Revealing the dynamic formation mechanism of porous Mo2C: an in-situ TEM study
Abstract
In-situ transmission electron microscopy (TEM) enables direct observation of the micromorphology and microstructure evolution of catalysts in the chemical atmosphere. Studying the structural evolution during the formation of molybdenum carbide using in-situ TEM is helpful for the preparation of high-performance carbide catalysts. Herein, the formation mechanism of porous Mo2C from MoO2 nanoparticles (NPs) was studied by in-situ TEM. The formation of Mo2C was induced by the defects of MoO2, and the formed Mo2C facilitated the carbonization of neighboring MoO2 NPs. The growth rate of Mo2C between MoO2 NPs was slower compared to that within a single MoO2 NP. In addition, the formation and growth of pores in Mo2C were also studied; the pores grew radially during the early stages from the nucleation sites and later grew branched and curved. As Mo2C underwent competitive growth, the pores transitioned from straight to curved. Eventually, during prolonged carbonization at high temperatures, Mo2C underwent sintering.
Keywords
INTRODUCTION
The transition metal carbides are widely used in industry due to their unique physical and chemical properties[1-7]. For instance, molybdenum (Mo) carbides can serve as supports in solid catalysts, which exhibit good performances in heterogeneous catalysis[8-10]. Moreover, Mo carbides also are the active phases, owning similar catalytic properties with the precious metals because of the introduction of carbon atoms[11-18]. They have been applied in hydrogenation[19-23], steam reforming of methanol[24], and water gas shift reaction[25]. Among them, β-Mo2C demonstrated excellent activity and selectivity in CO2 reduction[26], hydrogen production[27], and hydrodeoxygenation reactions[28]. Therefore, the research and development of preparation technology plays an important role in the application of high-performance Mo carbide catalysts. At present, the main preparation methods of Mo carbides include solid-solid and solid-gas (temperature-programmed reduction) reaction methods[29]. The solid-gas approach, which employs the reaction of the Mo oxides and the carbon-containing gases (e.g., CO, CH4, C2H6, and aromatic compounds), was developed rapidly[30-36]. It is crucial to investigate the structural transformation process of Mo oxides into Mo carbides during temperature-programmed reduction carbonization.
Along with the development of preparation technologies for Mo carbides, the carbonization mechanism of Mo oxides to Mo carbides has also been studied intensively[37-39]. The carburization of MoO3 with hydrocarbon and hydrogen was studied by the photoelectron spectroscopy[40]. The carbon deposition on the sample surface decreased with increasing carbon content. It indicated the diffusion of surface carbon on the sample into a bulk phase in the carburization process of Mo oxides. The MoO2 was the intermediate phase determined by thermodynamic analysis in the process of MoO3 transformed into Mo2C[41]. Based on this, the structural evolution processes of MoO2 in different carbon-containing gas atmospheres were investigated systematically. For example, the reduction of MoO2 powders with CO to produce Mo2C was studied, and the reduction mechanisms were significantly distinct at different temperatures[42]. The MoO2 followed a one-step reaction translated to Mo2C at lower temperatures. However, the transition process was different at high temperatures; the MoO2 was reduced to Mo first, and then the Mo was carburized to Mo2C. The transformation of MoO2 to Mo2C in a hydrocarbon atmosphere was also focused. The MoOxCy as the intermediate phases were observed during the carburization of MoO2 in CH4/H2 or C2H6/H2[43]. In addition, the mechanism of MoO2 to Mo2C under methane pulse conditions was also studied[44]. The researchers proposed the “plum-pudding” model in the solid-phase transformation from MoO2 to Mo2C. However, due to the limitation of characterization techniques, there are no relevant reports on the study of direct observation regarding Mo2C formation processes in the preparation by temperature-programmed reduction methods. It seriously affects the perception and regulation of Mo2C preparation. Usually, the direct reaction of Mo oxides with a carbon source at elevated temperatures generates β-Mo2C. The investigation of their structural formation mechanism could provide guidance for the controllable preparation and also benefit the synthesis of Mo2C with other phase structures.
In-situ transmission electron microscopy (TEM) has been used to directly visualize the structural evolution of nano-catalysts[45-47]. In recent years, the deoxidation process of MoO3 was studied by environmental TEM, accompanied by the nanoparticles (NPs) crushing and regrowth in H2 and thermal field, and the MoO3 has a good directional deoxidation process[48]. Meanwhile, the different solid carbon sources were used, and the controllable growth of Mo carbides was monitored by in-situ TEM[49]. The face centered cubic (FCC) MoC with full occupation of interstitial sites by carbon sites was formed because the sucrose was decomposed into high reactivity sp3 carbon atoms. The three-stage mechanism during nucleation and growth of Mo2C NPs was also revealed by in-situ TEM[50]. Furthermore, if an atmosphere is introduced into TEM, the formation process of Mo carbides in the carbonation atmosphere can be directly observed. This helps to understand the mechanism of synthesizing Mo carbides by the solid-gas reaction method.
Herein, to get a better understanding of the formation mechanism of Mo oxides to Mo carbides in a temperature-programmed reduction method, we studied the microstructural evolutions of MoO2 NPs to porous Mo2C in a mixed atmosphere of methane and hydrogen by using in-situ TEM. And the mechanism of gas-solid reaction in the formation of Mo2C was analyzed in detail.
EXPERIMENTAL
Synthesis of MoO3 nanobelts
The typical solvothermal method applied to synthesize the MoO3 nanobelts has been reported previously[51]. In brief, the 4,839 mg (0.02 mol) sodium molybdate dihydrate was dissolved in 60 mL deionized water after the 4 mL nitric acid was diluted by 16 mL deionized water and added to the stirred solution dropwise. Then, the solution was transferred into a 100 mL autoclave, sealed, and maintained at 130 °C for 12 h in an oven. Finally, the obtained deposition was filtered and washed with deionized water and then calcinated at 300 °C in air for 2 h. The MoO2 was prepared by reducing MoO3 nanobelts in H2 or CH4/H2 atmosphere at 500 °C for 2 h with a heating rate of 10 °C/min. Mo2C was synthesized under a CH4/H2 atmosphere at 700 °C for
Samples characterization
TEM and high-angle annular dark field scanning TEM (HAADF-STEM) images were obtained using FEI Tecnai G2 F20 operated at 200 kV. Scanning electron microscopy (SEM) images were obtained using Regulus 8100 operated at 3 kV. X-ray diffraction (XRD) measurements were performed on a Rigaku D/max 2400 diffractometer (Cu Kα radiation, λ = 0.15418 nm) operating at 40 kV and 40 mA. X-ray photoelectron spectroscopy (XPS) characterization was carried out with an ESCALAB 250 instrument with Al Kα X-rays (1,489.6 eV, 150 W, 50.0 eV pass energy). N2 adsorption-desorption isotherms were measured on an ASAP 2020 micromeritics apparatus, and the specific surface areas of the samples were calculated following the multi-point BET (Brunauer-Emmett-Teller) procedure. The pore-size distributions were determined from the adsorption branch of the isotherms using the BJH (Barett-Joyner-Halenda) model.
CH4/H2 temperature programmed surface reaction (TPSR)
The 40 mg MoO3 nanobelts were loaded in a quartz tube reactor that was connected to a mass spectrometer. Following, the samples were elevated to 700 °C with a heating rate of 5 °C/min under 20 vol.% CH4/H2 flow (5 mL/min). The mass signals of H2 (Mz = 2) and H2O (Mz = 18) were monitored during the process.
In-situ TEM investigation
The commercial gas-heating holder (produced by DENSsolutions), a home-made gas controlling system, and the Titan Themis G3 ETEM were adopted during the in-situ TEM experiments. The MoO3 sample was encapsulated in a nanoreactor of a gas-heating holder. The nanoreactor has two amorphous SiNx windows in order to observe the structural evolution of MoO3 catalysts. The sample was calcinated at 300 °C in
RESULTS AND DISCUSSION
Characterization of the Mo oxides (carbides)
The typical XRD patterns and TEM images of MoO3 nanobelts after calcination are shown in Supplementary Figure 1. The XRD pattern [Supplementary Figure 1A] confirmed the MoO3 phase structure (JCPDS 65-2421) for MoO3 nanobelts calcinated at 300 °C, and the sharp diffraction peaks verified the high crystallinity. High-resolution TEM (HRTEM) with local fast Fourier transform (FFT) observation also identified the crystallographic property of MoO3. The interplanar distances of 0.380 nm and 0.369 nm with an intersection angle of 90° were assigned to the (101) and (010) planes [Supplementary Figure 1C]. The sharp, bright diffraction spots are displayed in FFT [Supplementary Figure 1D], illustrating the high crystallinity of MoO3 nanobelts, too. The temperature programmed surface reaction (TPSR) experiments show that the content change curves of H2 and H2O when MoO3 nanobelts were reduced and carbonized
The STEM images and energy-dispersive X-ray spectroscopy (EDX) elemental maps of MoO2 and Mo2C samples were displayed in Supplementary Figure 4, exhibiting the well-distributed Mo/O in MoO2 [Supplementary Figure 4A-C] and Mo/C in Mo2C
Observation regarding the formation of porous Mo2C
In order to understand the formation mechanism of Mo2C, we observed the micromorphological and microstructural evolution of MoO2 to Mo2C at the nanoscale using in-situ TEM. Figure 1 exhibits the carbonization process of MoO2 to Mo2C under the 20 vol.% CH4/H2 atmosphere at ambient pressure. Figure 1A shows that the samples were MoO2 NPs under the CH4/H2 atmosphere at 600 °C. The average particle size of MoO2 NPs was 62.8 nm [Supplementary Figure 7]. When the temperature increased to
Figure 1. In-situ transformation from MoO2 to Mo2C. (A-D) In-situ TEM images of the Mo2C formation from MoO2 in 20 vol.% CH4/H2 atmosphere; (E) The corresponding SAED patterns of MoO2 (A) and Mo2C (D); (F) Intensity profiles from the integration of diffraction rings of SAED patterns in E (a.u., arbitrary units); (G) Unit cells of MoO2 and Mo2C; (H) The histogram of cell volume and volume per Mo of MoO2 and Mo2C. Mo: Molybdenum; SAED: selected area electron diffraction; TEM: transmission electron microscopy.
Unraveling the nucleation and growth of porous Mo2C
Figure 2 displays the Mo2C nucleation process of MoO2 NPs under the drive of CH4 and H2 at 700 °C. Previous studies have illustrated that the methane was cracked into carbon with high reactivity at high temperatures, and the carbon species adsorbed on the surface of metal oxides[52,53]. In this experiment, the MoO2 and highly reactive carbon further reacted and formed the Mo carbides. It is noteworthy that the defects in MoO2 NPs were more likely to be carbonized preferentially. The preferential nucleation of Mo2C was located at the defects of MoO2 NPs. Figure 2F showed many small nanocrystals gradually appearing and the generation of pores at the defects of MoO2 NPs, suggesting that the Mo2C sites were formed here. Following, Mo2C grew radially from the nucleation site in all directions at MoO2 NPs [Figure 2H-J]. It proved that the defects in MoO2 NPs induced the nucleation of Mo2C. In addition, the carbonization process of two adjacent MoO2 NPs was observed at 700 °C in the CH4/H2 atmosphere [Supplementary Figures 8 and 9]. Under the co-drive of CH4 and H2, the defects in MoO2 NPs were carbonized first, and the NP transformed into porous Mo2C. Subsequently, the carbonized MoO2 NP induced the carbonization of adjacent MoO2 NPs at the interface between two NPs. The carbonization reaction crossed the interface between two NPs and continued in the next MoO2 NP. Lastly, the two MoO2 NPs were turned to porous Mo2C, and the grain boundary of the two NPs disappeared. It further reveals that the carbonization of MoO2 NPs was also promoted by the adjacent already carbonized porous Mo2C as the nucleating agents.
Figure 2. Defect-induced nucleation of Mo2C. (A-E) In-situ TEM images of the nucleation process of Mo2C under 20 vol.% CH4/H2 atmosphere at 700 °C; (F-J) Enlarged TEM images acquired from the dashed boxes in (A) to (E). TEM: Transmission electron microscopy.
Generally, the MoO2 NPs obtained by the reduction of MoO3 nanobelts were usually stacked[54]. Herein, the growth rate of Mo2C within and between MoO2 NPs was studied [Figure 3]. There are approximately nine MoO2 NPs stacked together in the observed two-dimensional (2D) region in Figure 3A. Figure 3K shows the growth rate of 2D area of porous Mo2C in Supplementary Figure 10. The carbonization rate of MoO2 NPs was represented by the growth rate of 2D area of porous Mo2C. When Mo2C grows across the interface between two MoO2 NPs, it is considered to be carbonized between MoO2 NPs. Alternately, when Mo2C only grows inside MoO2 NPs, it is carbonized within MoO2 NPs. Judging from TEM images at 5 s, 10 s, and 15 s
Figure 3. Growth rate of Mo2C within and between MoO2 NPs. (A-J) In-situ TEM images of structural evolution from stacked MoO2 NPs to Mo2C under 20 vol.% CH4/H2 atmosphere at 700 °C; (K) The carbonization rates within and between MoO2 NPs. The boxes represent the growth rate of two-dimensional area of porous Mo2C. Blue numbers represent the number of interfaces with Mo2C growth crossing between MoO2 NPs, and the capital letters represent the corresponding TEM images in (B-J). NPs: Nanoparticles; TEM: transmission electron microscopy.
Revealing the pore formation and evolution of porous Mo2C
Subsequently, the formation of pores in the growth of Mo2C was observed in Figure 4. The three types of porous Mo2C growth were summarized. At the early stage, the pores showed radial growth from the center to the periphery [Figure 4A-E]. The structural transition from MoO2 to Mo2C was accompanied by the formation of straighter pores and faster pore growth rates. The competitive growth of pores was observed when two Mo2C nucleation sites met during the carbonization process. As shown in Figure 4F-J, the straighter pores became distorted, and the growth rate of pores was slowed down during this process. In addition, the tip splitting and side branches of pores were observed in the late stage of growth. The growth of porous Mo2C slowed down, and the pores curved due to the reduction of Mo sources [Figure 4K-O]. The above observations revealed that the growth and evolution of pores were affected by the amount of Mo sources. The pores of the Mo2C radial grew and formed straighter pores when the Mo sources were sufficient. On the contrary, the pores of Mo2C became curved and branched when the Mo sources were reduced.
Analyzing the microstructure of porous Mo2C
Lastly, the micromorphology and structure of porous Mo2C obtained by MoO2 carbonization were analyzed, as shown in Figure 5. Figure 5B demonstrates the porous Mo2C with different orientations of nanocrystals; the (101) facets with a lattice spacing of 2.29 Å were observed. The measured planes with lattice spacings of 2.61 Å, 2.29 Å, and 2.29 Å and angles of 64° and 52° in Figure 5C correspond to the crystal parameters of (010) 2.61 Å, (101) 2.29 Å and (1-11) 2.29 Å in hexagonal Mo2C structures (JCPDS 35-0787). FFT pattern [Figure 5C] shows the hexagonal Mo2C structure from the [-101] zone axis [Figure 5D]. The micromorphology and pore size of Mo2C nanocrystal were computed in Supplementary Figure 12. The mean pore width and length are 1.4 nm and 9.7 nm, respectively. In addition, the N2 physisorption tests
CONCLUSIONS
The structure evolution process of MoO2 to porous Mo2C in a carbonizing atmosphere was systemically investigated by using in-situ TEM. The formation of porous structures was observed during the carbonization process, which could be attributed to the volume decrease when an equivalent of Mo in the form of MoO2 is converted to Mo2C. The defects in MoO2 NPs facilitated the nucleation of Mo2C under
DECLARATIONS
Authors’ contributionsDesign of the study and writing of the manuscript for the whole work: Wang Y, Niu Y, Zhang B
Performed the TEM characterization: Wang Y, Niu Y, Li S, Liu Y
Performed the analysis of data: Wang Y, Niu Y, Pu Y
Performed data acquisition and provided administrative, technical, and material support: Wang Y, Niu Y, Zhang B
Availability of data and materialsNot applicable.
Financial support and sponsorshipThis work was supported by the National Natural Science Foundation of China (Nos. 22072164, 22002173, 52161145403), the China Postdoctoral Science Foundation (2020M680999), the Natural Science Foundation of Liaoning Province (2022-MS-004), and the foundations of Shenyang National Laboratory for Materials Science.
Conflicts of interestAll authors declared that there are no conflicts of interest.
Ethical approval and consent to participateNot applicable.
Consent for publicationNot applicable.
Copyright© The Author(s) 2023.
REFERENCES
1. Lin Z, Denny SR, Chen JG. Transition metal carbides and nitrides as catalysts for thermochemical reactions. J Catal 2021;404:929-42.
2. Li J, Chen X, Zhu X, Jiang Y, Chang X, Sun S. Two-dimensional transition metal MXene-based gas sensors: a review. Chin Chem Lett 2023:108286.
3. Oyama S. Preparation and catalytic properties of transition metal carbides and nitrides. Catal Today 1992;15:179-200.
4. Pang J, Sun J, Zheng M, Li H, Wang Y, Zhang T. Transition metal carbide catalysts for biomass conversion: a review. Appl Catal B Environ 2019;254:510-22.
5. Dong S, Pu Y, Niu Y, Zhang L, Wang Y, Zhang B. Interstitial carbon in Ni enables high-efficiency hydrogenation of 1,3-butadiene. Acta Phys Chim Sin 2023;39:2301012.
6. He K, Shen R, Hao L, et al. Advances in nanostructured silicon carbide photocatalysts. Acta Phys Chim Sin 2022;38:2201021.
7. Du X, Zhang R, Li D, Hu C, Garcia H. Molybdenum carbide as catalyst in biomass derivatives conversion. J Energy Chem 2022;73:68-87.
8. Yao S, Zhang X, Zhou W, et al. Atomic-layered Au clusters on α-MoC as catalysts for the low-temperature water-gas shift reaction. Science 2017;357:389-93.
9. Dong J, Fu Q, Jiang Z, Mei B, Bao X. Carbide-supported Au catalysts for water-gas shift reactions: a new territory for the strong metal-support interaction effect. J Am Chem Soc 2018;140:13808-16.
10. Lin L, Zhou W, Gao R, et al. Low-temperature hydrogen production from water and methanol using Pt/α-MoC catalysts. Nature 2017;544:80-3.
11. Ma Y, Guan G, Hao X, Cao J, Abudula A. Molybdenum carbide as alternative catalyst for hydrogen production - a review. Renew Sust Energ Rev 2017;75:1101-29.
12. Hou R, Chang K, Chen JG, Wang T. Replacing precious metals with carbide catalysts for hydrogenation reactions. Top Catal 2015;58:240-6.
13. Frühberger B, Chen JG. Reaction of ethylene with clean and carbide-modified Mo(110): converting surface reactivities of molybdenum to Pt-group metals. J Am Chem Soc 1996;118:11599-609.
14. Shi Y, Yang Y, Li Y, Jiao H. Activation mechanisms of H2, O2, H2O, CO2, CO, CH4 and C2Hx on metallic Mo2C(001) as well as Mo/C terminated Mo2C(101) from density functional theory computations. Appl Catal A Gen 2016;524:223-36.
15. Du X, Liu J, Li D, et al. Structural and electronic effects boosting Ni-doped Mo2C catalyst toward high-efficiency C-O/C-C bonds cleavage. J Energ Chem 2022;75:109-16.
16. Wan C, Regmi YN, Leonard BM. Multiple phases of molybdenum carbide as electrocatalysts for the hydrogen evolution reaction. Angew Chem Int Ed Engl 2014;53:6407-10.
17. Lian JH, Tan HY, Guo CQ, et al. Unravelling the role of ceria in improving the stability of Mo2C- based catalysts for the steam reforming of dimethyl ether. Catal Sci Technol 2021;11:5570-8.
18. Guo X, Wang C, Wang W, et al. Vacancy manipulating of molybdenum carbide MXenes to enhance Faraday reaction for high performance lithium-ion batteries. Nano Res Energy 2022;1:e9120026.
19. Yang Q, Qiu R, Ma X, Hou R, Sun K. Surface reconstruction and the effect of Ni-modification on the selective hydrogenation of 1,3-butadiene over Mo2C-based catalysts. Catal Sci Technol 2020;10:3670-80.
20. Yue S, Xu D, Sheng Y, et al. One-step synthesis of mesoporous alumina-supported molybdenum carbide with enhanced activity for thiophene hydrodesulfurization. J Environ Chem Eng 2021;9:105693.
21. Dongil AB, Zhang Q, Pastor-pérez L, Ramírez-reina T, Guerrero-ruiz A, Rodríguez-ramos I. Effect of Cu and Cs in the β-Mo2C system for CO2 hydrogenation to methanol. Catalysts 2020;10:1213.
22. Rocha AS, Souza LA, Oliveira Jr RR, Rocha AB, da Silva VT. Hydrodeoxygenation of acrylic acid using Mo2C/Al2O3. Appl Catal A Gen 2017;531:69-78.
23. Ye X, Ma J, Yu W, et al. Construction of bifunctional single-atom catalysts on the optimized β-Mo2C surface for highly selective hydrogenation of CO2 into ethanol. J Energy Chem 2022;67:184-92.
24. Cao J, Ma Y, Guan G, et al. Reaction intermediate species during the steam reforming of methanol over metal modified molybdenum carbide catalysts. Appl Catal B Environ 2016;189:12-8.
25. Wang G, Schaidle JA, Katz MB, Li Y, Pan X, Thompson LT. Alumina supported Pt-Mo2C catalysts for the water-gas shift reaction. J Catal 2013;304:92-9.
26. Zhang X, Liu Y, Zhang M, et al. Synergy between β-Mo2C nanorods and non-thermal plasma for selective CO2 reduction to CO. Chem 2020;6:3312-28.
27. Ma FX, Wu HB, Xia BY, Xu CY, Lou XW. Hierarchical β-Mo2C nanotubes organized by ultrathin nanosheets as a highly efficient electrocatalyst for hydrogen production. Angew Chem Int Ed 2015;54:15395-9.
28. Murugappan K, Anderson EM, Teschner D, Jones TE, Skorupska K, Román-leshkov Y. Operando NAP-XPS unveils differences in MoO3 and Mo2C during hydrodeoxygenation. Nat Catal 2018;1:960-7.
29. Vitale G, Guzmán H, Frauwallner ML, Scott CE, Pereira-almao P. Synthesis of nanocrystalline molybdenum carbide materials and their characterization. Catal Today 2015;250:123-33.
30. Vitale G, Frauwallner M, Hernandez E, Scott C, Pereira-almao P. Low temperature synthesis of cubic molybdenum carbide catalysts via pressure induced crystallographic orientation of MoO3 precursor. Appl Catal A Gen 2011;400:221-9.
31. Chang H, Zhang G, Chou K. Topochemical synthesis of one-dimensional Mo2C nanobelts. Ceram Int 2020;46:12891-6.
32. Wang L, Zhang G, Chou K. Preparation of Mo2C by reducing ultrafine spherical β-MoO3 powders with CO or CO-CO2 gases. J Aust Ceram Soc 2018;54:97-107.
33. Li S, Kim WB, Lee JS. Effect of the reactive gas on the solid-state transformation of molybdenum trioxide to carbides and nitrides. Chem Mater 1998;10:1853-62.
34. Xiao T, York APE, Coleman KS, et al. Effect of carburising agent on the structure of molybdenum carbides. J Mater Chem 2001;11:3094-8.
35. Kugler EL, Clark CH, Wright JH, et al. Preparation, interconversion and characterization of nanometer-sized molybdenum carbide catalysts. Top Catal 2006;39:257-62.
36. Jung KT, Kim WB, Rhee CH, Lee JS. Effects of transition metal addition on the solid-state transformation of molybdenum trioxide to molybdenum carbides. Chem Mater 2004;16:307-14.
37. Alaba PA, Abbas A, Huang J, Daud WMAW. Molybdenum carbide nanoparticle: understanding the surface properties and reaction mechanism for energy production towards a sustainable future. Renew Sust Energ Rev 2018;91:287-300.
38. Wang W, Han Y, Li Z, Liu X, Xu S. Phase equilibrium diagram and phase transformation for preparation of Mo2C: thermodynamic study and experimental verification. Ceram Int 2020;46:755-62.
39. Zhu L, Zhao Y, Yang W, Hsu H, Peng P, Li F. Low-temperature selective synthesis of metastable α-MoC with electrochemical properties: electrochemical co-reduction of CO2 and MoO3 in molten salts. Chinese Chem Lett 2023:108583.
40. Koós Á, Oszkó A, Solymosi F. A photoelectron spectroscopic study of the carburization of MoO3. Appl Surf Sci 2007;253:3022-8.
41. Cetinkaya S, Eroglu S. Thermodynamic analysis and synthesis of porous Mo2C sponge by vapor-phase condensation and in situ carburization of MoO3. J Alloys Compd 2010;489:36-41.
42. Dang J, Zhang G, Wang L, Chou K, Pistorius PC. Study on reduction of MoO2 powders with CO to produce Mo2C. J Am Ceram Soc 2016;99:819-24.
43. Hanif A, Xiao T, York APE, Sloan J, Green MLH. Study on the structure and formation mechanism of molybdenum carbides. Chem Mater 2002;14:1009-15.
44. Bkour Q, Cuba-torres CM, Marin-flores OG, et al. Mechanistic study of the reduction of MoO2 to Mo2C under methane pulse conditions. J Mater Sci 2018;53:12816-27.
45. Wang Y, Niu Y, Gao T, Liu S, Zhang B. Assessing the effect of the electron-beam irradiation on Pd/Ga2O3 catalyst under ambient pressure. ChemCatChem 2020;12:4765-9.
46. Niu Y, Liu X, Wang Y, et al. Visualizing formation of intermetallic PdZn in a palladium/zinc oxide catalyst: interfacial fertilization by PdHx. Angew Chem Int Ed Engl 2019;58:4232-7.
47. Li C, Liu B, Jiang N, Ding Y. Elucidating the charge-transfer and Li-ion-migration mechanisms in commercial lithium-ion batteries with advanced electron microscopy. Nano Res Energy 2022;1:e9120031.
48. Ma P, Li A, Wang L, Zheng K. Investigation of deoxidation process of MoO3 using environmental TEM. Materials 2021;15:56.
49. Lin Z, Cai L, Lu W, Chai Y. Phase and facet control of molybdenum carbide nanosheet observed by in situ TEM. Small 2017;13:1700051.
50. Fei L, Ng SM, Lu W, et al. Atomic-scale mechanism on nucleation and growth of Mo2C nanoparticles revealed by in situ transmission electron microscopy. Nano Lett 2016;16:7875-81.
51. Yang S, Wang Z, Hu Y, et al. Highly responsive room-temperature hydrogen sensing of α-MoO3 nanoribbon membranes. ACS Appl Mater Interfaces 2015;7:9247-53.
52. Bonnet F, Ropital F, Berthier Y, Marcus P. Filamentous carbon formation caused by catalytic metal particles from iron oxide. Mater Corros 2003;54:870-80.
53. Zou Z, Fu L, Song X, Zhang Y, Liu Z. Carbide-forming groups IVB-VIB metals: a new territory in the periodic table for CVD growth of graphene. Nano Lett 2014;14:3832-9.
54. Hu B, Mai L, Chen W, Yang F. From MoO3 nanobelts to MoO2 nanorods: structure transformation and electrical transport. ACS Nano 2009;3:478-82.
55. Guo X, Maier J. Grain boundary blocking effect in zirconia: a schottky barrier analysis. J Electrochem Soc 2001;148:E121.
Cite This Article
Export citation file: BibTeX | RIS
OAE Style
Wang Y, Niu Y, Pu Y, Li S, Liu Y, Zhang B. Revealing the dynamic formation mechanism of porous Mo2C: an in-situ TEM study. Chem Synth 2023;3:42. http://dx.doi.org/10.20517/cs.2023.33
AMA Style
Wang Y, Niu Y, Pu Y, Li S, Liu Y, Zhang B. Revealing the dynamic formation mechanism of porous Mo2C: an in-situ TEM study. Chemical Synthesis. 2023; 3(4): 42. http://dx.doi.org/10.20517/cs.2023.33
Chicago/Turabian Style
Wang, Yongzhao, Yiming Niu, Yinghui Pu, Shiyan Li, Yuefeng Liu, Bingsen Zhang. 2023. "Revealing the dynamic formation mechanism of porous Mo2C: an in-situ TEM study" Chemical Synthesis. 3, no.4: 42. http://dx.doi.org/10.20517/cs.2023.33
ACS Style
Wang, Y.; Niu Y.; Pu Y.; Li S.; Liu Y.; Zhang B. Revealing the dynamic formation mechanism of porous Mo2C: an in-situ TEM study. Chem. Synth. 2023, 3, 42. http://dx.doi.org/10.20517/cs.2023.33
About This Article
Copyright
Data & Comments
Data
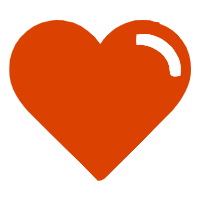

Comments
Comments must be written in English. Spam, offensive content, impersonation, and private information will not be permitted. If any comment is reported and identified as inappropriate content by OAE staff, the comment will be removed without notice. If you have any queries or need any help, please contact us at support@oaepublish.com.