In-situ Li2O-atmosphere assisted solvent-free route to produce highly conductive Li7La3Zr2O12 solid electrolyte
Abstract
Solid-state batteries have garnered attention due to their potentiality for increasing energy density and enhanced safety. One of the most promising solid electrolytes is garnet-type Li7La3Zr2O12 (LLZO) ceramic electrolyte because of its high conductivity and ease of manufacture in ambient air. The complex gas-liquid-solid sintering mechanism makes it difficult to prepare LLZO with excellent performance and high consistency. In this study, an in-situ Li2O-atmosphere assisted solvent-free route is developed for producing the LLZO ceramics. First, the lithium-rich additive Li6Zr2O7 (LiZO) is applied to in-situ supply Li2O atmosphere at grain boundaries, where its decomposition products (Li2ZrO3) build the bridge between the grain boundaries. Second, comparisons were studied between the effects of dry and wet routes on the crystallinity, surface contamination, and particle size of calcined powders and sintered ceramics. Third, by analyzing the grain boundary composition and the evolution of ceramic microstructure, the impacts of dry and wet routes and lithium-rich additive LiZO on the ceramic sintering process were studied in detail to elucidate the sintering behavior and mechanism. Lastly, exemplary Nb-doped LLZO pellets with 2 wt% LiZO additives sintered at 1,300 °C × 1 min deliver Li+ conductivities of 8.39 × 10-4 S cm-1 at 25 °C, relative densities of 96.8%, and ultra-high consistency. It is believed that our route sheds light on preparing high-performance LLZO ceramics for solid-state batteries.
Keywords
INTRODUCTION
With the development of electric vehicles and mobile vehicles in recent years, the need for lithium-ion batteries has increased significantly. Solid-state lithium metal batteries (SSLMBs) based on solid-state electrolytes are strong candidates for next-generation technologies due to their potential high safety and high energy density[1-3]. SSLMBs transcend the capacity limitations of conventional liquid lithium-ion batteries and answer the transportation industry's requirement for increased power and energy density[4,5]. Therefore, the solid-state electrolyte has received extensive research[6,7]; highly ionic conductive solid electrolytes (SEs), including sulfide electrolytes and oxide electrolytes, have been developed by numerous researchers[8-12].
Among these SEs, Li7La3Zr2O12 (LLZO) is attractive due to its high room-temperature ion conductivity
On the other hand, due to its high sintering temperature (Zr-site- and Li-site-doped LLZO typically exceeds 1,150 and 1,050 °C, respectively), the lithium loss is a serious problem[35,36]. Traditional mother powder [such as Li6.55La3Zr1.55Nb0.45O12 (Nb-LLZO) with Li content excess 15%] was usually adopted to cover the green pellet or to supplement Li2O atmosphere. The lithium atmosphere from the mother powder enters the green pellets from the exterior to the interior, which will result in slow and uneven sintering. It is essential to identify inexpensive lithium supplement materials and more advanced lithium supplement procedures. Zheng et al. have investigated the in-situ lithium supplementation method in previous studies[37,38]. However, they employed wet procedure, and the consistency of the as-prepared ceramics was not further investigated. For large-scale batch preparation of LLZO ceramics with high performance and high consistency, it is critical to simplify the experimental procedure as much as possible combining with in-situ lithium supplementation strategy.
The goal of this work is to create a large-scale preparation process platform for LLZO SEs that is dependable and repeatable. Due to the low cost of the Nb element, we chose Nb-doped LLZO as a typical material. The Nb-LLZO was prepared without solvent using the conventional solid-state method, and the high-efficiency sintering of a large number of green pellets was achieved by the “pellet-on-gravel” stacking sintering method[13]. The lithium-rich additive Li6Zr2O7 [LiZO, decomposes into Li2O + Li2ZrO3 during high temperature sintering (> 1,160 °C)] is selected to compensate for the loss of lithium atmosphere during the sintering process of the green pellets while also enhancing the bonding of grain boundaries and speeding up the ceramic sintering [Scheme 1]. In addition, detailed evaluations on the phase, relative density (RD), conductivity, microstructure, and grain revolution were conducted for ceramics prepared via wet and dry routes under different amounts of LiZO additives. Finally, the electrochemical performance of symmetric and Li-LiFePO4 cells fabricated with Nb-LLZO ceramics produced by the optimized conditions was evaluated to verify the application of these ceramics.
EXPERIMENTAL
Powder and ceramic preparation
Due to the high conductivity and low cost, a composition of Nb-LLZO (0% excessive Li, Li0) and 0/2/4 wt% LiZO (Li0L0/2/4) (Abbreviations and full names summarized in Supplementary Table 1) additive was utilized in this work. The precursors included LiOH·H2O (Aladdin, AR 98%), ZrO2 (NanJingMingShan, AR, 99.99%), La2O3 (Sinopharm Chemical Reagent, 99.95%), and Nb2O5 (Aladdin, 99.9%). The wet route was prepared as follows. Precursor powders with a stoichiometry ratio of Nb-LLZO were ball milled at 180 rpm (revolution) for 3 h with IPA and yttrium-stabilized zirconium oxide (YSZ) beads as the milling media. After drying at 55 °C for 12 h, dried powders were calcinated at 850 °C for 6 h to obtain cubic garnet-phase Nb-LLZO powders. These powders were sieved through P80 mesh and then further ball milled at 150 rpm (revolution) for 3 h to obtain a tailored powder. These fine powders were dried at 55 °C for 6 h and then sieved through 200-grit mesh. Furthermore, 1 g of sieved powder was uniaxially pressed into 12 mm green pellets at 3 tons. The solvent-free method saves solvents and drying processes compared to the wet route and differs in the material of the ball-milling tank. Scheme 2 depicts the preparation process for the conventional wet approach and the solvent-free method (hereafter known as the dry method). Table 1 displays the specific parameters for the dry and wet routes. LiZO powders were prepared by a solid-state reaction. After weighing the raw powders LiOH·H2O (Aladdin, AR 98%) and ZrO2 (NanJingMingShan, AR, 99.99%) at the molar ratio of lithium-to-zirconium equal to 4, they were ball-milled for 6 h at 400 rpm (rotation, revolution 200 rpm)[37]. The mixture was dried and calcined at 800 °C for 6 h to obtain the LiZO additive.
Scheme 2. Schematic diagrams of (A) the conventional wet-milling route and (B) the modified solvent-free route, respectively.
Preparation process comparison
Parameters | Wet | Dry |
Tank material and inner dimensions | Nylon, φ110 × h100 mm | Polyurethane, φ110 × h100 mm |
Grinding media | YSZ, φ10 mm × 100 g, φ5 mm × 600 g | |
Planetary milling machine | MITR Co Ltd, YXQM-8L. Main disk, φ420 mm | |
Mixing weight | ~206 g + 400 g IPA | ~206 g |
Revolution/rotation (mixing) | 180/360 r min × 3 h | |
Drying (mixing) | 55 °C × 12 h | No |
Loading in φ95 × h95 mm MgO | 120 g | 200 g |
Calcination | Open crucible, 3 °C min-1, 850 °C × 6 h | |
Tailoring weight | 80 g Nb4.5Li0 + 0/1.6/3.2 g LiZO + 160 g IPA | 80 g Nb4.5Li0 + 0/1.6/3.2 g LiZO |
Revolution/rotation (tailoring) | 150/300 r min × 3 h | |
Drying (tailoring) | 55 °C × 6 h | No |
Sieving | 200 grits, stainless steel screen mesh | |
Formation | φ12 mm, 1 g, 3 tons (~265 MPa) | |
Sintering | φ25 × h28 mm MgO Crucible & Lid, 7 pellets stack |
Characterizations
The crystal structures of powders and ceramics were characterized through powder X-ray diffraction (XRD) (Rigaku Ultima IV, 40 mA, 40kV) in the range of 10~60° at 8° min-1. The Archimedes method was utilized for calculating the densities of ceramics; pure EA is used as the medium. The theoretical density of Nb-LLZO was 5.14 g cm-3, which is calculated from XRD results. Applying the FullProf software suite, Rietveld co-refinement against XRD patterns was conducted. A scanning electron microscope (SEM, TESCAN-MIRA3) was used to investigate the ceramic's microstructure and the green pellets. The energy dispersive spectrum (EDS, Bruker QUANTAX), which was attached to the SEM, characterized the element mapping and point scanning. The ionic conductivity of ceramics is tested by electrochemical impedance spectroscopy (EIS, Zahner Zennium Pro) with a frequency range of 8 M Hz to 10 Hz or 1 Hz. To confirm the validity of the test, Ag is plated onto ceramic surfaces employing ion sputter (HeTongChuangYe, HTCY, JS-1600) as the blocking electrodes.
Electrochemical measurements
Dry-processed Nb4.5Li0L2 pellets were ground to parallel surfaces with a thickness of about 2 mm using a 1,200 grit SiC grind disk, and they were subsequently polished to a shine using 1,200 grit abrasive paper. Because of the negative interaction between metallic lithium and Nb-LLZO, there are two different approaches to building Li|Li symmetric cells. Li|Nb-LLZO|Li was assembled by gently rubbing the polished Nb-LLZO in a lithium soup at 330 °C until the ceramic surface was covered with clean molten lithium. As a comparison, two pieces of Li foil (φ10 mm × thickness 100 μm) were attached to the parallel faces, and a separator is inserted as a barrier between the lithium foil and the ceramic. Additionally, 5 μL(1 M LiPF6 in 1:1 vol/vol EC/DEC) of electrolyte was injected as lubricant on both sides of the separators to improve cycle performance. For Li|LFP full cells, the cathode included 70 wt% active material (70 wt% LFP, 20 wt% super P, 10 wt% PVDF) with an average mass loading of ~3.08 mg cm-2. A small amount of electrolyte (10 μL, 1 M LiPF6 in 1:1 vol/vol EC/DEC) is used to wet the cathode-garnet electrolyte interface. All the symmetrical and full cells are assembled in coin-2032 cells. And to separate water and oxygen, all of the aforementioned activities are completed in a glovebox filled with argon (O2 < 0.5 ppm, H2O < 0.1 ppm).
RESULTS AND DISCUSSION
Precursors mixed using wet and dry processes exhibit various XRD characteristic peaks after calcination
Figure 1. Phase result of sintered powders. XRD patterns of as-calcinated Li6Zr2O7 and Li0 via wet and dry routes.
XRD patterns of Li0L0 and Li0L4 powders tailored by dry and wet routes with corresponding Rietveld refinement are shown in Figure 2. Four structure models, including cubic and tetragonal garnet-type LLZO, monoclinic-type LiZO, and trigonal-type La2O3, were applied to refine the diffraction data. The phase proportions were listed in Table 2. Minor La2O3 phase occurred in all powder refining data, and the dry routes are more apparent than the wet technique for this phenomenon. Cubic LLZO remained the dominant phase in all refinement XRD data, comprising 98% or more. As a result, the main phase is used as the basis for the evaluation of powder lattice parameters in this work (i.e., cubic phase LLZO). Dry ball milling is more effective at breaking the lattice because it is solvent-free, which causes the LLZO particles to undergo amorphization to a greater extent. There was a significant difference in the lattice parameters between fine powders produced by dry and wet routes. The lattice parameters of wet-tailored powders (Li0L0/4 wet) were all higher than 13.0 Å, whereas the lattice values of dry-tailored powders (Li0L0/4 dry) were all near to 12.9 Å. The enlarged lattice after wet tailoring originated from the solvent's absorption of moisture, which introduced serious Li+/H+ exchange. Powders in cubic LLZO with less Li+/H+ exchange after dry tailoring would benefit the sintering results.
Figure 2. Refinement profiles of XRD data of (A) Li0L0 wet, (B) Li0L0 dry, (C) Li0L4 wet, and (D) Li0L4 dry powders. The software applied for Refinement is Fullprof suite. The CIF files adopted for refinement are La2O3, Li6Zr2O7, tetragonal LLZO, and cubic LLZO from the COD database.
Ratios of c-LLZO and t-LLZO, Li6Zr2O7 and La2O3 phases
Sample | Cell parameter (Å) | Ratio (%) | Error | |||
c-LLZO | c-LLZO | t-LLZO | La2O3 | LiZO | Rwp | |
Nb4.5Li0L0 Wet | 13.035 | 97.87% | 1.87% | 0.26% | 0% | 6.39% |
Nb4.5Li0L4 Wet | 13.020 | 98.93% | 0.11% | 0.21% | 0.75% | 6.11% |
Nb4.5Li0L0 Dry | 12.901 | 98.68% | 0.72% | 0.6% | 0% | 6.23% |
Nb4.5Li0L4 Dry | 12.899 | 97.48% | 0.97% | 0.8% | 0.75% | 6.22% |
The Thermogravimetric analysis- differential scanning calorimetry (TG-DSC) results of as-tailored Li0L0~4 powders were shown in Figure 3. Obviously, dry and wet tailoring gave the powders different characteristics. For wet tailoring powders, there were five stages of weight loss, whereas just two steps for the dry procedure. When cooled in an ambient setting, the sintered powders will absorb H2O and CO2 from the ambient atmosphere, forming chemical adsorption materials on the surface of LLZO[45]. After wet tailoring, the weight loss stages dramatically increased to five in comparison with the dry route, indicating more serious and complex pollution in wet-milled powders. Wet-milling powders lost more weight overall than 10 wt%, indicating a considerable protonation of wet tailored powders[46]. The weight loss of Li0L0 and Li0L4 powders after dry tailoring at stage VII was just
Figure 3. TG-DSC of Li0L0 and Li0L4 powders treated with wet-dry routes. The purge gas is 80% N2 and 20% O2 monitoring the practical calcination and sintering under ambient air. The I~VII stages corresponded to the following reactions: I: 20~60 °C, CH3CHOHCH3 (l) → CH3CHOHCH3 (g); II: 80~230 °C, LiOH·H2O → LiOH·0.5H2O + H2O (g), H2O (Absorbed) → H2O (g), CO2
Figure 4 shows the cross-sectional morphology of the as-sintered Li0L0 and Li0L4 pellets, proving the good sintering results for dry milled Li0L4 powder. Both the dry and wet milled Li0L0 cannot be densified at 1,220 °C, where many worm-like grains with rough surfaces and lots of pores occurred
Figure 4. Cross-section SEM images of the Li0L0 and Li0L4 pellets sintered at (A) 1,220 °C × 20 min, (B) 1,260 °C × 20 min.
Nyquist plots of as-sintered L0/4- wet/dry ceramics further proved the effect of Li2O atmosphere in-situ provided by Li6Zr2O6. Li0L0 ceramic sintered at 1,220 °C contained two semicircles [Figure 5A], which corresponded to the grains and grain boundaries, respectively. The inflection point between the first and second semicircle for Li0L0 was 215 kHz, where this point was defined as the terminal frequency (TF). Dry-processed ceramics had a much higher TF than that of wet-processed ceramics in the second flat semicircle in the mid-low frequency range, where all ceramics sintered at 1,220~1,280 °C exhibited this feature
Figure 5. Normalized Nyquist plots of Li0L0/4 ceramics sintered at (A) 1,220 °C × 20 min and (B) 1,260 °C × 20 min. (C and D) DRT transition of Nyquist plots. g: grain, bulk. gb: grain boundary. (E and F) Resistance data calculated from the DRT results. (G) Li+ conductivities and (H) Relative densities of Li0L0/4 sintered at 1,220~1,280 °C for 20 min.
Figure 5G and H depicts the conductivities and RD of Li0L0/4 ceramics at room temperature (23.7 °C). The RD and conductivity of all Li0L0 samples improved with increasing sintering temperature, whereas the Li0L4 exhibited a decreasing trend above 1,240 °C. The conductivities of Li0L4 ceramics maintained above
As shown in Figure 6, the evolution of grain and grain boundaries was studied to reveal the advantages of LiZO additive during the dry route. The densification procedure for Nb-LLZO was divided into six stages from green pellet to dense ceramic. Numerous amorphous, glassy substances with dark hues were found among grains in wet ball-milling powders [Figure 6B and D]. Deep protonated LLZO after wet milling would first decompose at 300-700 °C and then react with Li-rich contaminations at 700-1,000 °C during the sintering process[45], which hindered densification. Compared to the particles contaminated with solvents, dry milled powders were clean, indicating the few contaminations. When sintered at 1,080 °C for one minute (Stage 2), where the lithium-rich additive LiZO did not release Li2O, all particles had grown with small necks developing between grains. Wet processed samples delivered a lower density than dry processed samples. The green pellets pressed from dry milled powder usually delivered high densities due to the few contaminations in powders. As the temperature increased to over 1,160 °C (Stage 3), cross-sectional microstructures of Li0L0 and Li0L4 ceramics differed substantially. The grains in Li0L4 grew significantly large with clear polyhedron surfaces and obvious linking necks. In contrast, the grains of the Li0L0 samples almost retained the same shape as that in stage 2. At stage 4, Li0L4 densified more with well-developed edges and distinct grain boundaries. In contrast, the Li0L0 grains failed to form a unique polyhedral shape, and they began to join with each other. At stage 5, the grains of Li0L4 further developed. The Li0L4-dry ceramic was almost densified while the Li0L4-wet ceramic contained lots of pores. In contrast, the Li0L0 ceramics exhibited trans-granular fractures, indicating the weak bulk strength, which might originate from the lack of Li in the LLZO lattice. At stage 6, grains in Li0L4-dry were tightly connected with clear grain boundaries and few isolated pores. In Li0L4-wet, the pores could not be completely evacuated. Li0L0 dry reached a relatively tight cross-sectional microstructure in trans-granular fracture at a high temperature of 1,300 °C, whereas Li0L0-wet exhibited abnormally grown grains with a great number of pores.
Figure 6. Evolution of the grain morphology. Cross-sectional SEM images of Nb-LLZO pellets: (A) Li0L0 wet, (B) Li0L0 dry, (C) Li0L4 wet, and (D) Li0L4 dry.
The evolution of ceramic microstructures explicated the role of LiZO in ceramic sintering: promoting the grain growth and enhancing grain boundary adhesion. The influence of dry and wet routes on particles was also clearly demonstrated: ceramics manufactured by the dry route could achieve a higher density than that by the wet route. Li0L4-dry required just 1,220 °C × 1 min to reach an RD higher than 90%. As shown in Figure 7, the changes in the RD and ion conductivity of the samples correlated to their microstructures.
Figure 7. Conductivity and relative density of Nb-LLZO ceramics shown in Figure 6.
The role of LiZO at grain boundaries was further revealed by EDS, as shown in Figure 8. A typical triangular grain boundary with glue-like segregations was selected to show the distributions of La, Zr, Nb, and O. Figure 8B depicted the element ratios at points 1, 2, and 3. Zr, La, and O ratios at bulk grains (point 3, 11.4%, 16.2%, and 67.8%, respectively) were similar to stoichiometric Nb-LLZO. The Zr ratio at the grain boundary was doubled (19.4%) to the ratio at the bulk grains. Additionally, the Zr-O ratio of the two kinds of sites ranged between 1:3 (point 3) and 2:7 (points 1 and 2); the second phase at the grain boundary was predominantly composed of Li2ZrO3 or LiZO species. A small excess of Nb may originate from the formation of LixNbOy from Li2O and Nb during sintering[27].
Figure 8. Second phase species analysis at grain boundary. (A) cross-sectional SEM images of Li0L4 dry ceramics. (B) element analysis results of points at the triple-point grain boundary and grain.
Cross-sectional triangular grain boundaries were further characterized by X-ray photoelectron spectroscopy (XPS) [Figure 9]. The ceramic sample was sintered at 1,220 °C × 1 min and then was prepared inside an Ar-filled glovebox avoiding the contamination from trace-level H2O and CO2. Ar+ sputtering was performed on the surface of the stripped LLZO to remove contamination before test. And due to the unevenness of the ceramic cross-section, the binding energy of elements might be partially shifted. The O 1s peak at 54.9 eV in Li0L0 dry represents the Nb-LLZO[52]. The O 1s spectra of Li0L4 dry were deconvoluted into two peaks at 53.7 and 55.9 eV corresponding to Nb-LLZO and Li2O, respectively[53]. In Figure 9B, all Zr 3d spectra exhibited a doublet with a fixed difference of 2.43 eV due to the spin-split coupling between 3d5/2 and 3d3/2. For dry Li0L0, just one chemical environment peak of Zr could be identified, which corresponded to the Zr in cubic LLZO[53,54]. The Zr 3d spectrum of the Li0L4 sample exhibited evident distortion and widening, revealing two different chemical environments of Zr. The main peak of Zr 3d5/2 located at the 182.8 eV corresponds to the Zr in the cubic LLZO while the side peak of the Zr 3d5/2 at the 181.8 eV was ascribed to the Li-Zr-O (e.g., Li2ZrO3)[55,56] at the cross-section of the sample. The Li-Zr-O could not be detected in the Raman test [Supplementary Figure 6], which originated from the small amount of Li-Zr-O existing at the narrow grain boundaries. Nevertheless, these results further proved the decomposition of LiZO to Li2O and Li-Zr-O at the grain boundaries.
Figure 9. Second phase species analysis at grain boundary. XPS spectra of (A and B) Li 1s, Zr 3d of the cross-section pellets for Li0L0 dry and Li0L4 dry.
The production of LLZO ceramic pellets was conducted by applying Li0L2 as the composition via a solvent-free method. Li0L4 was not adopted due to the relatively low conductive decomposed Li-Zr-O compounds. Plenty of Li-Zr-O compounds in-situ formed at grain boundaries could improve the robustness of controlling the grain growth; however, these materials would hinder the Li+ transportation across the grain boundaries. Figure 10A depicted the RD of seven parallel samples of Li0L2 sintered by four sintering conditions. All these samples had an RD higher than 96%. The consistency was examined using standard deviation (S.D.). Clearly, the average RD of ceramics manufactured by dry method was high with low S.D. This consistency was also proved in EIS. Figure 10B depicted the Nyquist plots (25 °C) of Li0L2-dry sintered at 1,300 °C for 1 min, and Supplementary Figure 7 depicted the data for other samples. All the plots delivered only one semicircle corresponding to dense microstructure. All parallel pellets in each group sintered under four conditions showed high consistency. The Li0L2-dry sintered at 1,300 °C for 1 min had the highest RD and conductivity [Figure 10C] of 96.8% and 8.39 × 10-4 S cm-1, respectively. The RD and conductivities of these parallel pellets sintered at different positions inside the MgO crucible were shown in Supplementary Figure 8.
Figure 10. Inspection concerning consistency of as-produced ceramics. Consistency and mean/standard deviation in (A) relative densities, (B) Nyquist plots of Li0L2 dry sintered at 1,300 °C × 1 min, and (C) Li+ conductivities of Li0L2 dry pellets.
Figure 11A and B showed the Nyquist plots of the above Li0L2-dry ceramics measured at -20 to 60 °C. By linearly fitting the Arrhenius plots [Figure 11C], the activation energy calculated from the total conductivity is 0.441 eV[57]. Highly conductive LLZO ceramics in good consistency could be produced with the aid of LiZO and a dry route. As a product, Nb-LLZO SE Li0L2 delivered high consistency in high RD (~97%) and conductivity (> 8 × 10-4 S cm-1).
Figure 11. (A and B) Nyquist plots and (C) Arrhenius plot of the mass-produced Li0L2 dry ceramics at -20 to 60 °C.
Because the Nb-LLZO is unstable against lithium metal[58-60], the Li|Nb-LLZO|Li cells soon (no more than
Figure 12. Electrochemical performances (30 °C) of symmetric Li-Li and full Li-LFP cells fabricated with scalable prepared Li0L2-dry pellets sintered at 1,300 °C for 1 min. (A) Galvanostatic cycling performance of Li-Li symmetric cell, (B) segmental voltage profile of (A), (C) rate performance of Li-Li symmetric cell, (D) voltage profiles and (E) galvanostatic cycling performance of Li-LFP batteries at different rates.
CONCLUSIONS
The role of lithium-rich additive LiZO was demonstrated in densifying garnet Nb-LLZO. The LiZO decomposed at grain boundaries during sintering, generating a Li2O environment that enhanced garnet sintering and offset Li-loss. After LiZO decomposition, Li2ZrO3 in amorphous and crystalline mixed phases spread along grain boundaries and acted as a bridge to fill the adjacent grain boundaries to improve conductivity. This work developed an economical, efficient route based on solid-state reaction to synthesize LLZO SE. The solvent-free technique avoided contamination caused by solvent-adsorbed contaminants. Increased milling energy, slightly decreased sintering activity, and increased compaction density could be achieved in the dry route for LLZO powders and green pellets. These features enabled LLZO ceramics produced via a solvent-free route to be denser than those produced by a typical wet route. Combining the above in-situ Li2O compensating strategy and solvent-free dry method, grain boundaries in as-produced ceramics were strongly bonded in uniform sizes without AGG. The as-synthesized Nb-LLZO with 2 wt% LiZO additional exhibited a high room-temperature ionic conductivity of 8.39 × 10-4 S cm-1 at 25 °C, an RD of 96.8%, and high critical current densities of 0.9 mA cm-2 at 30 °C as prepared. Moreover, the ceramics produced in such a batch exhibit an exceptionally high degree of consistency. This work provided an effective production strategy for LLZO ceramics with high performance and high consistency, which promotes the development of solid-state batteries based on garnet-type ceramics.
DECLARATIONS
Authors’ contributions
Directed concentration, methodology, formal analysis, data collection, writing (original draft), and investigation: Tang J
Conducted basic characterization and data collection: Zhou Y, Li X
Managed financial support: Tang W
Contributed to conception, methodology, formal analysis, writing-review and editing: Huang X
Responsible for the laboratory platform, supervision, and writing (review and editing): Tian B
Availability of data and materials
The data supporting our findings can be found in the Supplementary Material.
Financial support and sponsorship
This work was supported by the National Natural Science Foundation of China (Grant No. 52102284) and sponsored by the Science and Technology Project of Shenzhen (JCYJ20210324094206019).
Conflicts of interest
All authors declared that there are no conflicts of interest.
Ethical approval and consent to participate
Not applicable.
Consent for publication
Not applicable.
Copyright
© The Author(s) 2024.
Supplementary Materials
REFERENCES
1. Xu L, Lu Y, Zhao C, et al. Toward the scale-up of solid-state lithium metal batteries: the gaps between lab-level cells and practical large-format batteries. Adv Energy Mater 2021;11:2002360.
2. Wang MJ, Kazyak E, Dasgupta NP, Sakamoto J. Transitioning solid-state batteries from lab to market: linking electro-chemo-mechanics with practical considerations. Joule 2021;5:1371-90.
3. Kim A, Woo S, Kang M, Park H, Kang B. Research progresses of garnet-type solid electrolytes for developing all-solid-state Li batteries. Front Chem 2020;8:468.
4. Li L, Duan H, Li J, Zhang L, Deng Y, Chen G. Toward high performance all-solid-state lithium batteries with high-voltage cathode materials: design strategies for solid electrolytes, cathode interfaces, and composite electrodes. Adv Energy Mater 2021;11:2003154.
5. Alexander GV, Indu MS, Murugan R. Review on the critical issues for the realization of all-solid-state lithium metal batteries with garnet electrolyte: interfacial chemistry, dendrite growth, and critical current densities. Ionics 2021;27:4105-26.
6. Ramakumar S, Deviannapoorani C, Dhivya L, Shankar LS, Murugan R. Lithium garnets: synthesis, structure, Li+ conductivity, Li+ dynamics and applications. Pro Mater Sci 2017;88:325-411.
7. Liang L, Sun X, Zhang J, et al. Sur-/interfacial regulation in all-solid-state rechargeable Li-ion batteries based on inorganic solid-state electrolytes: advances and perspectives. Mater Horiz 2019;6:871-910.
8. Peng L, Ren H, Zhang J, et al. LiNbO3-coated LiNi0.7Co0.1Mn0.2O2 and chlorine-rich argyrodite enabling high-performance solid-state batteries under different temperatures. Energy Stor Mater 2021;43:53-61.
9. He Z, Zhang Z, Yu M, et al. Synthetic optimization and application of Li-argyrodite Li6PS5I in solid-state battery at different temperatures. Rare Met 2022;41:798-805.
10. Huang X, Lu Y, Song Z, Xiu T, Badding ME, Wen Z. Preparation of dense Ta-LLZO/MgO composite Li-ion solid electrolyte: sintering, microstructure, performance and the role of MgO. J Energy Chem 2019;39:8-16.
11. Huang X, Su J, Song Z, et al. Synthesis of Ga-doped Li7La3Zr2O12 solid electrolyte with high Li+ ion conductivity. Ceram Int 2021;47:2123-30.
12. Iriyama Y, Wadaguchi M, Yoshida K, Yamamoto Y, Motoyama M, Yamamoto T. 5V-class bulk-type all-solid-state rechargeable lithium batteries with electrode-solid electrolyte composite electrodes prepared by aerosol deposition. J Power Sources 2018;385:55-61.
13. Huang X, Tang J, Zhou Y, et al. Developing preparation craft platform for solid electrolytes containing volatile components: experimental study of competition between lithium loss and densification in Li7La3Zr2O12. ACS Appl Mater Interfaces 2022;14:33340-54.
14. Thompson T, Yu S, Williams L, et al. Electrochemical window of the Li-ion solid electrolyte Li7La3Zr2O12. ACS Energy Lett 2017;2:462-8.
15. Ma C, Cheng Y, Yin K, et al. Interfacial stability of Li metal-solid electrolyte elucidated via in situ electron microscopy. Nano Lett 2016;16:7030-6.
16. Huang X, Xiu T, Badding ME, Wen Z. Two-step sintering strategy to prepare dense Li-Garnet electrolyte ceramics with high Li+ conductivity. Ceram Int 2018;44:5660-7.
17. Awaka J, Kijima N, Hayakawa H, Akimoto J. Synthesis and structure analysis of tetragonal Li7La3Zr2O12 with the garnet-related type structure. J Solid State Chem 2009;182:2046-52.
18. Wolfenstine J, Rangasamy E, Allen JL, Sakamoto J. High conductivity of dense tetragonal Li7La3Zr2O12. J Power Sources 2012;208:193-6.
19. Ohta S, Kobayashi T, Asaoka T. High lithium ionic conductivity in the garnet-type oxide Li7-X La3(Zr2-X, NbX)O12 (X=0-2). J Power Sources 2011;196:3342-5.
20. Li Y, Wang C, Xie H, Cheng J, Goodenough JB. High lithium ion conduction in garnet-type Li6La3ZrTaO12. Electrochem Commun 2011;13:1289-92.
21. Allen J, Wolfenstine J, Rangasamy E, Sakamoto J. Effect of substitution (Ta, Al, Ga) on the conductivity of Li7La3Zr2O12. J Power Sources 2012;206:315-9.
22. Kotobuki M, Kanamura K, Sato Y, Yoshida T. Fabrication of all-solid-state lithium battery with lithium metal anode using Al2O3-added Li7La3Zr2O12 solid electrolyte. J Power Sources 2011;196:7750-4.
23. Huang X, Lu Y, Song Z, et al. Manipulating Li2O atmosphere for sintering dense Li7La3Zr2O12 solid electrolyte. Energy Stor Mater 2019;22:207-17.
24. Huang X, Lu Y, Guo H, et al. None-mother-powder method to prepare dense Li-garnet solid electrolytes with high critical current density. ACS Appl Energy Mater 2018;1:5355-65.
25. Nguyen MH, Park S. Synergetic effect of Li-ion concentration and triple doping on ionic conductivity of Li7La3Zr2O12 solid electrolyte. Nanomaterials 2022;12:2946.
26. Zhou Y, Li X, Yang Y, Huang X, Tian B. Production of Ta-doped Li7La3Zr2O12 solid electrolyte with high critical current density. ACS Appl Energy Mater 2022;5:13817-28.
27. Huang X, Lu Y, Niu Y, et al. From protonation & Li-rich contamination to grain-boundary segregation: evaluations of solvent-free vs. wet routes on preparing Li7La3Zr2O12 solid electrolyte. J Energy Chem 2022;73:223-39.
28. Smetaczek S, Limbeck A, Zeller V, et al. Li+/H+ exchange of Li7La3Zr2O12 single and polycrystals investigated by quantitative LIBS depth profiling. Mater Adv 2022;3:8760-70.
29. Arinicheva Y, Guo X, Gerhards M, et al. Competing effects in the hydration mechanism of a garnet-type Li7La3Zr2O12 electrolyte. Chem Mater 2022;34:1473-80.
30. Nie K, Wu S, Wang J, et al. Reaction mechanisms of Ta-substituted cubic Li7La3Zr2O12 with solvents during storage. ACS Appl Mater Interfaces 2021;13:38384-93.
31. Gupta A, Kazyak E, Dasgupta NP, Sakamoto J. Electrochemical and surface chemistry analysis of lithium lanthanum zirconium tantalum oxide (LLZTO)/liquid electrolyte (LE) interfaces. J Power Sources 2020;474:228598.
32. Wood M, Gao X, Shi R, et al. Exploring the relationship between solvent-assisted ball milling, particle size, and sintering temperature in garnet-type solid electrolytes. J Power Sources 2021;484:229252.
33. Zheng H, Li G, Liu J, et al. A rational design of garnet-type Li7La3Zr2O12 with ultrahigh moisture stability. Energy Stor Mater 2022;49:278-90.
34. Zheng H, Li G, Liu H, Wu Y, Duan H. Influence of dry- and wet-milled LLZTO particles on the sintered pellets. J Am Ceram Soc 2023;106:274-84.
35. Huang X, Song Z, Xiu T, Badding ME, Wen Z. Searching for low-cost LixMOy compounds for compensating Li-loss in sintering of Li-Garnet solid electrolyte. J Materiomics 2019;5:221-8.
36. Murugan R, Thangadurai V, Weppner W. Fast lithium ion conduction in garnet-type Li7La3Zr2O12. Angew Chem Int 2007;46:7778-81.
37. Zheng C, Ruan Y, Su J, et al. Grain boundary modification in garnet electrolyte to suppress lithium dendrite growth. Chem Eng J 2021;411:128508.
38. Zheng C, Lu Y, Su J, et al. Grain boundary engineering enabled high-performance garnet-type electrolyte for lithium dendrite free lithium metal batteries. Small Methods 2022;6:e2200667.
39. Kataoka K, Akimoto J. Large single-crystal growth of tetragonal garnet-type Li7La3Zr2O12 by melting method. Solid State Ionics 2020;349:115312.
40. Kataoka K. Oxide single crystals with high lithium-ion conductivity as solid electrolytes for all-solid-state lithium secondary battery applications. J Ceram Soc Japan 2020;128:7-18.
41. Kudo H, Wu C, Ihle H. Mass-spectrometric study of the vaporization of Li2Os and thermochemistry of gaseous LiO, Li2O, Li3O, and Li2O2. J Nucl Mater 1978;78:380-9.
42. Li Y, Han JT, Wang CA, Xie H, Goodenough JB. Optimizing Li+ conductivity in a garnet framework. J Mater Chem 2012;22:15357-61.
43. Larraz G, Orera A, Sanjuán ML. Cubic phases of garnet-type Li7La3Zr2O12: the role of hydration. J Mater Chem A 2013;1:11419-28.
44. Huang X, Song Z, Xiu T, Badding ME, Wen Z. Sintering, micro-structure and Li+ conductivity of Li7-La3Zr2-NbO12/MgO
45. Cai J, Polzin B, Fan L, et al. Stoichiometric irreversibility of aged garnet electrolytes. Mater Today Energy 2021;20:100669.
46. Liu C, Rui K, Shen C, Badding ME, Zhang G, Wen Z. Reversible ion exchange and structural stability of garnet-type Nb-doped
47. Pfeiffer H, Bosch P. Thermal stability and high-temperature carbon dioxide sorption on hexa-lithium zirconate (Li6Zr2O7). Chem Mater 2005;17:1704-10.
48. Baral AK, Narayanan S, Ramezanipour F, Thangadurai V. Evaluation of fundamental transport properties of Li-excess garnet-type Li5+2xLa3Ta2-xYxO12 (x = 0.25, 0.5 and 0.75) electrolytes using AC impedance and dielectric spectroscopy. Phys Chem Chem Phys 2014;16:11356-65.
49. Samsinger RF, Letz M, Schuhmacher J, et al. Fast ion conduction of sintered glass-ceramic lithium ion conductors investigated by impedance spectroscopy and coaxial reflection technique. J Electrochem Soc 2020;167:140510.
50. Dion F, Lasia A. The use of regularization methods in the deconvolution of underlying distributions in electrochemical processes. J Electroanal Chem 1999;475:28-37.
51. Zhang Y, Chen Y, Yan M, Chen F. Reconstruction of relaxation time distribution from linear electrochemical impedance spectroscopy. J Power Sources 2015;283:464-77.
52. Cheng L, Crumlin EJ, Chen W, et al. The origin of high electrolyte-electrode interfacial resistances in lithium cells containing garnet type solid electrolytes. Phys Chem Chem Phys 2014;16:18294-300.
53. Jones JC, Rajendran S, Pilli A, et al. In situ x-ray photoelectron spectroscopy study of lithium carbonate removal from garnet-type solid-state electrolyte using ultra high vacuum techniques. J Vac Sci Technol A 2020;38:023201.
54. Han F, Zhu Y, He X, Mo Y, Wang C. Electrochemical stability of Li10GeP2S12 and Li7La3Zr2O12 solid electrolytes. Adv Energy Mater 2016;6:1501590.
55. Yuan K, Jin X, Xu C, et al. Fabrication of dense and porous Li2ZrO3 nanofibers with electrospinning method. Appl Phys A 2018;124:403.
56. Huang Y, Chen J, Ni J, Zhou H, Zhang X. A modified ZrO2-coating process to improve electrochemical performance of
57. Tenhaeff WE, Rangasamy E, Wang Y, et al. Resolving the grain boundary and lattice impedance of hot-pressed Li7La3Zr2O12 garnet electrolytes. ChemElectroChem 2014;1:375-8.
58. Kim Y, Yoo A, Schmidt R, et al. Electrochemical stability of Li6.5La3Zr1.5M0.5O12 (M = Nb or Ta) against Metallic Lithium. Front Energy Res 2016;4:20.
59. Tang J, Niu Y, Zhou Y, et al. H3PO4-induced Nano-Li3PO4 pre-reduction layer to address instability between the Nb-Doped Li7La3Zr2O12 electrolyte and metallic Li anode. ACS Appl Mater Interfaces 2023;15:5345-56.
Cite This Article
Export citation file: BibTeX | RIS
OAE Style
Tang J, Zhou Y, Li X, Huang X, Tang W, Tian B. In-situ Li2O-atmosphere assisted solvent-free route to produce highly conductive Li7La3Zr2O12 solid electrolyte. Energy Mater 2024;4:400022. http://dx.doi.org/10.20517/energymater.2023.87
AMA Style
Tang J, Zhou Y, Li X, Huang X, Tang W, Tian B. In-situ Li2O-atmosphere assisted solvent-free route to produce highly conductive Li7La3Zr2O12 solid electrolyte. Energy Materials. 2024; 4(2): 400022. http://dx.doi.org/10.20517/energymater.2023.87
Chicago/Turabian Style
Tang, Jiawen, Yongjian Zhou, Xiaoyi Li, Xiao Huang, Wei Tang, Bingbing Tian. 2024. "In-situ Li2O-atmosphere assisted solvent-free route to produce highly conductive Li7La3Zr2O12 solid electrolyte" Energy Materials. 4, no.2: 400022. http://dx.doi.org/10.20517/energymater.2023.87
ACS Style
Tang, J.; Zhou Y.; Li X.; Huang X.; Tang W.; Tian B. In-situ Li2O-atmosphere assisted solvent-free route to produce highly conductive Li7La3Zr2O12 solid electrolyte. Energy Mater. 2024, 4, 400022. http://dx.doi.org/10.20517/energymater.2023.87
About This Article
Copyright
Data & Comments
Data
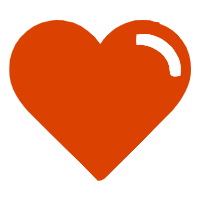

Comments
Comments must be written in English. Spam, offensive content, impersonation, and private information will not be permitted. If any comment is reported and identified as inappropriate content by OAE staff, the comment will be removed without notice. If you have any queries or need any help, please contact us at support@oaepublish.com.