the NCA surface, not only effectively reduces the residual LiOH and forms a LiAlO2@NCA heterostructure on the NCA cathode material surface but also provides a theoretical basis for the addition of Li-reactants, thereby breaking through the limitations of empirical trial-and-error methods. The developed LiAlO2@NCA heterostructure incorporates interface state features, optimizes the band structure of the initial system, boosts electronic conductivity, decreases the energy barrier for Li+ migration, and mitigates polarization during charging and discharging. These enhancements collectively lead to improved rate capability and charge-discharge efficiency of the NCA cathode material. Compared to NCA, the NCA-6000 sample exhibits higher discharge capacities at all tested rates. Moreover, the LiAlO2@NCA heterostructure forms a stable protective coating on the NCA cathode surface, reducing unwanted reactions between the electrode and electrolyte, limiting volume changes in the electrode material, improving interfacial stability, and enhancing structural reversibility. These factors collectively improve the cycling stability of the NCA cathode material. Under 1 C conditions, the NCA-6000 sample demonstrated a capacity retention of 77.3% after 200 cycles, which is higher than the 55.3% observed for the NCA sample under identical conditions. The quantitative reconstruction strategy for the surface structure of NCA cathode materials proposed in this study offers a promising approach to developing high-energy-density cathode materials.
DECLARATIONS
Authors’ contributions
Provide research ideas, design experimental protocols and writing-original draft: Guo, X.
material preparation, characterization and Electrochemical performance test: Yang, J.; Deng, G.; Cao, X.
Provided technical and material support: Zhang, B.; Deng, T.
review and editing: Zhu, Y.; Liu, J.; Wang, W.
Editing: Xia, S.
All authors revised the manuscript.
Availability of data and materials
All detailed materials and methods supporting the results of this study are included in the article/Supplementary Materials.
Financial support and sponsorship
This work was financially supported by Yunnan Fundamental Research Project (202401AS070001), Yunnan Key Laboratory of Crystalline Porous Organic Functional Materials (202449CE340024), and the Program of Innovative Research Team (in Science and Technology) in the University of Yunnan Province.
Conflicts of interest
Zhu, Y.; Liu, J.; Wang, W. are affiliated with Guizhou Anda Technology Energy Co. Ltd., while all other authors have declared no conflicts of interest.
Ethical approval and consent to participate
Not applicable.
Consent for publication
Not applicable.
Copyright
© The Author(s) 2025.
Supplementary Materials
REFERENCES
1. Lee, S.; Park, N.; Park, G.; et al. Doping strategy in developing Ni-rich cathodes for high-performance lithium-ion batteries. ACS. Energy. Lett. 2024, 9, 740-7.
2. Yang, J.; Liang, X.; Ryu, H.; Yoon, C. S.; Sun, Y. Ni-rich layered cathodes for lithium-ion batteries: from challenges to the future. Energy. Storage. Mater. 2023, 63, 102969.
3. Xia, S.; Cai, Y.; Yao, L.; et al. Nitrogen-rich two-dimensional π-conjugated porous covalent quinazoline polymer for lithium storage. Energy. Storage. Mater. 2022, 50, 225-33.
4. Xia, S.; Liu, T.; Huang, W.; et al. Extended π-conjugated N-containing heteroaromatic hexacarboxylate organic anode for high performance rechargeable batteries. J. Energy. Chem. 2020, 51, 303-11.
5. Sagar, R. U. R.; Rahman, M. M.; Cai, Q.; Liang, T.; Chen, Y. I. A comparative study on morphology dependent performance of neodymium - graphene as an anode material in lithium-ion batteries. J. Energy. Storage. 2024, 77, 109854.
6. Rehman, S. R. U.; Nelson, A.; Fazal, M. W.; et al. An ultralight porous carbon scaffold for anode-free lithium metal batteries. J. Mater. Chem. A. 2025, 13, 5081-90.
7. Huang, W.; Sun, Y.; Zhao, G.; et al. Constructing nano spinel phase and Li+ conductive network to enhance the electrochemical stability of ultrahigh-Ni cathode. Mater. Today. 2024, 79, 86-96.
8. Deng, Z.; Liu, Y.; Wang, L.; et al. Challenges of thermal stability of high-energy layered oxide cathode materials for lithium-ion batteries: a review. Mater. Today. 2023, 69, 236-61.
9. Wu, Z.; Zhang, C.; Yuan, F.; et al. Ni-rich cathode materials for stable high-energy lithium-ion batteries. Nano. Energy. 2024, 126, 109620.
10. Ryu, H.; Park, N.; Seo, J. H.; et al. A highly stabilized Ni-rich NCA cathode for high-energy lithium-ion batteries. Mater. Today. 2020, 36, 73-82.
11. Ryu, H.; Lim, H.; Lee, S. G.; Sun, Y. Near-surface reconstruction in Ni-rich layered cathodes for high-performance lithium-ion batteries. Nat. Energy. 2024, 9, 47-56.
12. Seong, W. M.; Cho, K. H.; Park, J. W.; et al. Controlling residual lithium in high-nickel (> 90 %) lithium layered oxides for cathodes in lithium-ion batteries. Angew. Chem. Int. Ed. 2020, 59, 18662-9.
13. Sheng, H.; Meng, X. H.; Xiao, D. D.; et al. An air-stable high-nickel cathode with reinforced electrochemical performance enabled by convertible amorphous Li2CO3 modification. Adv. Mater. 2022, 34, e2108947.
14. Song, M.; Lee, D.; Kim, J.; et al. Chemical decomposition pathway of residual lithium carbonate of Li-ion battery cathodes. J. Power. Sources. 2023, 560, 232699.
15. Du, Y.; Sheng, H.; Meng, X.; et al. Chemically converting residual lithium to a composite coating layer to enhance the rate capability and stability of single-crystalline Ni-rich cathodes. Nano. Energy. 2022, 94, 106901.
16. Cao, D.; Tan, C.; Chen, Y. Oxidative decomposition mechanisms of lithium carbonate on carbon substrates in lithium battery chemistries. Nat. Commun. 2022, 13, 4908.
17. Cui, Z.; Manthiram, A. Thermal stability and outgassing behaviors of high-nickel cathodes in lithium-ion batteries. Angew. Chem. Int. Ed. 2023, 62, e202307243.
18. Seong, W. M.; Kim, Y.; Manthiram, A. Impact of residual lithium on the adoption of high-nickel layered oxide cathodes for lithium-ion batteries. Chem. Mater. 2020, 32, 9479-89.
19. Freiberg, A. T.; Sicklinger, J.; Solchenbach, S.; Gasteiger, H. A. Li2CO3 decomposition in Li-ion batteries induced by the electrochemical oxidation of the electrolyte and of electrolyte impurities. Electrochim. Acta. 2020, 346, 136271.
20. Cui, Z.; Zuo, P.; Guo, Z.; Wang, C.; Manthiram, A. Formation and detriments of residual alkaline compounds on high-nickel layered oxide cathodes. Adv. Mater. 2024, 36, e2402420.
21. Wang, C.; Shao, L.; Guo, X.; et al. Air-induced degradation and electrochemical regeneration for the performance of layered Ni-rich cathodes. ACS. Appl. Mater. Interfaces. 2019, 11, 44036-45.
22. Aktekin, B.; Sedykh, A. E.; Müller-Buschbaum, K.; Henss, A.; Janek, J. The formation of residual lithium compounds on Ni-rich NCM oxides: their impact on the electrochemical performance of sulfide-based ASSBs. Adv. Funct. Mater. 2024, 34, 2313252.
23. Renfrew, S. E.; McCloskey, B. D. Residual lithium carbonate predominantly accounts for first cycle CO2 and CO outgassing of Li-stoichiometric and Li-rich layered transition-metal oxides. J. Am. Chem. Soc. 2017, 139, 17853-60.
24. Xia, Y.; Chen, A.; Wang, K.; et al. Industrial modification comparison of Ni-Rich cathode materials towards enhanced surface chemical stability against ambient air for advanced lithium-ion batteries. Chem. Eng. J. 2022, 450, 138382.
25. Gao, Y.; Jiang, R.; Dai, Z.; et al. Revealing the relationships between washing/recalcination processes and structure performance of Ni-rich layered cathode materials. ACS. Appl. Energy. Mater. 2022, 5, 15069-77.
26. Zhang, S. S.; Fan, X.; Wang, C. Enhanced electrochemical performance of Ni-rich layered cathode materials by using LiPF6 as a cathode additive. ChemElectroChem 2019, 6, 1536-41.
27. Kim, J.; Zhang, X.; Zhang, J.; Manthiram, A.; Meng, Y. S.; Xu, W. A review on the stability and surface modification of layered transition-metal oxide cathodes. Mater. Today. 2021, 46, 155-82.
28. Wen, Z.; Song, Y.; Shi, H.; et al. Improved electrochemical performance of single-crystal nickel-rich cathode by coating with different valence states metal oxides. J. Energy. Storage. 2024, 98, 113037.
29. Wei, J.; Xiong, H.; Zhang, H.; Li, X.; Liu, Y.; Shi, Z. Enhancement in the electrochemical stability at high voltage of high nickel cathode through constructing ultrathin LiCoPO4 coating. Appl. Surf. Sci. 2024, 659, 159922.
30. Yang, H.; Gao, R. M.; Zhang, X. D.; et al. Building a self-adaptive protective layer on Ni-rich layered cathodes to enhance the cycle stability of lithium-ion batteries. Adv. Mater. 2022, 34, e2204835.
31. Kim, S.; Kim, M.; Ku, M.; Park, J.; Lee, J.; Kim, Y. B. Coating robust layers on Ni-rich cathode active materials while suppressing cation mixing for all-solid-state lithium-ion batteries. ACS. Nano. 2024, 18, 25096-106.
32. Wu, F.; Shi, Q.; Chen, L.; et al. New insights into dry-coating-processed surface engineering enabling structurally and thermally stable high-performance Ni-rich cathode materials for lithium ion batteries. Chem. Eng. J. 2023, 470, 144045.
33. Chu, Y.; Mu, Y.; Zou, L.; et al. Thermodynamically stable dual-modified LiF&FeF3 layer empowering Ni-rich cathodes with superior cyclabilities. Adv. Mater. 2023, 35, e2212308.
34. Xia, S.; Huang, W.; Shen, X.; et al. Rearrangement on surface structures by boride to enhanced cycle stability for LiNi0.80Co0.15Al0.05O2 cathode in lithium ion batteries. J. Energy. Chem. 2020, 45, 110-8.
35. Negi, R. S.; Yusim, Y.; Pan, R.; et al. A dry-processed Al2O3/LiAlO2 coating for stabilizing the cathode/electrolyte interface in high-Ni NCM-based all-solid-state batteries. Adv. Mater. Inter. 2022, 9, 2101428.
36. Park, H. G.; Min, K.; Park, K. A synergistic effect of Na+ and Al3+ dual doping on electrochemical performance and structural stability of LiNi0.88Co0.08Mn0.04O2 cathodes for Li-ion batteries. ACS. Appl. Mater. Interfaces. 2022, 14, 5168-76.
37. Yang, Z.; Hu, Q.; Yang, H.; et al. Promoting air stability of Co-Li2O cathode additive via LiAlO2 coating for lithium-ion batteries. J. Electroanal. Chem. 2025, 983, 119042.
38. Liang, C.; Cheng, Y.; Lv, C.; et al. Surface oxygen-locked LiNi0.6Mn0.4O2: towards stable cycling at 4.7 V. Energy. Storage. Mater. 2025, 75, 104087.
39. Sun, Y.; Liu, Z.; Chen, X.; Yang, X.; Xiang, F.; Lu, W. Enhancing the stabilities and electrochemical performances of
40. Guo, X.; Li, S.; Dai, S.; Wu, S.; Liu, D.; Yang, G. The intricate roles of Al2O3 on the structure and electrochemical performances of LiNi0.5Co0.2Mn0.3O2 cathodematerials. J. Alloys. Compd. 2024, 984, 173931.
41. Lv, Y.; Huang, S.; Zhang, J.; et al. Antimony doping enabled radially aligned microstructurein LiNi0.91Co0.06Al0.03O2 cathode for high-voltage and low-temperature lithium battery. Adv. Funct. Mater. 2024, 34, 2312284.
42. Zhou, Y.; Zhang, H.; Wang, Y.; et al. Relieving stress concentration through anion-cation codoping toward highly stable nickel-rich cathode. ACS. Nano. 2023, 17, 20621-33.
43. Li, L.; Chen, Z.; Zhang, Q.; et al. A hydrolysis-hydrothermal route for the synthesis of ultrathin LiAlO2-inlaid LiNi0.5Co0.2Mn0.3O2 as a high-performance cathode material for lithium ion batteries. J. Mater. Chem. A. 2015, 3, 894-904.
44. Bichon, M.; Sotta, D.; Dupré, N.; et al. Study of immersion of LiNi0.5Mn0.3Co0.2O2 material in water for aqueous processing of positive electrode for Li-ion batteries. ACS. Appl. Mater. Interfaces. 2019, 11, 18331-41.
45. Wood, K. N.; Teeter, G. XPS on Li-battery-related compounds: analysis of inorganic SEI phases and a methodology for charge correction. ACS. Appl. Energy. Mater. 2018, 1, 4493-504.
46. Wu, F.; Dong, J.; Chen, L.; et al. High-voltage and high-safety nickel-rich layered cathode enabled by a self-reconstructive cathode/electrolyte interphase layer. Energy. Storage. Mater. 2021, 41, 495-504.
47. Wu, F.; Kim, G.; Kuenzel, M.; et al. Elucidating the effect of iron doping on the electrochemical performance of cobalt-free lithium-rich layered cathode materials. Adv. Energy. Mater. 2019, 9, 1902445.
48. Chen, Z.; Kim, G.; Bresser, D.; et al. MnPO4-coated Li(Ni0.4Co0.2Mn0.4)O2 for Lithium(-ion) batteries with outstanding cycling stability and enhanced lithiation kinetics. Adv. Energy. Mater. 2018, 8, 1801573.
49. Jung, C.; Kim, D.; Eum, D.; et al. New insight into microstructure engineering of Ni-rich layered oxide cathode for high performance lithium ion batteries. Adv. Funct. Mater. 2021, 31, 2010095.
50. Sun, Y.; Wang, C.; Huang, W.; et al. One-step calcination synthesis of bulk-doped surface-modified Ni-rich cathodes with superlattice for long-cycling Li-ion batteries. Angew. Chem. Int. Ed. 2023, 62, e202300962.
Cite This Article

How to Cite
Download Citation
Export Citation File:
Type of Import
Tips on Downloading Citation
Citation Manager File Format
Type of Import
Direct Import: When the Direct Import option is selected (the default state), a dialogue box will give you the option to Save or Open the downloaded citation data. Choosing Open will either launch your citation manager or give you a choice of applications with which to use the metadata. The Save option saves the file locally for later use.
Indirect Import: When the Indirect Import option is selected, the metadata is displayed and may be copied and pasted as needed.
About This Article
Copyright
Data & Comments
Data
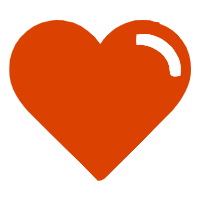
Comments
Comments must be written in English. Spam, offensive content, impersonation, and private information will not be permitted. If any comment is reported and identified as inappropriate content by OAE staff, the comment will be removed without notice. If you have any queries or need any help, please contact us at [email protected].