Recent advance in poly(bisphenol a carbonate) chemical recycling: catalysts, reaction strategies, and its applications
Abstract
The chemical upcycling of waste plastics into high-value-added products such as monomers, fuels, or fine chemicals represents a promising strategy for mitigating the adverse effects of massive end-of-life plastics. Poly(bisphenol A carbonate) (BPA-PC) stands out as a notable engineering plastic due to its exceptional overall performance; however, its durability and potential environmental toxicity make its recycling imperative. Although a lot of reviews about plastic degradation have been done before our review, the progress for plastic degradation needs to be constantly updated and summarized due to the rapid development of this field. Meanwhile, BPA-PC, as an important notable engineering plastic, previous reviews only focused on its depolymerization into monomers and missed their further conversion into final chemicals. which In this concise review, we summarize recent developments in the chemical upcycling of BPA-PC to valuable chemicals, emphasizing the role of various catalysts and reagents. Some of the most utilized chemical upcycling strategies such as alcoholysis, aminolysis and upcycling of BPA-PC in “polymer-to-polymer” format to reproduce new polymers are elucidated in detail. Finally, we provide insights into the future prospects of chemical upcycling for waste BPA-PC.
Keywords
INTRODUCTION
The annual global production of plastics has surpassed 460 million tons, yet only about 9% of waste plastics are recycled. Plastics have profoundly advanced human society, driving significant developments across various sectors[1-3]. However, their accumulation, due to their stable and non-biodegradable nature, has led to serious environmental problems, including soil pollution, marine pollution, and climate change[4-6]. Waste plastics are considered one of the major crises threatening the sustainable development. Consequently, the transition from the traditional “linear plastic economic model” to the promising “circular plastic economic model” has garnered extensive attention[7]. Currently, plastic recycling methods are primarily categorized into mechanical recycling, energy recovery (incineration), and chemical recycling[8,9]. Despite the widespread application of mechanical recycling and incineration for large-scale plastic waste treatment, these methods have critical drawbacks. Mechanical recycling results in materials with lower molecular weight and reduced thermal and mechanical performance compared to the virgin materials[10,11], while incineration releases hazardous gases and microplastics[12,13]. In contrast, chemical recycling of waste plastics into initial monomers or high-value chemicals[14,15] with high resource utilization, economic benefits, environmental friendliness and quality controllability will be regarded as a significant driving force for the circular plastic economic model.
As one of the fastest-growing engineering plastics, poly(bisphenol A carbonate) (BPA-PC) boasts excellent optical properties, heat resistance, impact resistance, toughness and flame retardancy. These attributes make BPA-PC highly versatile, finding applications in electronics, electrical appliances, sheet containers, automotive industry, medical devices and protective equipment[16]. It is projected that by 2024, the global demand for BPA-PC will reach 7.72 million tons[17]. However, the extraordinary durability of BPA-PC leads to its persistent accumulation in the environment, gradually releasing harmful bisphenol A (BPA)[18-20]. Therefore, the efficient chemical recycling of BPA-PC is imperative. The primary methods for chemical recycling of BPA-PC include pyrolysis, hydrolysis, reduction, alcoholysis, and aminolysis[21-26]. Pyrolysis, characterized by random and non-selective bond breaking, results in complex products and requires high reaction temperatures with significant energy consumption, thereby increasing costs and reducing practicability[27-29]. Additionally, carbonic acid, a by-product of BPA-PC pyrolysis, decomposes into carbon dioxide and water, complicating its reuse[30,31]. Although high conversion rates can be achieved in BPA-PC reduction under suitable conditions, the requirement for high-pressure hydrogen necessitates equipment with substantial pressure-bearing capacity, limiting scalability[32,33]. In contrast, employing alcohols or amines as nucleophilic reagents for depolymerization, such as in alcoholysis and aminolysis, presents a more promising alternative. These processes capture the carbonyl portion of polymers, generating high-value carbonyl products such as organic carbonates, carbamates and ureas[34]. Thus, they offer greater practical and economic value and have garnered significant attention in recent years.
In this comprehensive review, a systematic summary for chemical upcycling of BPA-PC to BPA and high-value-added carbonate derivatives with various depolymerization reagents was presented. According to the depolymerization reagents and products structures, the main categorization was as follows: (1) Alcoholysis (methanolysis, ethanolysis and phenolysis glycolysis); (2) Aminolysis of BPA-PC and depolymerization of BPA-PC by other nucleophilic reagents; (3) Reuse of BPA-PC depolymerization monomers to synthesis of new polymers. Moreover, we provide insights into the future potential and prospects of chemical upcycling for waste BPA-PC.
ALCOHOLYSIS OF BPA-PC
Methanolysis, ethanolysis and phenolysis of BPA-PC to linear carbonates
As shown in Figure 1, alcoholysis of BPA-PC with different structures of alcohols could obtain unified product BPA and corresponding carbonates. Dimethyl carbonate (DMC), diethyl carbonate (DEC), and diphenyl carbonate (DPC) could be produced with methanol, ethanol, and phenol as nucleophilic reagents for the chemical recycling of BPA-PC, respectively. This section is classified and summarized according to the types of catalysts.
Alkali metal catalysis
As early as 1998, Hu et al. initially investigated the alkali-catalyzed methanolysis of BPA-PC, which found that only 7% yield of BPA was obtained catalyzed by the NaOH (8.5 mol% relative to carbonate units of BPA-PC) in methanol at 60 °C after 330 min. However, the depolymerization rate was significantly accelerated when toluene or dioxane was added as a co-solvent. For example, in a mixed solvent of MeOH (1 mL) and toluene (1 mL), BPA-PC was completely depolymerized by a similar treatment for 70 min, and the products BPA (96%) and DMC (100%) were obtained in high yields. The reaction time could be further shortened by increasing the amount of the co-solvent. Since BPA-PC is virtually insoluble in methanol, a plausible reason for the accelerated action of co-solvents is that they can dissolve or solubilize the surface of solid BPA-PC and promote contact between reaction reagents, thereby increasing the rate of methanolysis[35]. Subsequently, Piñero et al. developed a greener process for alkali-catalyzed methanolysis of BPA-PC under supercritical or near-critical conditions in a semi-continuous laboratory plant[36]. The relationship between operating conditions such as reaction temperature, pressure, alcohol/co-solvent ratio, and catalyst concentration with product yield, selectivity, and reaction rate were systematically investigated. The best yields of BPA and DMC were achieved at the conditions of 120-140 °C, 10 MPa, and 1.5~2 kg/m3 NaOH/pure methanol, while the reaction selectivity and yield of the products were reduced with less toxic water used as the co-solvent. Chiu et al. used a batch autoclave reactor to explore the methanolysis of BPA-PC. It was found that under high temperature and subcritical conditions, BPA-PC could also be effectively depolymerized without adding a catalyst[37]. Under the optimal reaction conditions, when the molar ratio of MeOH/BPA-PC was 37.5 at 240 °C, it only took 5 min for complete methanolysis of BPA-PC, with the yields for BPA and DMC being 90.7% and 95.2%, respectively. Furthermore, Kim et al. revealed that increasing the MeOH/BPA-PC molar ratio to 71 in the temperature range of 160-220 °C without catalysts and toxic solvents resulted in higher BPA and DMC yields, but this further increased the energy and cost requirements. When the ethylene glycol (EG)/MeOH co-solvent system is used, the depolymerization yield does not grow[38].
The monomer BPA and DPC would also be obtained with phenol as a depolymerization reagent catalyzed by alkali metal halides, such as potassium fluoride. The product yields could reach as high as 90% and the turnover frequency (TOF) value was as high as 1,392 h-1. Moreover, the mixture of BPA, DPC and phenol was verified to be the starting point of the polymerization to produce new BPA-PC, thus completing the closed cycle[39].
Ionic liquid catalysis
Despite the above progress, strong alkali-base catalysts or high temperature and pressure are inevitable. It is desirable to explore more mild and efficient catalytic systems. As the pioneer of ionic liquid catalytic depolymerization, Liu et al. developed a new process for BPA-PC methanolysis using ionic liquids as catalysts[40,41]. Under the specified conditions, the yields of BPA and DMC exceeded 95% after 2.5 h using the ionic liquid 1-butyl-3-methylimidazolium chloride ([Bmim][Cl]) or 1-butyl-3-methylimidazolium acetate ([Bmim][Ac]) as a catalyst. Moreover, the ionic liquid could be reused 6-8 times with almost no loss of reactivity. This work avoided the use of toxic transition metal ions and organic solvents, providing a green and promising choice for the practical recycling of BPA-PC wastes.
Organic base catalysis
Organic catalysts are considered as metal-free eco-friendly catalysts. 1,8-Diazabicyclic [5.4.0] undecan-7-ene (DBU), as an organic catalyst, was first employed for the alcoholysis of BPA-PC[42]. Other organocatalysts, such as 1,4-diazobicyclic [2.2.2] octane (DABCO) and 4-(dimethylamino) pyridine (DMAP), were less active than the amidine base DBU. The study was extended to EtOH and EtOH/MeOH mixtures. The ethanolysis reaction yielded BPA and DEC in quantitative yields, whereas in MeOH/EtOH solutions, mixed products of BPA and carbonates [DMC, DEC, methyl ethyl carbonate (MEC)] were obtained. Besides, Alberti and Enthaler studied the methanolysis of BPA-PC by microwave-assisted heating in the presence of catalytic amounts of DMAP[43]. Excellent activities with a TOF of up to 1,164 h-1 were observed at 180 °C.
Zinc catalysis
In recent years, eco-friendly zinc-based catalysts were found to have high activity for alcoholysis as well. Yang et al. have successfully achieved the selective depolymerization of BPA-PC and other commercial plastics under mild conditions by utilizing the bis(trimethylsilyl) amino zinc ([Zn(HMDS)2]) as multifunctional catalyst and methanol as the depolymerization reagent[44]. Payne et al. also prepared a series of ZnII-complex catalysts based on half-salan ligands, which were successfully applied for the rapid methanol depolymerization (12-18 min) of BPA-PC even at room temperature and low catalyst loading conditions[45].
Compared with various catalysts mentioned above, Alkali and Zn-based catalysts have excellent reactivity, organic catalysts avoid the use of metals, and ionic liquid catalytic depolymerization processes provide a green and sustainable pathway for the practical recycling of BPA-PC wastes.
Glycolysis of BPA-PC to functionalized cyclic carbonates
Oku et al. investigated the reuse of waste BPA-PC as a chemical reagent using EG as a depolymerization reagent catalyzed by NaOH (0.1 equiv.) at 180 °C, yielding monohydroxyethyl ether of BPA (MHE-BPA, 42%), bishydroxyethyl ether of BPA (BHE-BPA, 11%), and BPA (42%) [Figure 2][46]. They concluded that ethylidene carbonate (EC) is an intermediate in the reaction which would react with the simultaneously formed BPA to obtain the final products. It was also found that quantitative conversion of BPA-PC to BHE-BPA was achieved within 20 min by adding additional EC (1.6 mol equiv.) to the same reaction system. Subsequently, Kim et al. further explored the non-catalyzed glycolysis of BPA-PC[47]. Unexpectedly, only BPA was found in the glycolysis product, which implied that EC did not react with BPA under non-catalytic conditions, but rapidly broken down into linear carbonates to produce CO2. Through the optimization of the reaction conditions, they found that BPA could achieve 95.6% of the maximum yield for only 85 min with weight ratio of EG/BPA-PC = 4, at 220 °C. To achieve efficient solvent-free glycolysis of BPA-PC, Nifant’ev et al. systematically studied the catalytic effects of acetate salts such as Li, Na, K, Mg, Ca and Zn on glycolysis of BPA-PC[48]. In the presence of Mg(OAc)2 (0.5 mol%, reaction for 15 min) or Zn(OAc)2
Functionalized cyclic carbonates are important intermediates in the manufacture of fine chemicals; propylene carbonate and vinyl carbonate, as representative cyclic carbonates, are widely used as polar non-protonic solvents and electrolytes in batteries[49,50]. Therefore, increasing attention has been paid to the conversion of BPA-PC to BPA and functionalized cyclic carbonates, since the carbonyl portion of BPA-PC can be used as an equivalent reagent instead of toxic CO and phosgene conforming to the goals of “green chemistry” and “atom economy”.
The pioneering work was done by Hata et al. in 2003; they treated BPA-PC with nucleophiles such as alkanedithiols, mercaptoethanol, aminoethanethiol, and aminoethanol in the presence of catalytic amounts of NaOH to obtain BPA and corresponding cyclic heterocarbonates [1,3-dithiopentyl-2-one (DTO) and 1,3-dithiane-2-one (DTA)] with high yields as shown in Figure 3[34]. It was proved that BPA-PC can be used as a phosgene equivalent for industrial purposes. In 2009, they continued to study the alcoholysis of BPA-PC by biomass-based polyols such as glycerol (Gly) and glucose (Glu) [Figure 4]. In addition to obtaining BPA, cyclic carbonates hydroxymethyldioxolane (HMDO) and dicarbonate (Glu-DC) were produced in 97% and 40% yields, respectively[51].
Figure 3. Depolymerization of BPA-PC by alkanedithiols, mercaptoethanol, aminoethanethiol, and aminoethanol. BPA-PC: Poly(bisphenol A carbonate).
Figure 4. Alcoholysis of BPA-PC by glycerol (Gly) and glucose (Glu) (isolated yield). BPA-PC: Poly(bisphenol A carbonate).
In addition, researchers have successively developed a variety of efficient catalytic systems. For example, in 2017, Iannone et al. developed a bifunctional acid/base catalyst based on the composition of nanostructured zinc oxide and tetrabutylammonium chloride (ZnO-NPs/NBu4Cl), which enabled efficient chemical recovery of BPA-PC in 7 h at 100 °C[52]. Diverse nucleophilic reagents, including water, alcohols, amines, polyols, aminols and polyamines, were universally applicable, and a group of high-value compounds, such as functionalized carbonates and ureas were obtained [Figure 5]. The catalyst was proved to be easy to recover and could be recycled many times without obvious decay of reactivity. However, a strong excess of the nucleophilic reagent was essential. In 2018, Quaranta et al. further studied the glycolysis reaction catalyzed by DBU based on their previous work[53]. The high-yield BPA monomer and the corresponding cyclic carbonate were smoothly obtained by depolymerizing BPA-PC waste with 1,2-propylene glycol or Gly. Do et al. also compared a series of transesterification catalysts for the alcoholysis of BPA-PC, and they found that 1,5,7-triazabicyclo[4.4.0]-dec-5-ene (TBD) exhibited the best performance, which led to the successful synthesis of a series of high-value-added organic carbonates at only 30 °C [Figure 6][54].
Figure 5. ZnO-NPs/NBu4Cl catalyzed depolymerization of BPA-PC (GLC yield; in brackets, isolated yields). BPA-PC: Poly(bisphenol A carbonate).
Figure 6. TBD-catalyzed alcoholysis of BPA-PC. (NMR yields; numbers in parenthesis are isolation yields). TBD: 1,5,7-triazabicyclo[4.4.0]-dec-5-ene; BPA-PC: poly(bisphenol A carbonate).
Jehanno et al. had new progress in 2020 using protic ionic salt TBD: methanesulfonic acid (MSA) as a catalyst to obtain five-membered heterocyclic monomers and six-membered cyclic carbonates with good to excellent yields without solvents [Figure 7][55]. In 2021, they successfully subjected this catalyst to the selective and sequential depolymerization of mixed plastics such as BPA-PC and polyethylene terephthalate (PET) under solvent-free conditions and high temperatures (100-160 °C)[56]. In 2023, Olazabal et al. further achieved the complete depolymerization of BPA-PC using 1-methylimidazole as a solvent and imidazole as a catalyst at 50 °C for 3 h, obtaining high trimethylene carbonate (TMC) yields (81%) [Figure 8][57]. This method was also applied to other nucleophilic reagents, resulting in the synthesis of a number of different cyclic carbonyl-containing intermediates.
Figure 7. TBD: MSA-catalyzed depolymerization of BPA-PC (NMR yields; numbers in parenthesis are isolation yields). TBD: 1,5,7-triazabicyclo[4.4.0]-dec-5-ene; MSA: methanesulfonic acid; BPA-PC: poly(bisphenol A carbonate).
AMINOLYSIS OF BPA-PC AND DEPOLYMERIZATION OF BPA-PC BY OTHER NUCLEOPHILIC REAGENTS
In addition to alcohols, other nucleophiles such as amines have also been studied for the depolymerization of BPA-PC. Hata et al. initially investigated the aminolysis of BPA-PC with dialkylamines in 2002[58]. However, the aminolysis process using monoamines such as dimethylamine and diethylamine was not successful, giving BPA monomers and other oligomeric carbamate intermediates low yields. When diamine was used instead of monoamines, the reaction proceeded smoothly to give BPA and cyclic urea derivatives such as 1,3-dimethyl-2-imidazolidinone (DMI), and the six-membered cyclic urea 2,6-dimethyl-2,6-diazacyclohexanone (DMDACH) in almost quantitative yields as shown in Figure 9. The aminolysis of carbamates with monoamines in the second step proceeds much more slowly than the cleavage of the carbonate group in the first step. However, with diamines, the intramolecular cyclization in the second step provides a kinetic advantage, thereby promoting the conversion to urea. In 2015, Singh et al. reported an unprecedented green method to react BPA-PC with primary amines to generate urea derivatives[59]. The carbonate moiety in BPA-PC was successfully extracted at 80 °C to prepare useful urea derivatives in moderate yields, without the use of any catalysts or toxic organic solvents [Figure 10].
Figure 9. Depolymerization of BPA-PC by DMEDA, DMDAP, (NMR yields). BPA-PC: Poly(bisphenol A carbonate); DMEDA: N,N’-dimethylethylenediamine; DMDAP: N,N’-dimethyl-1,3-propanediamine.
Figure 10. Depolymerization of BPA-PC by primary amines (isolated yield). BPA-PC: Poly(bisphenol A carbonate).
Recently, Wang et al. proposed an “amino-alcoholysis” strategy for upcycling BPA-PC plastic waste to BPA monomers and high-value-added chiral 2-oxazolidinone chemicals via ZnX2-catalyzed depolymerization of chiral amino alcohols under mild conditions [Figure 11][60]. In addition, high yields and selectivity were achieved in the sequential depolymerization of BPA-PC/PET mixed plastics. Using dimethyl sulfoxide (DMSO) as a strong polar solvent, the reaction can proceed smoothly without the necessity for a catalyst[61]. More importantly, BPA-PC could be efficiently depolymerized under solvent-free conditions with only one equivalent of depolymerizing agent. This “amino-alcoholysis” strategy was proved to be suitable for different types of commercial BPA-PC, and the feasibility of the method for practical application was further verified by scaling up the reaction. The recovered high-purity BPA was repolymerized to prepare new polymers, thus realizing closed-loop recycling. In addition, oxazolidinone compounds with different structures were obtained, demonstrating the generalizability of the method, which is important for plastic recycling and economic sustainability.
Figure 11. Depolymerization of BPA-PC by amino alcohols (NMR yields). BPA-PC: Poly(bisphenol A carbonate).
Jung et al. used hydroxamic acid as a nucleophilic reagent for TBD-catalyzed depolymerization of BPA-PC to obtain a series of dioxazolone[62]. The resulting dioxazolones could be subjected to one-pot C-H amidation to generate amides, which are important synthetic building blocks. As shown in Figure 12, amides 3a-3e were obtained in yields in the range of 69%-79%, while furanoic acid-derived dioxazolone showed low yields in transforming into amide 3f and BPA. This protocol promoted a green and sustainable process using BPA-PC as a carbonyl source instead of the toxic phosgene or 1,1’-carbonyldiimidazole (CDI) reagent in dioxazolone synthesis.
Figure 12. Depolymerization of BPA-PC by hydroxamic acid and one-pot C-H amidation. (isolation yields; numbers in parenthesis are NMR yields). BPA-PC: Poly(bisphenol A carbonate).
The chemical depolymerization of BPA-PC using α-hydroxyketone as a nucleophilic reagent was performed by Onida et al. in 2023[63]. The reaction was catalyzed by TBD in 2-Me-THF at room temperature to give higher value-added vinylidene carbonate in moderate to high yields (30%-97%, 13 instances) [Figure 13]. The success of TBD was attributed to its ability to activate both α-hydroxyketone and the carbonyl group of BPA-PC via hydrogen bonding. The practicality of the method was demonstrated by further scale-up experiments.
REUSE OF BPA-PC DEPOLYMERIZATION MONOMERS TO PRODUCE NEW POLYMERS
The efficient depolymerization of BPA-PC plastics through alcoholysis, aminolysis and other methods has resulted in a variety of multifunctional monomer products which could be utilized as raw materials for the synthesis of new polymer materials. In this regard, the use of hydroxyethyl ether products of BPA as rigid copolymerization monomers has attracted attention. Oku et al. have shown that the addition of additional EC is the key to the formation of bis(hydroxyethyl) ether (BHEEB) during glycolysis of BPA-PC in the presence of NaOH. Despite the fact that a number of inexpensive synthetic routes for EC have been developed, EC is not yet a commercial product, which restricts the industrial application of the method[46]. Instead, Lin et al. further developed a one-pot atmospheric pressure alkoxylation process based on the studies of Oku et al.[46,64]. On the basis of the completion of the first step in depolymerization, catalytic ZnO and cheap urea were added to the reaction mixture as carbonylation agents, and cyclic carbonates were generated in situ from EG or propylene glycol, which could be used to complete the ethoxylation or propoxylation process. Finally, bishydroxyethyl ether of BPA (BHE-BPA) or bishydroxypropyl ether of BPA (BHP-BPA) was generated as the final product. In comparison, this method offers higher selectivity and yields for the BPA-based diol (more than 90%). BHE and BHP products have been successfully applied as important raw materials in the preparation of high molecular weight polyurethane (PU) elastomers and plastics with excellent mechanical properties. In addition, Berti et al. have shown that it is possible to insert BPA groups into the polyester chain by reacting with BHEEB, resulting in terephthalate polyesters with higher mechanical properties and thermal stability[65].
In 2018, Pang et al. successfully achieved the synthesis of a series of BPA-PC homopolymers and copolymers using the chemical recycling of BPA-PC and a novel bicyclic diol octahydro-2,5-pentalenediol (OPD) deriving from naturally-occurring citric acid [Figure 14][66]. It was found that BHEEB not only compensated for the low reactivity of OPD, but also improved the brittleness of OPD-based polycarbonates without affecting other properties.
Gioia et al. further optimized the synthesis process of BHEEB [Figure 15], with an environmentally friendly catalyst K2CO3[67]. Subsequently, purified BHEEB was polymerized with succinic acid (SA) and isosorbide (IS) which were derived from renewable sources. In the presence of a tin-based catalyst (MTBO), low molecular weight polyesters were obtained with properties suitable for coatings applications [Figure 15]. Furthermore, a second route was developed for recycling BPA-PC [Figure 15]. BPA-PC reacted with vinyl carbonate via selective decarboxylation to produce polyether-carbonate, followed by partial depolymerization using diols to further reduce its relative molecular weight while increasing its hydroxyl group number. The oligomer is also suitable for powder coating applications.
Figure 15. Conversion of BPA-PC into novel polymers for powder coating applications. BPA-PC: Poly(bisphenol A carbonate).
Saito et al. used diols with different chain lengths to depolymerize BPA-PC into new diols containing carbonates, such as bis(3-hydroxypropyl) carbonate (3C), bis(4-hydroxybutyl) carbonate (4C) and bis(5-hydroxypentyl) carbonate (5C); they could be further applied to obtain a group of value-added aliphatic polycarbonates through organic catalyzed polycondensation [Figure 16][68]. These new polymers showed promising ionic conductivity values that could serve as sustainable polymer electrolytes for solid-state batteries. Wu et al. investigated the conversion of BPA-PC into multifunctional intermediates by depolymerization of BPA-PC with aliphatic diamines in the absence of catalysts under mild conditions
Figure 16. Conversion of BPA-PC to polymer electrolytes for batteries. BPA-PC: Poly(bisphenol A carbonate).
Figure 17. Conversion of BPA-PC into multifunctional intermediates to produce various PU polymers. BPA-PC: Poly(bisphenol A carbonate); PU: polyurethane.
Other studies of recycling BPA-PC to synthesize bio-based polycarbonates have also been reported. For example, in 2021, De Leo et al. achieved quantitative conversion of BPA-PC into BPA and DPC using zinc acetate and ionic liquids as catalysts and phenol as a nucleophilic reagent. The latter was subjected to a melt transesterification reaction with curcumin (CM) from natural polyphenols or its tetrahydrogenated colorless product (THCM) to obtain the corresponding bio-based polycarbonates CM-PC and THCM-PC, respectively [Figure 19][71]. An innovative study was carried out by Saito et al. in 2022. BPA-PC was upcycled with biobased vanillin derivatives into novel dialdehyde monomers (DVEC), which could be transformed into poly(imide-carbonate) [P(ImC)] by polymerization with primary amines as shown in Figure 20[72]. P(ImC) showed full recyclability under acidic conditions, thus enabling closed-loop recycling. It is noteworthy that the P(ImC) prepared using different diamines and triamines [tris(2-aminoethyl)amine (TREN)] as starting materials has readily tunable thermal and mechanical properties, which have broader application prospects.
Figure 19. Conversion of BPA-PC to bio-based polycarbonate THCM-PC. BPA-PC: Poly(bisphenol A carbonate).
CONCLUSION AND OUTLOOK
As summarized in this review, chemical recovery strategies for alcoholysis, aminolysis or other nucleophiles attack on BPA-PC have been widely studied. In order to achieve complete conversion of the polymer, researchers have systematically explored reaction conditions such as solvents, temperatures, pressures, concentrations of depolymerization reagents, types and loading of catalysts. However, in the early research, these processes generally have some drawbacks such as the use of high toxicity and environmental organic solvents or transition metal catalysts, harsh reaction conditions and large energy consumption. Therefore, increasing green and sustainable BPA-PC depolymerization processes have been developed in recent years via efficient and low-cost non-toxic metal catalysts, organic catalysts and ionic liquid catalysts, and green solvent systems. In addition, milder and greener catalyst-free or solvent-free reaction conditions have also been reported. Based on the development of BPA-PC upcycling technologies, the regeneration of new polymer materials from monomer products obtained through the BPA-PC upcycling was also achieved, indicating its potential practical values.
Although methanolysis can effectively yield BPA and DMC, the low boiling point of DMC makes it prone to mixing with residual reaction by-products, necessitating the use of multi-stage distillation or solvent extraction for separation. This complex separation process may limit the scalability of industrial applications. Compared with methanolysis, DEC obtained via ethanolysis has a higher boiling point, making separation relatively easier. However, due to potential azeotrope formation between DEC and by-products, precise distillation equipment is still required for effective separation. Given that aminolysis yields various amino derivatives, traditional separation methods may require multiple extractions or column chromatography techniques. To enhance separation efficiency, exploring continuous flow synthesis systems or membrane separation technology could reduce cross-contamination of products.
In the future, efficient and low energy consumption depolymerization technology is an important trend, which needs more efficient catalysts and sustainable depolymerization processes. Except for the homogeneous catalysis depolymerization of BPA-PC, heterogeneous catalysis processes have the advantage of allowing the catalyst to be reused several times, but they also exhibit low reactive activity. Meanwhile, the sustainable processes are also imperative demands for the industrialization of BPA-PC depolymerization. Moreover, although chemical catalysts play a crucial role in depolymerization reactions, the challenges of product separation and purification must be addressed to achieve large-scale industrial implementation of these methods. Future research should focus more on these aspects to develop cost-effective and sustainable recycling processes.
DECLARATIONS
Authors’ contributions
Proposed the topic of this review: Song T, Xu G
Prepared the manuscript: Li S, Zhu G, Yang R
Revised the manuscript: Hou H, Song T, Wang Q
Availability of data and materials
Not applicable.
Financial support and sponsorship
This work was supported by Shandong Provincial Natural Science Foundation (grant number ZR2024MB131 and ZR2023ME008), the National Natural Science Foundation of China 22002178), the Zhoushan Science and Technology Project (grant number 2020C02001) and the Major Science and Technology Innovation Program of Shandong Province (grant number 2022CXGC020604).
Conflicts of interest
All authors declared that there are no conflicts of interest.
Ethical approval and consent to participate
Not applicable.
Consent for publication
Not applicable.
Copyright
© The Author(s) 2024.
REFERENCES
2. Andrady AL, Neal MA. Applications and societal benefits of plastics. Philos Trans R Soc Lond B Biol Sci 2009;364:1977-84.
3. Geyer R, Jambeck JR, Law KL. Production, use, and fate of all plastics ever made. Sci Adv 2017;3:e1700782.
4. Bergmann M, Collard F, Fabres J, et al. Plastic pollution in the Arctic. Nat Rev Earth Environ 2022;3:323-37.
5. MacLeod M, Arp HPH, Tekman MB, Jahnke A. The global threat from plastic pollution. Science 2021;373:61-5.
6. Zhao X, You F. Life cycle assessment of microplastics reveals their greater environmental hazards than mismanaged polymer waste losses. Environ Sci Technol 2022;56:11780-97.
7. Zhao X, Korey M, Li K, et al. Plastic waste upcycling toward a circular economy. Chem Eng J 2022;428:131928.
8. Chen J, Wu J, Sherrell PC, et al. How to build a microplastics-free environment: strategies for microplastics degradation and plastics recycling. Adv Sci 2022;9:e2103764.
9. Rahimi A, García JM. Chemical recycling of waste plastics for new materials production. Nat Rev Chem 2017;1:BFs415700170046.
10. Badia J, Ribes-Greus A. Mechanical recycling of polylactide, upgrading trends and combination of valorization techniques. Eur Polym J 2016;84:22-39.
11. Ignatyev IA, Thielemans W, Vander Beke B. Recycling of polymers: a review. ChemSusChem 2014;7:1579-93.
12. Dai L, Zhou N, Lv Y, et al. Pyrolysis technology for plastic waste recycling: a state-of-the-art review. Prog Energy Combust Sci 2022;93:101021.
13. Thiounn T, Smith RC. Advances and approaches for chemical recycling of plastic waste. J Polym Sci 2020;58:1347-64.
14. Chen H, Wan K, Zhang Y, Wang Y. Waste to wealth: chemical recycling and chemical upcycling of waste plastics for a great future. ChemSusChem 2021;14:4123-36.
15. Xu G, Wang Q. Chemically recyclable polymer materials: polymerization and depolymerization cycles. Green Chem 2022;24:2321-46.
16. Hakimelahi HR, Hu L, Rupp BB, Coleman MR. Synthesis and characterization of transparent alumina reinforced polycarbonate nanocomposite. Polymer 2010;51:2494-502.
17. Singh R, Shahi S, Geetanjali. Chemical degradation of poly(bisphenol a carbonate) waste materials: a review. ChemistrySelect 2018;3:11957-62.
18. Esmer ÖK, Çağındı Ö. Safety of polycarbonate water carboys for residual and migration levels of bisphenol-A. Akademik Gıda 2020;18:411-20.
19. Saal FS, Vandenberg LN. Update on the health effects of bisphenol A: overwhelming evidence of harm. Endocrinology 2021;162:bqaa171.
20. Lopes-Rocha L, Ribeiro-Gonçalves L, Henriques B, Özcan M, Tiritan ME, Júlio C, Souza JCM. An integrative review on the toxicity of Bisphenol A (BPA) released from resin composites used in dentistry. Biomed Mater Res 2021;109:1942-52.
21. Antonakou EV, Achilias DS. Recent advances in polycarbonate recycling: a review of degradation methods and their mechanisms. Waste Biomass Valor 2013;4:9-21.
23. Thiyagarajan S, Maaskant-Reilink E, Ewing TA, Julsing MK, Haveren JV. Back-to-monomer recycling of polycondensation polymers: opportunities for chemicals and enzymes. RSC Adv 2022;12:947-70.
24. Huang J, He C, Li X, Pan G, Tong H. Theoretical studies on thermal degradation reaction mechanism of model compound of bisphenol A polycarbonate. Waste Manag 2018;71:181-91.
25. Yu Y, Gao B, Liu Y, Lu XB. Efficient and selective chemical recycling of CO2-based alicyclic polycarbonates via catalytic pyrolysis. Angew Chem 2022;61:e202204492.
26. Quaranta E. Rare Earth metal triflates M(O3SCF3)3 (M = Sc, Yb, La) as Lewis acid catalysts of depolymerization of poly-(bisphenol A carbonate) via hydrolytic cleavage of carbonate moiety: catalytic activity of La(O3SCF3)3. Appl Catal B 2017;206:233-41.
27. Montaudo G, Carroccio S, Puglisi C. Thermal and themoxidative degradation processes in poly(bisphenol a carbonate). J Anal Appl Pyrolysis 2002;64:229-47.
28. Puglisi C, Sturiale L, Montaudo G. Thermal decomposition processes in aromatic polycarbonates investigated by mass spectrometry. Macromolecules 1999;32:2194-203.
29. Siddiqui MN, Redhwi HH, Antonakou EV, Achilias DS. Pyrolysis mechanism and thermal degradation kinetics of poly(bisphenol A carbonate)-based polymers originating in waste electric and electronic equipment. J Anal Appl Pyrolysis 2018;132:123-33.
30. Grause G, Kärrbrant R, Kameda T, Yoshioka T. Steam hydrolysis of poly(bisphenol a carbonate) in a fluidized bed reactor. Ind Eng Chem Res 2014;53:4215-23.
31. Quaranta E, Mesto E, Lacalamita M, et al. Using a natural chlorite as catalyst in chemical recycling of waste plastics: hydrolytic depolymerization of poly-[bisphenol A carbonate] promoted by clinochlore. Waste Manag 2021;120:642-9.
32. Alberti C, Eckelt S, Enthaler S. Ruthenium-catalyzed hydrogenative depolymerization of end-of-life poly(bisphenol A carbonate). ChemistrySelect 2019;4:12268-71.
33. Westhues S, Idel J, Klankermayer J. Molecular catalyst systems as key enablers for tailored polyesters and polycarbonate recycling concepts. Sci Adv 2018;4:eaat9669.
34. Hata S, Goto H, Tanaka S, Oku A. Viable utilization of polycarbonate as a phosgene equivalent illustrated by reactions with alkanedithiols, mercaptoethanol, aminoethanethiol, and aminoethanol: a solution for the issue of carbon resource conservation. J Appl Polym Sci 2003;90:2959-68.
35. Hu LC, Oku A, Yamada E. Alkali-catalyzed methanolysis of polycarbonate. A study on recycling of bisphenol A and dimethyl carbonate. Polymer 1998;39:3841-5.
36. Piñero R, García J, Cocero MJ. Chemical recycling of polycarbonate in a semi-continuous lab-plant. A green route with methanol and methanol-water mixtures. Green Chem 2005;7:380.
37. Chiu SJ, Tsai CT, Chang YK. Monomer recovery from polycarbonate by methanolysis. e-Polymers 2008;8:12008.
38. Kim D, Kim B, Cho Y, Han M, Kim B. Kinetics of polycarbonate methanolysis by a consecutive reaction model. Ind Eng Chem Res 2009;48:6591-9.
39. Alberti C, Scheliga F, Enthaler S. Recycling of end-of-life poly(bisphenol A carbonate) via alkali metal halide-catalyzed phenolysis. ChemistryOpen 2019;8:822-7.
40. Liu F, Li Z, Yu S, Cui X, Ge X. Environmentally benign methanolysis of polycarbonate to recover bisphenol A and dimethyl carbonate in ionic liquids. J Hazard Mater 2010;174:872-5.
41. Liu F, Li L, Yu S, Lv Z, Ge X. Methanolysis of polycarbonate catalysed by ionic liquid [Bmim][Ac]. J Hazard Mater 2011;189:249-54.
42. Quaranta E, Sgherza D, Tartaro G. Depolymerization of poly(bisphenol A carbonate) under mild conditions by solvent-free alcoholysis catalyzed by 1,8-diazabicyclo[5.4.0]undec-7-ene as a recyclable organocatalyst: a route to chemical recycling of waste polycarbonate. Green Chem 2017;19:5422-34.
43. Alberti C, Enthaler S. Depolymerization of end-of-life poly(bisphenol A carbonate) via 4-dimethylaminopyridine-catalyzed methanolysis. Waste Biomass Valor 2020;11:4621-9.
44. Yang R, Xu G, Dong B, Guo X, Wang Q. Selective, sequential, and “one-pot” depolymerization strategies for chemical recycling of commercial plastics and mixed plastics. ACS Sustain Chem Eng 2022;10:9860-71.
45. Payne JM, Kamran M, Davidson MG, Jones MD. Versatile chemical recycling strategies: value-added chemicals from polyester and polycarbonate waste. ChemSusChem 2022;15:e202200255.
46. Oku A, Tanaka S, Hata S. Chemical conversion of poly(carbonate) to bis(hydroxyethyl) ether of bisphenol A. An approach to the chemical recycling of plastic wastes as monomers. Polymer 2000;41:6749-53.
47. Kim D, Kim B, Cho Y, Han M, Kim B. Kinetics of polycarbonate glycolysis in ethylene glycol. Ind Eng Chem Res 2009;48:685-91.
48. Nifant’ev IE, Pyatakov DA, Tavtorkin AN, Ivchenko PV. Chemical recycling and upcycling of poly(Bisphenol A carbonate) via metal acetate catalyzed glycolysis. Polym Degrad Stab 2023;207:110210.
49. Dong T, Zheng YJ, Yang GW, Zhang YY, Li B, Wu GP. Crosslinked resin-supported bifunctional organocatalyst for conversion of CO2 into cyclic carbonates. ChemSusChem 2020;13:4121-7.
50. Sathish M, Gopinath A, Madhan B, Subramanian V, Rao JR. Cyclic carbonate: a green multifunctional agent for sustainable leather manufacture. J Clean Prod 2022;356:131818.
51. Hidaka K, Iwakawa Y, Maoka T, Tanimoto F, Oku A. Viable chemical recycling of poly(carbonate) as a phosgene equivalent illustrated by the coproduction of bisphenol A and carbohydrate carbonates. J Mater Cycles Waste Manag 2009;11:6-10.
52. Iannone F, Casiello M, Monopoli A, et al. Ionic liquids/ZnO nanoparticles as recyclable catalyst for polycarbonate depolymerization. J Mol Catal A Chem 2017;426:107-16.
53. Quaranta E, Minischetti CC, Tartaro G. Chemical recycling of poly(bisphenol A carbonate) by glycolysis under 1,8-diazabicyclo[5.4.0]undec-7-ene catalysis. ACS Omega 2018;3:7261-8.
54. Do T, Baral ER, Kim JG. Chemical recycling of poly(bisphenol A carbonate): 1,5,7-Triazabicyclo[4.4.0]-dec-5-ene catalyzed alcoholysis for highly efficient bisphenol A and organic carbonate recovery. Polymer 2018;143:106-14.
55. Jehanno C, Demarteau J, Mantione D, et al. Synthesis of functionalized cyclic carbonates through commodity polymer upcycling. ACS Macro Lett 2020;9:443-7.
56. Jehanno C, Demarteau J, Mantione D, et al. Selective chemical upcycling of mixed plastics guided by a thermally stable organocatalyst. Angew Chem Int Ed Engl 2021;60:6710-7.
57. Olazabal I, Luna E, De Meester S, Jehanno C, Sardon H. Upcycling of BPA-PC into trimethylene carbonate by solvent assisted organocatalysed depolymerisation. Polym Chem 2023;14:2299-307.
58. Hata S, Goto H, Yamada E, Oku A. Chemical conversion of poly(carbonate) to 1,3-dimethyl-2-imidazolidinone (DMI) and bisphenol A: a practical approach to the chemical recycling of plastic wastes. Polymer 2002;43:2109-16.
59. Singh S, Lei Y, Schober A. Direct extraction of carbonyl from waste polycarbonate with amines under environmentally friendly conditions: scope of waste polycarbonate as a carbonylating agent in organic synthesis. RSC Adv 2015;5:3454-60.
60. Wang Z, Yang R, Xu G, Liu T, Wang Q. Chemical upcycling of poly(bisphenol A carbonate) plastic catalyzed by ZnX2 via an amino-alcoholysis strategy. ACS Sustainable Chem Eng 2022;10:4529-37.
61. Zhou X, Chai M, Xu G, Yang R, Sun H, Wang Q. Catalyst-free amino-alcoholysis depolymerization strategy: a facile and powerful tool for chemical recycling of poly(bisphenol A carbonate). Green Chem 2023;25:952-9.
62. Jung HJ, Park S, Lee HS, et al. Chemical upcycling of waste poly(bisphenol A carbonate) to 1,4,2-dioxazol-5-ones and one-pot C-H amidation. ChemSusChem 2021;14:4301-6.
63. Onida K, Fayad M, Norsic S, Boyron O, Duguet N. Chemical upcycling of poly(bisphenol A carbonate) to vinylene carbonates through organocatalysis. Green Chem 2023;25:4282-91.
64. Lin C, Lin H, Liao W, Dai SA. Novel chemical recycling of polycarbonate (PC) waste into bis-hydroxyalkyl ethers of bisphenol A for use as PU raw materials. Green Chem 2007;9:38-43.
65. Berti C, Colonna M, Fiorini M, Lorenzetti C, Marchese P. Chemical modification of terephthalate polyesters by reaction with bis(hydroxyethyl ether) of bisphenol A. Macro Mater Eng 2004;289:49-55.
66. Pang C, Jiang X, Yu Y, et al. Sustainable polycarbonates from a citric acid-based rigid diol and recycled BPA-PC: from synthesis to properties. ACS Sustain Chem Eng 2018;6:17059-67.
67. Gioia C, Vannini M, Celli A, Colonna M, Minesso A. Chemical recycling of post-consumer compact discs towards novel polymers for powder coating applications. RSC Adv 2016;6:31462-9.
68. Saito K, Jehanno C, Meabe L, et al. From plastic waste to polymer electrolytes for batteries through chemical upcycling of polycarbonate. J Mater Chem A 2020;8:13921-6.
69. Wu C, Chen L, Jeng R, Dai SA. 100% atom-economy efficiency of recycling polycarbonate into versatile intermediates. ACS Sustain Chem Eng 2018;6:8964-75.
70. Quaranta E, Dibenedetto A, Nocito F, Fini P. Chemical recycling of poly-(bisphenol A carbonate) by diaminolysis: a new carbon-saving synthetic entry into non-isocyanate polyureas (NIPUreas). J Hazard Mater 2021;403:123957.
71. De Leo V, Casiello M, Deluca G, et al. Concerning synthesis of new biobased polycarbonates with curcumin in replacement of bisphenol A and recycled diphenyl carbonate as example of circular economy. Polymers 2021;13:361.
Cite This Article

How to Cite
Download Citation
Export Citation File:
Type of Import
Tips on Downloading Citation
Citation Manager File Format
Type of Import
Direct Import: When the Direct Import option is selected (the default state), a dialogue box will give you the option to Save or Open the downloaded citation data. Choosing Open will either launch your citation manager or give you a choice of applications with which to use the metadata. The Save option saves the file locally for later use.
Indirect Import: When the Indirect Import option is selected, the metadata is displayed and may be copied and pasted as needed.
About This Article
Copyright
Data & Comments
Data
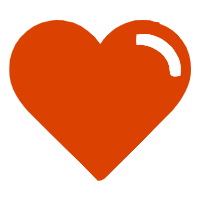
Comments
Comments must be written in English. Spam, offensive content, impersonation, and private information will not be permitted. If any comment is reported and identified as inappropriate content by OAE staff, the comment will be removed without notice. If you have any queries or need any help, please contact us at [email protected].