Tuning wettability of gallium-based liquid metal anode for lithium-ion battery via a metal mixing strategy
Abstract
Exploring highly stable alloy-type anodes for rechargeable lithium batteries is urgent with the ever-increasing demands for high energy density batteries. The liquid metal (LM)-based anodes demonstrate great potential in advanced lithium-ion batteries due to their high energy densities and self-healing performance. However, its high surface tension leads to poor wettability towards the current collector and higher interfacial contact resistance. In this study, we developed a new free-standing LM-based anode LM-W10/Cu foil with good wettability and machinability by mixing high-melting-point tungsten (W) nanoparticles. It greatly improves the inherent defects of poor interfacial contact and lithium diffusion kinetics between the LM and current collectors, reduces the tedious and costly electrode manufacturing process, and regulates lithium deposition behaviors. And this metal mixing strategy has a negligible effect on the self-healing nature of LM. Symmetric cells of LM-W10/Cu foil anodes displayed a low overpotential (~13 mV) and cycled stably for more than 8,000 h (4,000 cycles) at 0.5 or
Keywords
INTRODUCTION
With increasing demand for high energy density and excellent stability electrodes in next-generation lithium (Li) batteries, metal-based electrodes have attracted widespread attention due to their high specific capacity and outstanding electrode reaction catalytic function[1-3]. Alloy-type anode materials possessing numerous advantages with a high theoretical specific capacity, large volume energy density, low cost and moderate working potential to lithium could achieve efficient energy storage during Li alloying/dealloying, which makes them the most promising anode materials for next-generation rechargeable batteries[4-6]. Unfortunately, several problems remain, restricting their applications: (1) the inevitable volume expansion of the alloy-type anode during the lithiation process causes huge stress and strain on the material, which further causes cracking and pulverization, poor contact between the electrode materials and the current collectors; and (2) volume swelling during charge/discharge break the solid electrolyte Interphase (SEI) film on the surface of anodes, during subsequent charge/discharge cycle, the electrolyte will react with the newly exposed materials to form new SEI films, resulting in continuous consumption of electrolyte and increasing thickness of the SEI film, which will aggravate the decay of battery capacity. In efforts to address these challenges, a multitude of strategies have been proposed in the past years, involving the use of a wide variety of porous metal or liquid metal (LM)-based materials[7-11], gradient multi-porous metal electrodes[12,13], electrolyte additives[14,15], artificial SEI films[16,17], etc., which have been emerged in endlessly. Especially room temperature LM-based materials[18-20] not only have the self-healing property but also alleviate the generation of Li dendrite and volume expansion during the cycle process, and they also possess a high Li storage capacity and suitable Li-alloying potential. However, the inherent disadvantages, such as fluidity and high surface tensions, restrict their spreading over most of the current collectors, resulting in a significant decline in battery life span and capacity fading; these problems have attracted extensive attention in recent years[21].
LM anodes at room temperature mainly include metallic Hg and Ga, alloys NaK, GaSn, GaIn and GaInSn, etc. Among them, GaInSn ternary alloys (mass ratio is 7:2:1, referred to as LM later), owing to numerous special properties including the lowest melting point (10 °C), high surface tension (718 mN/m), high electronic conductivity (3.5 × 106 S/m), low viscosity (2.4 mPa s), low toxicity, self-healing ability, and chemical stability, have been widely applied in flexible electronics, energy storage, biomedicine health,
Inspired by the fact that high-melting-point metal particles mixed with LM could form an unalloyed cohesive mixture[29], we report a facial LM-W10 anode fabrication strategy by introducing tungsten (W) nanoparticles (φ 50 nm, 10 wt.%) to reducing the fluidity and surface tension of LM. After being mixed, the binder- and conductor-free LM-W10 anode presents low surface tension and high viscosity characteristics, and the composite can be easily dispersed over the current collector. A close contact interface can be thus obtained, and the reversible Li storage performance has been achieved. The present work indicates great application prospects in room temperature 3D printing manufacture of flexible devices.
EXPERIMENTAL
Materials
Gallium ingot (99.99% purity), Indium and Tin pellets (99.995% purity), and tungsten powder (99.9% purity, φ 50 nm) were purchased from Zhongnuo Advanced Material (Beijing) Technology Co., Ltd. The Cu foil (CF) was purchased through Shanghai Hesen Electrical Co., Ltd. All chemicals were used without further purification.
Preparation of materials and electrodes
The synthesis of LM (GaInSn) was carried out in an Ar-filled glove box (H2O, O2 < 0.1 ppm). The proportion of LM was Ga:ln:Sn = 7:2:1 (wt.%), placed in a nickel crucible, heated at 200 °C for 1 h, and constantly agitated to ensure that all components were distributed equally. The composite was collected after natural cooling. The LM and W (φ 50 nm) powders were weighed according to the mass ratio of 95:5, 90:10, 85:15, named LM-W5, LM-W10, and LM-W15, respectively, constant clockwise grinding using an agate mortar and pestle in the air until the LM form a paste-like consistency. The theoretical gravimetric capacity of the LM-W10 is 756 mAh/g (10 wt.% inactive W does not provide capacity). The commercial CF was cut into round pieces with a diameter of 14 mm, and the LM/CF, LM-W5/CF, LM-W10/CF and
Characterizations
The contact angle was tested by dropping materials on a glass slide at room temperature by a measurement instrument (JC2000D1, China). The morphology was observed by using an optical microscope (Keyence-VHX-950F) and scanning electron microscopy (SEM, Verios 460L, FEI). The surface elemental information was analyzed by an X-ray photoelectron spectrometer (XPS, ESCALAB 250Xi, ThermoFisher Scientific) and C1s (284.60 eV) as the reference line. X-ray diffraction (XRD) measurements were obtained from a Rigaku (MiniFlex 600) apparatus equipped with a Cu Kα radiation source. Cyclic voltammetry (CV) and electrochemical impedance spectroscopy (EIS) were tested by an electrochemical workstation (CHI 760E). EIS was performed at 105 Hz with an amplitude of 1 mV.
Battery assembly and electrochemical measurements
The electrochemical performance was carried out on CR2032. Celgard2400 was used as a separator. Symmetric cells with two identical electrodes were built; the electrolyte was 1 M lithium bis(trifluoromethanesulfonyl)imide (LiTFSI) solution in 1,3-dioxolane (DOL) and dimethoxymethane (DME) (1:1 by volume) with 1 wt.% LiNO3 additive. In full cells, all anodes (Li/LM-W10/CF, Li/LM/CF,
RESULTS AND DISCUSSION
The LM-W5, LM-W10 and LM-W15 composites were prepared using a simple one-step grinding method. As shown in Supplementary Figure 1, the pure LM (GaInSn) displays as a liquid droplet with a metallic luster; after mixing with different mass ratio Nano-sized W powder, the LM-W5 still contains a lot of LM droplets, showing not much change in the properties of LM; however, the LM-W10 and LM-W15 form a paste that displays the characteristics of low surface tension and high viscosity. To further evaluate electrochemical performance to select the optimal W content [Supplementary Figure 2], the Li/LM-W5/CF, Li/LM-W10/CF and Li/LM-W15/CF electrodes were prestored with 1 mAh/cm2 of Li, respectively, and assembled into symmetrical cells with two identical electrodes. The Li/LM-W5/CF exhibited a relatively high over-potential of 0.15 V and began to oscillate after 300 h, which was ascribed to high surface tension of LM-W5 leading to poor wettability with the current collector at a current density of 5 mA/cm2. The
As shown in Figure 1A and B, the schematic diagrams of LM-W10 and LM were presented, and contact angles were tested to investigate the wettability with current collectors. On the glass slide substrate, the contact angle of LM is 135°; by contrast, the LM-W10 could be easily spread on the glass slide, and it has strong adhesion to the substrate. Then, both LM-W10 and LM were spread on CF to fabricate LM-W10/CF and LM/CF. Observations from the optical microscope on morphology evolution [Supplementary Figure 3] show that the surface morphology of LM/CF is smooth and flat, while the LM-W10/CF is rough and convex. The mixing of W powder can completely change the physical properties of LM, thereby changing its surface tension and viscosity. According to the results of elemental distribution
Figure 1. The schematic diagram of (A) LM and (B) LM-W10, and corresponding contact angles on glass slide; optical microscopy photos of (C) LM/CF and (D) LM-W10/CF after lithiation at a current density of 1 mA/cm2.
It is vital to understand the Li alloying/dealloying process of LM-W10/CF and LM/CF for further performance optimization. The XRD patterns were recorded to analyze the phase composition
Figure 2. (A) The cyclic voltammetry of LM-W10/CF and LM/CF at 0.5 mV/s; (B) Nyquist plots of fresh and after five cycles of
To evaluate the electrochemical performance of the Li/LM-W10/CF and Li/LM/CF anode, symmetric cells were assembled to study the reversible Li storage performance. As shown in Figure 3A, both electrodes were deposited with 1 mAh/cm2 of Li and assembled into symmetrical cells with two identical electrodes, then fixed areal capacity of 0.5 mAh/cm2 in subsequent repeated cycles. The Li/LM-W10/CF displayed a relatively low over-potential (~13 mV) and remained stable for more than 8,000 h (4,000 cycles) at a current density of 0.5 mA/cm2. Meanwhile, the Li/LM/CF exhibited an over-potential of ~28 mV, and short-circuit occurred after about 3,700 h (~1,850 cycles). Figure 3B shows the performance of samples prestored with
Figure 3. Electrochemical performance of symmetric cells with Li/LM-W10/CF and Li/LM/CF. (A and B) the current densities were controlled to be 0.5 and 1 mA/cm2 (The inset were enlarged time-voltage curves); (C) nucleation over-potentials for lithiation in the three electrodes model cell at ~ 1 mA/cm2; (D) rate performance of Li/LM-W10/CF from 0.2 to 1 mA/cm2 (2 mAh/cm2 pre-deposited Li).
The Li/LM-W10/CF anode was fabricated into full cells coupled with LFP cathodes to investigate its practical applications. Figure 4A shows the cycling performance of full cells with different anodes at 1C. The Li/LM-W10/CF||LFP cell presents outstanding stability and maintains at 144 mAh/g with an average Coulombic Efficiency (CE) of 98.9%. The capacity retention is 95.15% even after 150 cycles with a fading rate of only 0.032% per cycle. By contrast, the discharge capacities of the Li/LM/CF||LFP and Li/CF||LFP cells rapidly decayed after 110 and 90 cycles, with relatively low CEs of 94.6% and 92.4%, respectively. The performance degradation of Li/LM/CF||LFP and Li/CF||LFP full cells is associated with the poor interfacial contact between originally low content of Li alloy compound and CF surface, which may lead to a "soft short circuit" within the battery. The poor contact also results in large electrode polarization and Li consumption in the subsequent cycle, thus deteriorating the life span of the battery.
CONCLUSIONS
In summary, a new binder- and conductor-free anode of LM-W10/CF was developed by one-step simple painting strategy. The introduction of high-melting-point W nanoparticles could effectively decrease the fluidity and surface tension of LM and make it easy to spread evenly over the current collector; the strategy has a negligible effect on the self-healing nature of LM. It greatly improves the inherent defects of poor interfacial contact and Li diffusion kinetics between the LM and current collectors, regulates lithium deposition behaviors, enhances the safety of LM anodes to a great extent and reduces the tedious and costly electrode manufacturing process, which makes this LM-W10/CF more suitable in the field of flexible electronic equipment. The LM-W10/CF composite electrode showed a low over-potential (~13 mV) and maintained cycle stability for more than 8,000 h (4,000 cycles) at 0.5 or 1 mA/cm2 in symmetric cells. Moreover, full cell tests upon pairing LFP cathodes demonstrated excellent cycling stability and rate properties and maintained a high-capacity retention of 95.15% after 150 cycles. Utilizing this ingenious and facile technology can definitely further improve the energy density of the LM anode and produce it in mass production. Furthermore, it is also appropriate for other alkali metal anodes[36-38] (e.g., Na and K) and will greatly expand the application field of flexible batteries in the future.
DECLARATIONS
Authors’ contributions
Materials synthesis, condition optimization, manuscript writing, electrochemical experiment testing and analysis: Lv Y
Intellectual contribution: Hu H
Acquired funding, supervised and guided the entire work, and made a major contribution to the writing and flow of the manuscript: Liu X
Availability of data and materials
Not applicable.
Financial support and sponsorship
This work was supported by the National Key Research and Development Program of China (2019YFA0705700) and the National Natural Science Foundation of China (22179095 and U1804255).
Conflicts of interest
All authors declared that there are no conflicts of interest.
Ethical approval and consent to participate
Not applicable.
Consent for publication
Not applicable.
Copyright
© The Author(s) 2024.
Supplementary Materials
REFERENCES
1. Liu H, Liu X, Wang S, Liu H, Li L. Transition metal based battery-type electrodes in hybrid supercapacitors: a review. Energy Stor Mater 2020;28:122-45.
3. Shen X, Liu H, Cheng XB, Yan C, Huang JQ. Beyond lithium ion batteries: higher energy density battery systems based on lithium metal anodes. Energy Stor Mater 2018;12:161-75.
4. Ni J, Zhu X, Yuan Y, et al. Rooting binder-free tin nanoarrays into copper substrate via tin-copper alloying for robust energy storage. Nat Commun 2020;11:1212.
5. Li Q, He G, Ding Y. Applications of low-melting-point metals in rechargeable metal batteries. Chemistry 2021;27:6407-21.
6. Shi Y, Yang W, Bai Q, Qin J, Zhang Z. Alloying/dealloying mechanisms, microstructural modulation and mechanical properties of nanoporous silver via a liquid metal-assisted alloying/dealloying strategy. J Alloys Compd 2021;872:159675.
7. Chi SS, Wang Q, Han B, et al. Lithiophilic Zn sites in porous CuZn alloy induced uniform Li nucleation and dendrite-free Li metal deposition. Nano Lett 2020;20:2724-32.
8. Yu J, Xia J, Guan X, et al. Self-healing liquid metal confined in carbon nanofibers/carbon nanotubes paper as a free-standing anode for flexible lithium-ion batteries. Electrochim Acta 2022;425:140721.
9. Yun J, Park BK, Won ES, et al. Bottom-up lithium growth triggered by interfacial activity gradient on porous framework for lithium-metal anode. ACS Energy Lett 2020;5:3108-14.
10. Won P, Jeong S, Majidi C, Ko SH. Recent advances in liquid-metal-based wearable electronics and materials. iScience 2021;24:102698.
11. Jia H, Wang Z, Dirican M, et al. A liquid metal assisted dendrite-free anode for high-performance Zn-ion batteries. J Mater Chem A 2021;9:5597-605.
12. Lv Y, Zhang QX, Li C, et al. Bottom-up Li deposition by constructing a multiporous lithiophilic gradient layer on 3D Cu foam for stable Li metal anodes. ACS Sustain Chem Eng 2022;10:7188-95.
13. Hyun G, Cao S, Ham Y, et al. Three-dimensional, submicron porous electrode with a density gradient to enhance charge carrier transport. ACS Nano 2022;16:9762-71.
14. Park S, Jeong SY, Lee TK, et al. Replacing conventional battery electrolyte additives with dioxolone derivatives for high-energy-density lithium-ion batteries. Nat Commun 2021;12:838.
15. Ming J, Cao Z, Wu Y, et al. New insight on the role of electrolyte additives in rechargeable lithium ion batteries. ACS Energy Lett 2019;4:2613-22.
16. Meda US, Lal L, M S, Garg P. Solid electrolyte interphase (SEI), a boon or a bane for lithium batteries: a review on the recent advances. J Energy Stor 2022;47:103564.
17. Liu W, Liu P, Mitlin D. Solid electrolyte interphases: review of emerging concepts in SEI analysis and artificial SEI membranes for lithium, sodium, and potassium metal battery anodes. Adv Energy Mater 2020;10:2070177.
18. Wu Y, Huang L, Huang X, et al. A room-temperature liquid metal-based self-healing anode for lithium-ion batteries with an ultra-long cycle life. Energy Environ Sci 2017;10:1854-61.
19. Meng J, Li C. Planting CuGa2 seeds assisted with liquid metal for selective wrapping deposition of lithium. Energy Stor Mater 2021;37:466-75.
20. Guo X, Zhang L, Ding Y, Goodenough JB, Yu G. Room-temperature liquid metal and alloy systems for energy storage applications. Energy Environ Sci 2019;12:2605-19.
21. Wei C, Tan L, Zhang Y, et al. Review of room-temperature liquid metals for advanced metal anodes in rechargeable batteries. Energy Stor Mater 2022;50:473-94.
22. Yang Z, Yang D, Zhao X, et al. From liquid metal to stretchable electronics: overcoming the surface tension. Sci China Mater 2022;65:2072-88.
23. Yan J, Lu Y, Chen G, Yang M, Gu Z. Advances in liquid metals for biomedical applications. Chem Soc Rev 2018;47:2518-33.
24. Han B, Xu D, Chi SS, et al. 500 Wh kg-1 class Li metal battery enabled by a self-organized core-shell composite anode. Adv Mater 2020;32:e2004793.
25. Sengupta S, Patra A, Akhtar M, Das K, Majumder SB, Das S. 3D microporous Sn-Sb-Ni alloy impregnated Ni foam as high-performance negative electrode for lithium-ion batteries. J Alloys Compd 2017;705:290-300.
26. Ozutemiz KB, Wissman J, Ozdoganlar OB, Majidi C. EGaIn-Metal interfacing for liquid metal circuitry and microelectronics integration. Adv Mater Inter 2018;5:1701596.
27. Ding Y, Guo X, Qian Y, Xue L, Dolocan A, Yu G. Room-temperature all-liquid-metal batteries based on fusible alloys with regulated interfacial chemistry and wetting. Adv Mater 2020;32:e2002577.
28. Wei C, Tan L, Tao Y, et al. Interfacial passivation by room-temperature liquid metal enabling stable 5 V-class lithium-metal batteries in commercial carbonate-based electrolyte. Energy Stor Mater 2021;34:12-21.
29. Kong W, Wang Z, Wang M, et al. Oxide-mediated formation of chemically stable tungsten-liquid metal mixtures for enhanced thermal interfaces. Adv Mater 2019;31:e1904309.
30. Guo X, Ding Y, Xue L, et al. A self-healing room-temperature liquid-metal anode for alkali-ion batteries. Adv Funct Mater 2018;28:1804649.
31. Wei C, Fei H, Tian Y, et al. Room-temperature liquid metal confined in MXene paper as a flexible, freestanding, and binder-free anode for next-generation lithium-ion batteries. Small 2019;15:e1903214.
32. Yu S, Kaviany M. Electrical, thermal, and species transport properties of liquid eutectic Ga-In and Ga-In-Sn from first principles. J Chem Phys 2014;140:064303.
33. Zhang Q, Lei X, Lv Y, Ma C, Liu X. Liquid metal-based cathode for flexible ambient Li-air batteries and its regeneration by water. Appl Surf Sci 2023;607:155074.
34. Savu SA, Casu MB, Schundelmeier S, et al. Nanoscale assembly, morphology and screening effects in nanorods of newly synthesized substituted pentacenes. RSC Adv 2012;2:5112-8.
35. Chao D, Ye C, Xie F, et al. Atomic engineering catalyzed MnO2 electrolysis kinetics for a hybrid aqueous battery with high power and energy density. Adv Mater 2020;32:2001894.
36. Tang S, Song F, Lu M, Han K, Peng X. Rational design of a visible-light photochromic diarylethene: a simple strategy by extending conjugation with electron donating groups. Sci China Chem 2019;62:451-9.
37. Wang C, Wang L, Li F, Cheng F, Chen J. Bulk bismuth as a high-capacity and ultralong cycle-life anode for sodium-ion batteries by coupling with glyme-based electrolytes. Adv Mater 2017;29:1702212.
Cite This Article
Export citation file: BibTeX | RIS
OAE Style
Lv Y, Hu H, Liu X. Tuning wettability of gallium-based liquid metal anode for lithium-ion battery via a metal mixing strategy. Energy Mater 2024;4:400018. http://dx.doi.org/10.20517/energymater.2023.90
AMA Style
Lv Y, Hu H, Liu X. Tuning wettability of gallium-based liquid metal anode for lithium-ion battery via a metal mixing strategy. Energy Materials. 2024; 4(2): 400018. http://dx.doi.org/10.20517/energymater.2023.90
Chicago/Turabian Style
Lv, Yang, Honghao Hu, Xizheng Liu. 2024. "Tuning wettability of gallium-based liquid metal anode for lithium-ion battery via a metal mixing strategy" Energy Materials. 4, no.2: 400018. http://dx.doi.org/10.20517/energymater.2023.90
ACS Style
Lv, Y.; Hu H.; Liu X. Tuning wettability of gallium-based liquid metal anode for lithium-ion battery via a metal mixing strategy. Energy Mater. 2024, 4, 400018. http://dx.doi.org/10.20517/energymater.2023.90
About This Article
Special Issue
Copyright
Data & Comments
Data
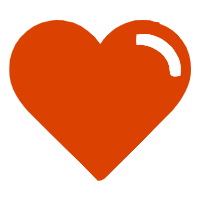

Comments
Comments must be written in English. Spam, offensive content, impersonation, and private information will not be permitted. If any comment is reported and identified as inappropriate content by OAE staff, the comment will be removed without notice. If you have any queries or need any help, please contact us at support@oaepublish.com.