Performance-based seismic design method for pile-supported wharves with seismic isolation system
Abstract
As the global coastal seismic zone is increasingly active, the pile-supported wharves experience various levels of damage, which may stop the port operations. The Wharves with Seismic Isolation System (SISW), in which the isolation devices are placed on the top of the piles, was proposed to release the constraint of the top of piles and to mitigate damages between the top of piles and the wharf deck. However, current research on SISW was case by case, and a consistent general design method is lacking. This paper presents the Performance-Based Seismic Design (PBSD) method for SISW. Here, multiple design levels and the corresponding performance objectives are proposed. An example project is introduced to explain the proposed PBSD method and verify the designed performance. The nonlinear time history analysis results demonstrate that the proposed design method effectively achieves the multi-level seismic objectives for SISW. Moreover, implementing SISW with the PBSD method achieves higher seismic performance objectives than Non-Seismic-Isolated Wharves, which utilize the same type of piles. The seismic resilience of wharves in high-intensity seismic regions can be significantly enhanced using the SISW and corresponding design method.
Keywords
INTRODUCTION
Pile-supported wharves, consisting primarily of decks and piles, are a fundamental structural system in port engineering. They possess advantageous characteristics, such as low sand and gravel consumption, minimal dredging volume, low wave reflection, and favorable mooring conditions. As pivotal maritime transportation hubs, the construction and operation of pile-supported wharves play a crucial role in fostering domestic and global trade growth. However, the escalating seismic activity worldwide has led to varying degrees of damage to wharf pile foundations in previous earthquakes[1-8], as exemplified in Figure 1 for selected cases.
A pile-supported wharf can be approximately treated as a single-degree-of-freedom system, where the structural mass is primarily concentrated in the deck, which generates seismic forces. At the same time, the piles provide lateral structural stiffness. Current seismic design codes[2,9-11] typically focus on controlling the horizontal displacement response of the wharf by designing the pile stiffness and relying on pile ductility to withstand intense earthquakes. Nevertheless, such design philosophy tends to underestimate the significance of "short pile failure" [Figure 1B] or "batter pile failure" [Figure 1C] resulting from the stiffness concentration effect of inboard piles or batter piles. Consequently, this leads to a notable reduction in the seismic performance of pile-supported wharf structures[12,13]. Moreover, overreliance on the ductile deformation of piles can induce excessive wharf deformation, leading to structural damage and operational disruption[1].
To mitigate ductile damage and the stiffness concentration effect in pile foundations, the implementation of Wharves with the Seismic Isolation System (SISW) [Figure 2] was proposed[7,14-19]. Specifically, isolation devices are arranged at the top of the piles (pile head or pile cap) to decouple the deformation between the deck and the piles, thereby reducing the seismic demands on plumb or batter piles during earthquakes.
Mito et al. introduced the concept of placing high-damping rubber bearings at the top of wharf piles
To mitigate stiffness concentration in batter piles, researchers[7,18] and standards[11] have proposed the placement of isolation devices at the top or cap of batter piles [Figure 2B]. Brunet et al. introduced the South Coronel Pier, which remained intact after the 2010 Chile earthquake, utilizing laminated lead core bearings[7]. Fendy et al. implemented isolators for a marginal wharf with batter piles[18]. The isolation scheme increased the natural period of the wharf, reducing the seismic demand by avoiding the dominant frequencies of earthquake waves. In addition to retrofitting existing wharves with isolators, researchers have also introduced isolated batter piles from a strengthening perspective to enhance the stiffness and energy dissipation capacity of wharves[15,17].
By adopting the wharves with the SISW, it is possible to control the damage mode of the wharf effectively, reducing pile damage and avoiding stiffness concentration. However, research on SISW has thus far been limited to case studies, and a systematic performance-based seismic design (PBSD) method for SISW has yet to be proposed. Therefore, this study proposes seismic objectives for SISW based on ASCE 61-14[11] and presents a two-stage PBSD method for SISW. Specifically, the layout and design parameters of the isolation devices are determined based on the Contingency Level Earthquake (CLE) (10% probability of exceedance in 50 years), while the wharf displacement response is examined based on the Maximum Considered Earthquake (MCE) level (2% probability of exceedance in 50 years). Finally, the effectiveness of the proposed design method for SISW is demonstrated and validated through a plump-pile wharf design case.
Seismic performance objectives for wharf with seismic isolation system
The ASCE code "Seismic Design of Piers and Wharves (ASCE 61-14)"[11] establishes the minimum seismic hazard and performance requirements, specifying the performance levels of wharves according to different design classifications and seismic levels. In line with ASCE 61-14, this study presents the design objectives for SISW, as outlined in Table 1, with two key differences compared to ASCE 61-14:
Design objectives for SISW
Seismic level | Operating level earthquake (OLE) | Contingency level earthquake (CLE) | Maximum considered earthquake (MCE) | |
Ground motion probability of exceedance | 50%/50 years | 10%/50 years | 2%/50 years | |
Design classification | H2 | Minimal damage | Minimal damage | Minimal damage |
H1 | Minimal damage | Minimal damage | Controlled and repairable damage | |
H0* | Minimal damage | Controlled and repairable damage | Life safety protection |
The "Design Earthquake (DE)" level in ASCE 61-14 is upgraded to the "MCE" level to enhance the seismic performance of wharves during rare earthquakes.
Two additional design classifications, namely "H1" and "H2", are introduced to achieve high-performance design for SISW.
The definitions and quantification criteria for different performance levels of the pile foundation are referenced from Section 3.9 "STRAIN LIMITS" in ASCE 61-14[11]. These performance levels are categorized based on the strain limits along pile plastic hinges. For example, the concrete strain limits for reinforced concrete (RC) pile plastic hinges allowed at the pile top and in the ground are 0.005 within the performance level of "minimal damage" and 0.025 and 0.008, respectively, within "controlled and repairable damage".
In the seismic design of wharves, it is necessary to convert material strains into structural displacements as design demands under different seismic levels. The pushover analysis could be conducted to obtain the displacement demands.
Performance-based seismic design for wharf with seismic isolation system
The plump-pile wharf is adopted as the example to introduce the PBSD method for SISW. Firstly, the design principles based on uniform pile stiffness are introduced. Secondly, a two-stage PBSD method for SISW is proposed.
Design principles
For pile-supported wharves with sloping embankments [see Figure 2], seismic isolation aims to control the damage mode of the wharves and prevent stiffness concentration-induced damage in inboard piles. Therefore, the isolators should be arranged to ensure balanced lateral stiffness of each pile in the transverse row, thereby distributing the seismic demands evenly among all piles. This principle is referred to as the "uniform pile stiffness principle" in this study. The arrangement of isolators should start from the inboard pile, and the number and capacity of isolators should be calculated based on the seismic demands and the process of uniform pile stiffness principle (the details will be presented in Section "Application of the PBSD method for wharf with seismic isolation system").
When using isolation devices, the lateral stiffness of the pile foundation (referred to as "isolated piles" hereafter) decreases significantly due to the hinged connection at the pile top. This increased seismic deformation in piles reduces the displacement of the isolation devices, which is detrimental to their performance.
To increase the stiffness and integrity of the isolated piles, rigid connecting beams between the pile tops can be installed to limit pile top rotation [see Figure 3]. When stiffness of piles is enhanced, the seismic deformation of the wharf can be concentrated in isolators.
Connecting beams are designed as capacity-protected elements to ensure their elasticity under the MCE levels. Specifically, when the SISW reaches design displacement, the demands for the moment and shear force at coupling beam ends can be calculated by structural mechanics. By multiplying by an over-strength factor (taken as 1.3 in this work), section steel with sufficient capacity can be selected as the main body. Moreover, the connection strength between the connecting beams and the piles needs to be verified through welding or bolted connections.
The design of isolation devices should meet the following conditions:
(1) Isolation devices should possess sufficient initial stiffness to mitigate detrimental vibrations of the wharf caused by wind loads, foundation micro-vibrations, or ship berthing forces. The isolation devices should maintain optimal vertical load resistance at each seismic level. When isolation devices reach the ultimate horizontal displacement, they should exhibit stability under the most unfavorable axial load.
(2) The mechanical performance of isolation devices should remain stable under aging, creep, temperature variations, and seawater corrosion. The design of isolation devices should account for short-term and long-term adverse effects caused by uneven structural settlement and deck shrinkage deformation.
Two-stage design procedure
This study proposes a two-stage PBSD method for SISW, as illustrated in Figure 4. The procedure consists of two stages: Elastic design under CLE and displacement verification under MCE. The design parameters of the isolation devices are determined using the linear response spectrum method for the CLE level, while nonlinear time history analysis is employed to verify the deck displacement for the MCE level.
For wharf seismic design in China, the common practice is to adopt a transverse single-bay elastic frame for an analysis per response spectrum method. The virtual fixed-point method, outlined in many countries’ specifications[9-11] for simplified pile-soil interaction consideration, is adopted to approximate the soil's constraint on the piles by determining the point of fixity on each pile.
To provide a practical SISW design approach, this work adopts the transverse single-bay frame with the virtual fixed-point method for pile-soil interactions. The process for determining the point of fixity of piles is referenced in[10]. Additionally, in the CLE and MCE design stages, the wharf frame models are elastic and elastic-plastic, respectively.
Note: For detailed equations related to the physical quantities in Figure 4, one can refer to Section "Application of the PBSD method for wharf with seismic isolation system".
Seismic performance objectives and displacement limits
The design classification and performance objectives for the wharf are determined based on Table 1. Since SISW offers a well-defined and controllable seismic deformation mechanism, a higher design classification, such as H1 or H2, can be adopted. Prior to seismic design, the arrangement of wharf piles, section dimensions, and reinforcements are typically determined during the structural gravity design phase. Therefore, a numerical model of the wharf can be established for pushover analysis to derive the deck displacement limits, δCLE and δMCE, for the CLE and MCE levels, respectively, as introduced in Section "Seismic performance objectives for wharf with seismic isolation system".
CLE level design - determination of isolator parameters
The CLE level design aims to satisfy the displacement limit, δCLE, for SISW. At this stage, a transverse single-bay elastic frame is adopted for linear response spectrum analysis. Nonlinear isolators are approximated as an elastic system using an equivalent linearization method. The design parameters of the isolators are determined based on the principle of uniform pile stiffness.
The specific steps are as follows:
(1)The fundamental period of SISW, Teff, is suggested to be larger than 2.0 times that of the non-seismic-isolated wharf (NSIW), T0. According to the same design approach conducted in bridge engineering[20-22], it will ensure that the non-elastic deformation is concentrated on the isolators instead of the substructures.
(2)The equivalent lateral stiffness of SISW, Keff, is distributed among the piles according to the principle of uniform pile stiffness. The number of isolation devices, n, and the equivalent stiffness of each bearing, kieff-i, are determined accordingly. As there is flexibility in the distribution of pile stiffness at this stage, several distribution schemes can be compared comprehensively for optimization.
(3)Iteratively calculate Keff, Teff, ξeff, and the spectral structural displacement, Sd, based on the designed bearing arrangement until Sd is smaller than δCLE.
(4)Determine the design parameters of the isolation devices based on kieff-i, Sd, and the damping ratio of the isolation devices, ξieff-i.
MCE level design - verification of structural displacement
After determining the design parameters of the isolation devices that meet the displacement limit for the CLE level, a nonlinear time history analysis is performed on the SISW model to verify the structural response under the MCE level, considering the material nonlinearity of the piles and isolation devices.
The nonlinear time history analysis should use three or more sets of seismic records[10]. If fewer than seven sets of records are used, the maximum response from each set is taken as the structural response. The average response can be considered if seven or more sets of records are used for analysis.
Capacity Design and Berthing Force Verification
The deck, isolator connections, and steel connecting beams should be designed as capacity-protected elements by multiplying the calculated peak shear demand from element cross sections by 1.3 at the MCE level.
Additionally, ship berthing forces for the designated ship type should be verified due to the decrease in lateral stiffness after wharf isolation.
APPLICATION OF THE PBSD METHOD FOR WHARF WITH SEISMIC ISOLATION SYSTEM
This section presents a case study of a marginal wharf with plump piles in China to illustrate the application of the PBSD method for SISW. The target response spectra of CLE and MCE are determined by the seismic exceedance probabilities, the site classification, and the seismic zoning per "Code for Seismic Design of Water Transportation Engineering (JTS 146-2012)"[10]. Furthermore, for time history analysis, the input acceleration peak values are modulated to 0.2 g and 0.4 g for CLE and MCE levels, respectively, according to[10].
Original wharf information
Figure 5 illustrates the cross-section and plan view of the marginal concrete slabs and beams wharf with a berth for 5,000 tonnes of breakbulk. The wharf is located in a sheltered marine environment. The spacing between the wharf bays is 6.1 m, with a total length of 317 m and a width of 31.3 m. The soil at the wharf site consists of silty sand with an elastic modulus of 40 MPa, an effective unit weight of 9.2 kN/m3, an internal friction angle of 33°, and a cohesion of 20 kPa. The site soil is classified as site category II according to JTS 146-2012[10]. The silty sand layer is underlain by bedrock.
Figure 5. Transverse section and plan view of the original wharf. (A) Transverse section (dimensions in mm, elevation in m); (B) Plan view (in mm).
The wharf is constructed using C40 concrete with a deck thickness of 0.4 m. The crane track and transverse beams have a width and height of 1.2 m and 1.5 m, respectively. Circular RC cast-in-place piles with a diameter of 1m are employed for the wharf. The stacking pressure on the wharf surface is 30 kPa, and the gravity design value of the wharf structure is 8,427 kN. The seismic fortification intensity in the located region is Eight Degrees, according to JTS 146-2012[10]. During the gravity design phase, the preliminary selection for the longitudinal reinforcement of the pile is 24Φ24, the stirrup selection is Φ10@200 with HBP300 steel, and the protective layer thickness is 50 mm.
SISW performance levels and displacement limits
In this case, the H1 design classification is adopted based on Table 1, where "Minimal damage" and "Controlled and repairable damage" are defined for CLE and MCE, respectively.
According to Section "Seismic performance objectives for wharf with seismic isolation system", strain limits along pile plastic hinges are employed as quantified indicators for different performance levels per ASCE 61-14[11]. However, in SISW seismic design, the deck displacement limits at CLE and MCE levels (δCLE, δMCE) are required as the design demands. Therefore, it is necessary to convert material strains into structural displacements by pushover analysis.
The steps are as follows: (1) Conducting pushover analysis by applying increasing horizontal displacements to the wharf deck; (2) Taking the deck horizontal displacement as the design demand when the plastic hinge strains of piles reach limits stipulated in ASCE 61-14[11] under a certain performance level.
The numerical modeling method for pushover analysis can be found in Section "FE model introduction", including element selection, material constitutive, and boundary constraints. The displacement limits for each pile under different performance levels are determined and presented in Table 2.
Panel displacement (mm) corresponding to pile performance levels (pile-deck rigid connection)
Performance level | Pile A | Pile B | Pile C | Pile D | Pile E |
Minimal damage | 205 | 151 | 110 | 74 | 46 |
Controlled and repairable damage | 484 | 392 | 307 | 206 | 124 |
Life safety protection | 756 | 616 | 484 | 315 | 190 |
According to Table 2, pile E, with the shortest free length in the original wharf, is identified as the most critical pile regarding seismic shear force and bending moment. For SISW, the shortest non-seismic-isolated piles become the most critical piles after the seismic isolation of the inboard piles.
In this case, isolating inboard piles C, D, and E is preliminarily determined. Among the non-seismic-isolated piles, pile B, with a shorter free length than pile A, becomes the most critical pile for SISW. Therefore, the displacement limits of pile B under different performance levels are utilized as the design demands of SISW, namely δCLE = 0.151 m and δMCE = 0.392 m.
CLE level design
Determination of isolation period (Teff) and structural stiffness (Keff)
The fundamental period of the reference wharf (NSIW), To, is calculated using Equation (1). The designed mass of the wharf is mo = 860 t, and the lateral stiffness of the piles is ko = 43,742.1 kN/m [Table 3]. Therefore, To = 0.88 s.
Distribution of pile stiffness for SISW (kN/m)
Lateral stiffness | Pile A | Pile B | Pile C | Pile D | Pile E | Sum |
Before distribution | 2,289.5 | 3,501.6 | 5,745.3 | 10,399.6 | 21,806.2 | 43,742.1 |
Isolator stiffness kieff-i | - | - | 2,872.7 | 2,872.7 | 2,872.7 | - |
After distribution | 2,289.5 | 3,501.6 | 1,915.1 | 2,250.9 | 2,538.3 | 12,495.3 |
Since the period of SISW, Teff, is suggested to be larger than 2.0 times that of NSIW, T0, the initial design period of the SISW is Teff = 1.76 s, and the equivalent damping ratio ξeff is set to 0.1 initially. The displacement (Sd) of the CLE level response spectrum for the SISW deck is calculated using Equation (2).
Where C represents the seismic coefficient for the CLE acceleration response spectrum obtained from[10].
The calculation yields Sd = 0.065 m, which is less than the CLE displacement limit δCLE = 0.151 m. The structural stiffness (Keff) of the SISW is computed using Equation (3), resulting in Keff = 10,947 kN/m.
Where W represents the gravity design value of the wharf structure, which is 8,427 kN.
Stiffness distribution and displacement verification
The primary objective of SISW design is to mitigate the stiffness concentration effect on the inboard piles. To achieve this, the structural stiffness (Keff) of the SISW is distributed among the piles to balance their lateral stiffness, thereby determining the number of isolated piles and the equivalent stiffness (kieff-i) of the isolators. The lateral stiffness adjustment for each SISW pile is presented in Table 3.
As noticed in Table 3, the (lateral) stiffness of Piles C, D, and E demonstrates that placing isolation devices on their tops ensures uniform stiffness for each pile.
The structural stiffness of the SISW after isolation denoted as K'eff is 12,495.3 kN/m, slightly higher than the target stiffness Keff = 10,947 kN/m. The wharf period T'eff is recalculated as 1.65 s using Equation (2).
Considering the factors of isolated piles’ quantity and relative stiffness between isolators and piles on the structural damping ratio, Equation (4) is used to calculate the equivalent structural damping ratio of SISW
Where ξieff-I represents the damping ratio of the isolation bearing on the ith pile; ξip represents the damping ratio of the ith pile; Did represents the horizontal design displacement of the isolation bearing on the ith pile, which can be approximated by the deck spectral displacement Sd; kieff-i is the equivalent stiffness of the isolation bearing on the ith pile; kip denotes the lateral stiffness of the ith pile. In this case, ξieff-i is assumed as 0.3, and ξip is taken as 0.05.
Using Equation (4), the equivalent damping ratio of the wharf is ξ'eff = 0.132, and the deck displacement is calculated as S'd = 0.061 m, which is less than the limit of 0.151 m. These results indicate that the spectral displacement of the SISW falls within the "Minimal damage" range, thus complying with the CLE design objective.
Calculation of isolator design parameters
Friction pendulum isolators are employed here, considering the inherent self-centering capacity. Moreover, friction pendulum isolators can adjust stiffness and damping by modifying friction materials and curvature radius to adapt to the required seismic objectives. The hysteresis model for the friction pendulum isolator is depicted in Figure 6. Equations (5) and (6) determine the friction coefficient (μi) and curvature radius (Ri) of the isolation bearing, respectively. The calculated design parameters of the isolation bearing can be found in Table 4.
Design parameters for friction pendulum isolation devices
Isolator located pile | Wi (kN) | μi | Ri (m) | kii (kN/m) | kifps (kN/m) |
Pile C | 1,922 | 0.04 | 1.26 | 9,877.7 | 1,519 |
Pile D | 1,922 | 0.04 | 1.26 | 9,877.7 | 1,519 |
Pile E | 1,660 | 0.05 | 1.27 | 8,491.4 | 1,306 |
Where: μi -Friction coefficient, Ri -Curvature radius, Kii -Initial stiffness, kifps -Secondary stiffness, kieff-i -Equivalent stiffness, diy -Yield displacement, Did -Design displacement, and Wi -Axial force.
MCE level verification
To verify whether the deck displacement D follows the design limit δMCE at the MCE level, a finite element (FE) model of the SISW, featuring the single-bay frame in accordance with the CLE level design, is created for time history analysis.
FE model introduction
A transverse single-bay frame of SISW based on the virtual fixed-point method is established using ABAQUS/Standard[23], as depicted in Figure 7. Adopting the 2-D model consistent with CLE design stage at MCE level verification contributes to the consistency and practicality of the design method. Additionally, shows that the 2-D model with the virtual fixed-point method can provide conservative results in nonlinear seismic analysis[24], indicating safety towards design.
Figure 7. Schematic diagram of the numerical model of the SISW. The calculation Equation for "LSP" (pile strain penetration length at the pile-deck connection) is provided in[11].
Timoshenko beam elements (B21) are chosen for both the pile foundations and the deck, allowing for the consideration of shear and bending deformations. Through mesh sensitivity analysis during preliminary modeling, it was found that using 1,000 mm and 500 mm mesh sizes for the deck and piles ensured both accurate results and higher computational efficiency.
The mechanical behavior of the friction pendulum system is simulated using the "Connector" featured in ABAQUS, which defines the force-displacement relationship between the top pile node and the deck node at all degrees of freedom [Figure 7]. For translational motions between two nodes, nonlinear behavior
The connecting beams on the isolated piles are constrained through the "MPC Beam constraint" in ABAQUS, binding the degrees of freedom of adjacent pile nodes. Additionally, rigid connections between nodes are established using "Tie" in ABAQUS to connect the non-seismic-isolated piles and the deck.
For the boundary constraints, the bottom nodes of each pile are coupled to a reference point ("Coupling" in ABAQUS), and displacement constraints are defined at the reference point. During time history analysis, the reference point is subjected to horizontal seismic acceleration while other degrees of freedom are restricted.
The loading protocol consists of two steps. First, a static analysis step is conducted to apply gravity loads to the wharf. Then, an implicit dynamic analysis step is performed to simulate horizontal unidirectional seismic acceleration.
The deck and pile foundation are constructed using C40 concrete, which has an elastic modulus of
Parameters of the CDP model
Dilation angle | Eccentricity | fbo/fco | Kc | Viscosity parameter |
30° | 0.1 | 1.16 | 0.667 | 0.005 |
The reinforcement used in the pile foundation is HBP300 steel with an elastic modulus of 2 × 105 MPa. It has a yield strength of 300 MPa, an ultimate strength of 632 MPa, and an ultimate tensile strain of 0.14. The constitutive model employs a bilinear isotropic hardening model.
Input seismic accelerations
Three sets of natural seismic waves are selected from the PEER ground motion database[25] [Table 6]. Only one horizontal component with higher Peak ground acceleration (PGA) is considered to investigate the structural responses under unidirectional seismic action. Two factors are considered regarding the wave selection: (1) Consistency of target spectrum. The acceleration spectra of selected waves, scaled to the MCE level (PGA = 0.4 g), are compared with the target response spectrum, as depicted in Figure 8. For the NSIW and SISW models, the errors between waves’ mean Sa and the target spectrum at their fundamental periods are -3% and 20%, respectively, indicating a good match; (2) Conformance to wharf site category. The wharf case with site category II, based on JTS 146-2012[10], has a shear wave velocity at a depth of 30 meters (Vs30) ranging from 265-515 m/s. The Vs30 values for the three selected waves fall within this range.
Figure 8. Selected seismic waves and response spectra (MCE level). (A) Seismic waves (PGA = 0.4 g); (B) Acceleration spectra
Selected ground motion records
No. | Name | Country | Year | Magnitude | PGA (g) | Vs30 (m/s) | Duration(s) |
1 | Hollister | America | 1961 | 5.6 | 0.11 | 335.5 | 40 |
2 | Kobe | Japan | 1995 | 6.9 | 0.32 | 312 | 41 |
3 | Friuli | Italy | 1976 | 6.5 | 0.36 | 505.23 | 36 |
In the subsequent time history analysis, the seismic motion is scaled to the MCE level to verify the displacement response of the SISW during large earthquakes. Additionally, a five-second free vibration period is added after applying the seismic motion to determine the residual displacement of the structure following the earthquake.
Calculation results
The maximum displacement of the wharf deck under the three seismic waves is 0.154 m [Table 7], which is smaller than the displacement limit (δMCE = 0.392 m) of the MCE level. This indicates that the SISW achieves a "controlled and repairable damage" state at the MCE level.
Maximum deck displacement for NSIW and SISW (mm)
Wharf type | Deck displacement limits | Maximum deck displacement | |||||||
Minimal damage | Controlled and repairable damage | Life safety protection | Hollister | Kobe | Friuli | ||||
CLE | MCE | CLE | MCE | CLE | MCE | ||||
NSIW | 0-46 | 46-124 | 124-190 | 74.2 | 119.8 | 52.1 | 137.6 | 25.6 | 56.0 |
SISW | 0-151 | 151-392 | 392-616 | 70.7 | 154.1 | 72.9 | 147.8 | 34.7 | 61.1 |
The seismic demands on the protective components of the wharf deck, connecting beams, and isolated piles were verified, and the results indicate that the demands are smaller than the design load-bearing capacity of these components.
In the wharf example, a 5,000-ton class bulk carrier with a full load displacement of 6,700 t is considered. The design mooring speed is 0.2 m/s. Based on the Chinese Code for Harbor Engineering Loads
In conclusion, the two-stage seismic design confirms that the reference wharf can meet the seismic objectives of CLE and MCE levels for design classification H1. This demonstrates the effectiveness of the PBSD method for the SISW.
SEISMIC PERFORMANCE EVALUATION OF WHARF WITH SEISMIC ISOLATION SYSTEM
This section establishes a numerical model for an NSIW (with the same model size, pile foundation material, and modeling method as the SISW) to conduct time history analysis at CLE and MCE levels. The dynamic response results of the SISW in Section "Application of the PBSD method for wharf with seismic isolation system" are compared to discuss the differences between them in deck displacement, acceleration, pile bending moment, and structural energy dissipation.
Deck displacement
Figure 9 and Table 7 show the time histories and peak values of horizontal deck displacements for the two types of wharves.
The peak displacements of the SISW are generally higher than those of the NSIW. This is primarily due to the longer fundamental periods of the former. However, since the SISW decouples the motion between the deck and the inboard piles, the structural ductility and displacement limits are significantly increased. Combining Table 7 and Table 1, the SISW satisfies the displacement limits for the design classification of H1 for both CLE and MCE levels. In comparison, the NSIW achieves "Controlled and repairable damage" and "Life safety protection" at the CLE and MCE levels, respectively, corresponding to the design classification of H0. This demonstrates that using the same specification of pile foundations, SISW can achieve higher seismic performance objectives than NSIW.
Furthermore, as shown in Figure 9B, the NSIW experienced a residual displacement of approximately 40mm during the Kobe earthquake due to the ductile deformation of the inboard piles. In contrast, the SISW, by balancing the lateral stiffness of transverse piles, avoids short pile failure and residual displacement.
MCE level verification
Figure 10 presents a comparison of the time histories of horizontal displacement for isolated piles and the deck in the SISW. Table 8 compares the peak horizontal displacement of the two types of components.
Maximum horizontal displacement for deck and isolated piles in SISW (mm)
Components | Hollister | Kobe | Friuli | |||
CLE | MCE | CLE | MCE | CLE | MCE | |
Deck | 70.7 | 154.1 | 72.9 | 147.8 | 34.7 | 61.1 |
Isolated piles | 12.4 | 28.2 | 11.3 | 34.5 | 6.8 | 8.0 |
It is evident that through pile head isolation, the displacements of isolated piles and the deck are decoupled. The maximum displacements of isolated piles at the CLE and MCE levels are 12.4 mm and 34.5 mm, respectively, falling within the "Minimal damage" limit [Table 2]. This is attributed to the design shear transmitted to the pile foundation through the isolating bearings, which ensures that the displacement peaks of isolated piles remain within a controllable range. These findings indicate the effective control of seismic deformation mechanisms in the wharf through the isolation design.
Deck acceleration
Figure 11 and Table 9 illustrate a comparison of the time histories and peak values of horizontal deck accelerations for the two types of wharves, respectively. Notably, the deck accelerations of the SISW exhibit a decrease compared to the NSIW under all seismic wave conditions due to the longer natural period and higher energy dissipation capacity of SISW. The reduction in deck acceleration reaches 28%-40% for CLE and 18%-36% for MCE. Decreasing deck acceleration mitigates the seismic inertial effect and reduces the seismic response of the gantry crane and cargo on the deck.
Maximum deck acceleration for two types of wharves (g)
Wharf type | Hollister | Kobe | Friuli | |||
CLE | MCE | CLE | MCE | CLE | MCE | |
NSIW | 0.15 | 0.17 | 0.13 | 0.16 | 0.1 | 0.14 |
SISW | 0.09 | 0.13 | 0.09 | 0.14 | 0.07 | 0.09 |
Reduction rate (%) | 40.9 | 24.1 | 28.0 | 16.4 | 31.2 | 32.0 |
Pile bending moment
Figures 12 and 13 present the distribution of bending moments in the piles when reaching peak displacements for the two types of wharves. Table 10 presents their maximum pile bending moments when reaching peak displacements. In the SISW, all piles remain within the design elastic limits, while the outboard piles D and E of the NSIW enter the plastic stage during the MCE levels of the Hollister and Kobe earthquakes. Additionally, the bending moments in non-seismic-isolated piles A and B of the SISW are higher than the corresponding piles of the NSIW (increasing by a maximum of 43% and 46% for CLE and MCE, respectively). Conversely, the bending moments in the isolated piles C, D, and E are lower than those in the corresponding piles of the NSIW (decreasing by a maximum of 65% and 66% for CLE and MCE, respectively). These findings indicate that by balancing the stiffness of transverse piles, the SISW increases the proportion of seismic demand shared by the outboard piles, reduces the bending moment demand on the inboard piles, prevents short pile failure, and promotes balanced resistance of the wharf pile group against seismic action.
Figure 12. Comparison of pile bending moments (piles A and B) at the moment of maximum displacement for the two types of wharves.
Figure 13. Comparison of pile bending moments (piles C, D, E) at the moment of maximum displacement for the two types of wharves.
Maximum pile bending moments for the two types of wharves
Seismic inputs | Seismic levels | Pile A | Pile B | Pile C | Pile D | Pile E | |||||
NSIW | SISW | NSIW | SISW | NSIW | SISW | NSIW | SISW | NSIW | SISW | ||
Hollister | CLE | 503.5 | 1,137 | 604.5 | 1,409 | 847.9 | 336.4 | 1,131 | 452.6 | 1,440 | 507.9 |
MCE | 1,089 | 1,450 | 1,254 | 1,820 | 1,512 | 390 | 1,860 | 707 | 2,280 | 1,210 | |
Kobe | CLE | 831.9 | 1,115 | 954.5 | 1,201 | 1,189 | 501.5 | 1,608 | 729.6 | 2,236 | 1,004 |
MCE | 1,134 | 1,508 | 1,323 | 1,741 | 9,783 | 438.6 | 14,100 | 561.3 | 2,273 | 880.8 | |
Friuli | CLE | 406.3 | 574.1 | 530.5 | 686.3 | 650.3 | 230.9 | 781.9 | 365.9 | 1,037 | 578.5 |
MCE | 734.6 | 1,323 | 1,013 | 1,585 | 1,302 | 257.5 | 1,566 | 410.6 | 2,066 | 635 |
Pile bending moment
According to the Abaqus manual[23], The total energy balance of the wharf FE models can be written as:
Where: ALLWK - External work (available only for the whole model), ALLKE - Kinetic energy, ALLIE - Total strain energy, ALLVD - Energy dissipated by structural damping, ALLFD - Total energy dissipated through frictional effects (available only for the whole model).
In Equation (7), the kinetic energy (ALLKE) approaches zero after the earthquake. The frictional energy dissipated in the model contacts (ALLKE) is also zero, as the model does not consider contact interactions. Therefore, the input energy to the structure is primarily consumed in the form of internal energy (including total strain energy, ALLIE, and energy dissipated by structural damping, ALLVD)[28-30]. The total strain energy ALLIE consumed by wharf models consists of energy dissipated through structural plastic deformation, including pile hysteresis deformation and isolators' nonlinear sliding.
Figure 14 compares internal energy dissipation (ALLIE + ALLVD) among components for the two types of wharves at the CLE and MCE levels. In the case of the NSIW, all the seismic input energy is absorbed by the plastic deformation of the piles, aligning with the occurrence of pile ductile damage [Figure 9]. In contrast, the pile foundation of SISW accounts for a maximum of 55% and 47% of the total structural energy dissipation for CLE and MCE, respectively, while the remaining energy is dissipated through friction pendulum systems. These findings indicate that by concentrating the inelastic deformation of the wharf in the isolation layer, the SISW dissipates a significant portion of seismic energy through the isolation devices, significantly reducing ductile damage to the pile foundation.
CONCLUSION
In the seismic design of marginal pile-supported wharves, the ductile damage to pile foundations hampers post-earthquake operation, and the concentration of stiffness in inboard piles or batter piles results in severe local damage. To mitigate wharf pile damage and stiffness concentration under various seismic levels, this paper introduces a PBSD method for wharves with the SISW, wherein structural inelasticity is confined to the isolation layer. Subsequently, a wharf case is designed using the proposed method, and its seismic performance is numerically investigated. The major conclusions are summarized as follows:
(1) Performance-based seismic objectives for SISW are suggested. Classifications H1 and H2 with "minimal damage" objectives under CLE and MCE levels, respectively, are introduced to achieve high-performance seismic design for SISW.
(2) A two-stage PBSD method for SISW is proposed. During the elastic design stage under the CLE level, the isolators are designed based on the elastic response spectrum method. During the displacement verification stage under the MCE level, the deck displacement is verified based on the nonlinear time history analysis.
(3) A design case is presented to show the application for the proposed two-stage PBSD method. The nonlinear time history analysis results indicate that the SISW showed higher seismic performance than the NSIW. The SISW avoids "short pile failure" caused by increased stiffness in inboard piles compared to NSIW. By confining inelastic deformation to the isolation layer, SISW exhibits a higher energy dissipation capacity than NSIW, effectively controlling ductile damage in pile foundations.
This study proposed a practical PBSD method for SISW. The feasibility of the design method is verified with the design-based 2-D model, providing the potential for standardized design for SISW. In the future, the design method's applicability will be validated by 3-D numerical models with multi-directional seismic inputs[31,32]. Refined pile-soil interaction and the pile-wave interaction will also be considered.
DECLARATIONS
Authors’ contributions
Methodology, software, investigation, formal analysis, writing - original draft: Wang Z
Conceptualization, data curation, supervision, writing - review & editing: Cao M
Validation, investigation: Li J
Conceptualization, funding acquisition, data curation, supervision, writing - review & editing: Cui Y
Availability of data and materials
The datasets used and analyzed during the current study are available from the corresponding author upon reasonable request.
Financial support and sponsorship
This work was supported by the National Key Research and Development Program of China (Grant No. 2021YFB2600703).
Conflicts of interest
All authors declared that there are no conflicts of interest.
Ethical approval and consent to participate
Written informed consent for publication of this paper was obtained from the Dalian University of Technology and all authors.
Consent for publication
Not applicable.
Copyright
© The Author(s) 2023.
Appendix
REFERENCES
1. Chang SE. Disasters and transport systems: loss, recovery and competition at the Port of Kobe after the 1995 earthquake. J Transp Geogr 2000;8:53-65.
2. Burcharth HF, Bernal A, Blazquez R, et al. Seismic design guidelines for port structures. California; 2001. Available from: https://vbn.aau.dk/en/publications/seismic-design-guidelines-for-port-structures [Last accessed on 26 Sep 2023].
3. Serventi G, Jordan M, Fotinos G, Soderberg E. The design of earthquake damage repairs to wharves before the earthquake occurs. 2004, pp. 1-10.
4. Mondal G, Rai DC. Performance of harbour structures in Andaman Islands during 2004 Sumatra earthquake. Eng Struct 2008;30:174-82.
5. Werner S, Mccullough N, Bruin W, et al. Seismic performance of port de port-au-prince during the haiti earthquake and post-earthquake restoration of cargo throughput. Earthq Spectra 2011;27:387-410.
6. Memari M, Fakher A, Mirghaderi R.
7. Brunet S, de la Llera JC, Jacobsen A, Miranda E, Meza C. Performance of port facilities in Southern Chile during the 27 February 2010 maule earthquake. Earthq Spectra 2012;28:553-79.
8. Smith-Pardo JP, Bardi JC, Ospina CE.
9. Overseas Coastal Area Development Institute of Japan (OCDI). Technical standards and commentaries for port and harbour facilities in Japan. Tokyo; 2009. Available from: https://ocdi.or.jp/en/archives/775 [Last accessed on 26 Sep 2023].
10. Ministry of Transport of the People's Republic of China. Code for seismic design of water transportation engineering (JTS 146-2012). Beijing: China Architecture & Building Press; 2012.
11. American Society of Civil Engineers. Seismic design of piers and wharves (ASCE/COPRI 61-14)-1. Virginia: American Society of Civil Engineers; 2014.
12. Razavi SA, Fakher A, Mirghaderi R.
13. Harn R. Have batter piles gotten a bad rap in seismic zones? (Or everything you wanted to know about batter piles but were afraid to ask). Ports 2004: port development in the changing world; 2004, pp. 1-10.
14. Mito M, Uwabe T, Kitazawa S, Makabe T, Nakahara T. The shaking table tests and sesmic response analysison the pier with isolation system. Proc Civil Eng Ocean 2000;16:469-74.
15. Kilborn J, Harn R, Firat Y. Seismic retrofit of piers supported on battered piles using lead-rubber bearings. Ports 2010: building on the past, respecting the future; 2010, pp. 71-80.
16. Leal J, de la Llera J, Aldunate G. Seismic isolators in pile-supported wharves. Ports 2013: success through diversification, California; 2013, pp. 590-9.
17. Stringer S, Walter C, Pesicka B. An innovative method of enhancing deep water wharf stability. Ports 2013: success through Diversification, California: 2013; pp. 805-14.
18. Fendy J, Rastandi JI, Prakoso WA, Sjah J. Study of dimension variation effect on a batter piled wharf structure with seismic isolation systems. Mater Sci Forum 2020;987:10-4.
19. Davidson BJ, Bell DK, George SF. The implementation of seismic isolation in the retrofit of a large wharf. Bull N Z Soc Earthq Eng 2003;36:208-17.
20. Mayes RL, Buckle IG, Kelly TE, Jones LR. AASHTO seismic isolation design requirements for highway bridges. J Struct Eng 1992;118:284-304.
22. Ye A, Guan Z. Seismic design of bridges, 2nd ed. Beijing: China Communications Press; 2014.
23. Abaqus. Abaqus 6.14 analysis user’s manual. Dassault Systèmes Simulia Corp; 2014.
24. Smith-Pardo JP, Firat GY.
25. Pacific Earthquake Engineering Research Center. PEER ground motion database. Available from: https://ngawest2.berkeley.edu/ [Last accessed on 26 Sep 2023].
26. Ministry of Transport of the People's Republic of China. Load code for harbour engineering (JTS 144-1-2010). Beijing: China Communications Press; 2010.
27. Ministry of Industry and Information Technology of the People's Republic of China. Rubber fender (HG-T2866-2016). Beijing: Chemical Industry Press; 2016.
28. Mandal S, Rice J, Elmustafa A. Experimental and numerical investigation of the plunge stage in friction stir welding. J Mater Proc Technol 2008;203:411-9.
29. Fueyo JG, Cabezas JA, Domínguez M, Antón N, Villarino A. Energy distribution in dowel-type joints in timber structures when using expansive kits. Forests 2021;12:1200.
30. Quan H, Alderliesten R. The energy dissipation during fatigue crack growth in metallic materials. Eng Fract Mech 2022;269:108567.
31. Su L, Lu J, Elgamal A, Arulmoli AK. Seismic performance of a pile-supported wharf: three-dimensional finite element simulation. Soil Dyn Earthqe Eng 2017;95:167-79.
Cite This Article

How to Cite
Download Citation
Export Citation File:
Type of Import
Tips on Downloading Citation
Citation Manager File Format
Type of Import
Direct Import: When the Direct Import option is selected (the default state), a dialogue box will give you the option to Save or Open the downloaded citation data. Choosing Open will either launch your citation manager or give you a choice of applications with which to use the metadata. The Save option saves the file locally for later use.
Indirect Import: When the Indirect Import option is selected, the metadata is displayed and may be copied and pasted as needed.
About This Article
Copyright
Data & Comments
Data
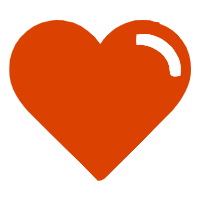
Comments
Comments must be written in English. Spam, offensive content, impersonation, and private information will not be permitted. If any comment is reported and identified as inappropriate content by OAE staff, the comment will be removed without notice. If you have any queries or need any help, please contact us at [email protected].